Topic overview
Production orders are the basic element of the production process. They can be created manually, generated based on material requirements planning, or downloaded into the system through data import.
The action dispatching a production order may be performed in the following applications:
- Production orders
- Cockpit: Production orders – for multiple orders simultaneously
- Production recommendations
Dispatching production processes involves creating required material, operation, and resource reservations. The system dispatches bills of material, routings, and bills of resources selected for a given production item.
The scheduling of all capacity- and material-related elements is performed according to a selected scheduling model defined for a given production order.
The user can only dispatch production items that have the status Released. The item status can be verified in the Items application → Production view → Utilization status field. Items that are blocked or marked for deletion cannot be dispatched.
When a production order is dispatched with the use of the [Select action] → [Dispatch] button, the following actions are performed:
- Material reservations are created for all released material items from the production order
- Co-product reservations are created for all released by-product items from the production order
- Resource reservations are created for all released operation resources
- Purchase orders are created for all external manufacturing operations
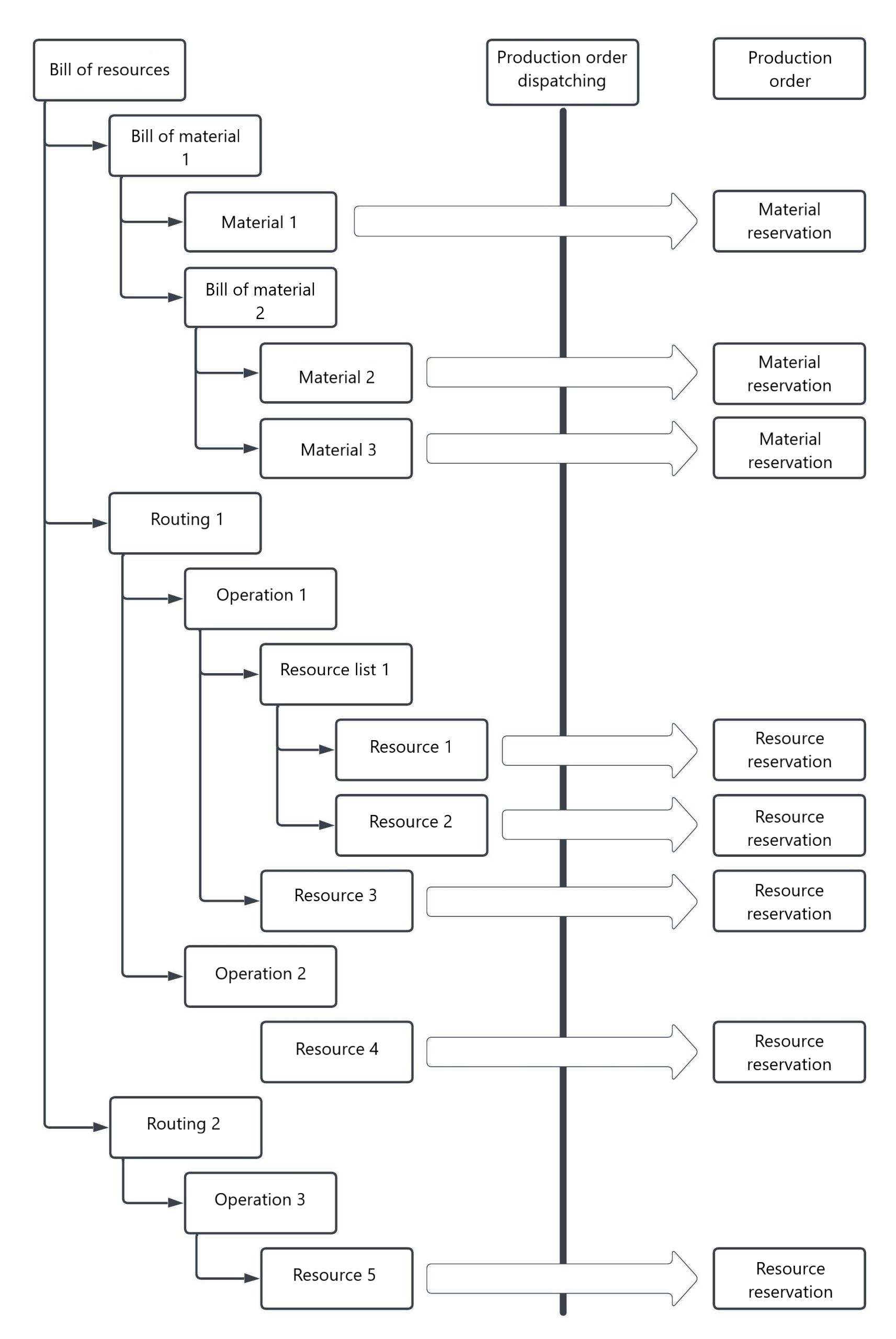
Details of the process of dispatching a production order
Dispatching a production order results in what follows:
- Dispatching an order with finite capacity takes precedence over defined dependencies in the production process structure.
- Finite capacity makes it possible to control the production order’s processing time, and thus the resource reservation’s time. Resource capacity can be defined in the applications Resources, Operations, and Routings. With regard to a resource’s capacity level for dispatching, it is possible to use the following calculations, according to the alert below, when initiating a dispatching operation:
- Calculation of the resource’s capacity level based on operation and routing data. In this case, capacity defined for the resource in the Resources application is ignored. Capacities defined for resources in the mentioned applications are multiplied upon dispatching.
- Calculation of the resource’s capacity level based on the resource’s base data, an operation, and a routing. Upon dispatching, all capacities will be appropriately multiplied.
- Dependencies defined for routings affect transport times and buffer times, if these are also used as part of an operation.
- Production structures used are always determined based on a date defined in the Dispatching date field on the Dispatching tab of the Production orders application. If production data versioning is active, only the versions that are or have been released within a defined period are used. It refers to bills of material, (external manufacturing) operations, routings, and bills of resources.
- If co-products have not been assigned to an operation in the Bills of resources application, their production will begin upon ending a production order
- In the case of external manufacturing operation items, the system verifies whether a purchase order has already been created or whether the goods have already been received. If the purchase order has been generated or the receipt of materials has been posted for a given order item, the original purchase order item is retained and must be canceled manually or appropriately corrected as part of an order correction.
- If a resource group is assigned to an operation, upon dispatching a production order, the system automatically selects an available resource from the group. In the case of resource groups, the system always uses finite capacity, regardless of the selected scheduling type.
- A capacity profile is determined according to a holiday model assigned to a relevant time model. If no holiday model has been assigned to a week time model, holidays defined in the company calendar apply. Production capacity is not available on holidays.
- Warehouses:
- Receipts warehouse – it is the warehouse to which a manufactured item will be received. The warehouse’s data is retrieved from:
- The header of the Bills of material application
- The Production data section of the manufactured item in the Production view of the Items application
- The Production order types application
- Issues warehouse – it is the warehouse from which materials will be collected for production; it is entered along with a material reservation item or in the line item editor of a bill of material. For a co-product, it will act as a receipts warehouse.
- Receipts warehouse – it is the warehouse to which a manufactured item will be received. The warehouse’s data is retrieved from:
- Rejects percentage – it increases the quantity of reserved materials and decreases the quantity of co-products. The value is calculated according to the formula:
- The transport times of first operations are not considered in the case of single-level dispatching
- For each production order item, the system displays relevant conditions, formulas, and substitute functions in production structures (operations, routings, bills of material). The exception to this is buffer times.
- It is not possible to change or create new main conditions or substitute resources. Directly in order items, it is possible to edit only formulas, but not conditions.
- Formulas changed manually are taken into account upon the recalculation of dates and quantities started by selecting the button [Recalculate due date and quantity] in the Production orders application
- Buffer times are recalculated with the [Recalculate due date and quantity] action according to the maximum buffer time reduction set for an operation. The action is available under the [Recalculate due date and quantity] button in the Production orders application.
- Constraints for operations may be edited in the line item editor of the Production orders application. Constraints changed manually are taken into account upon the recalculation of dates and quantities started by selecting the button [Recalculate due date and quantity] in the Production orders application.
- Parameters may be edited in the line item editor of the Production orders application with regard to:
- Variable parameters defined for resources and resource groups in the Resources and Resource groups applications
- Operation parameters defined for operations in the Operations application
Parameters changed manually are taken into account upon the recalculation of dates and quantities started by selecting the button [Recalculate due date and quantity] in the Production orders application.
- Material reservation texts are transferred from the texts of bill of material items
- Operation item texts are transferred from the texts of routing items. If a text is missing, an operation’s header text is transferred.
- Resource reservation texts are transferred from the texts of operation items. If a text is missing, a text from a resource’s base data is transferred.
- Co-product item texts are transferred from the texts of bill of material items
- It is also possible to recalculate production order dates using the [Midpoint rescheduling] action. Performing the action has the following effects:
- Manual changes to quantities and target times are retained
- Capacity level remains unchanged
- Newly entered constraints are considered
- Changes to formulas and parameters are not considered
Scheduling categories and dispatching methods
Correct definition of scheduling in the Production orders application affects the determination of the processing time and due date of a production order. The following scheduling categories are distinguished:
- Forward without a capacity limit
- Forward with a capacity limit
- Backward without a capacity limit
- Backward with a capacity limit
Additionally, the following dispatching methods are distinguished:
- Single-level
- Multi-level
- Multi-level in order
From the connection of these, the following options can be selected for single-level dispatching:
- Forward single-level without a capacity limit:
- Based on a defined begin date, the (earliest possible) end date is calculated
- An order is dispatched as soon as possible at the expense of an idle period of co-products that are not on the critical path
- It does not take into account available resource capacities
- Backward single-level without a capacity limit:
- Dispatching as late as possible
- Minimum processing time
- Acceptance of employment gaps
- It does not take into account available resource capacities
- Based on a defined end date, the begin date is calculated
- A production order is dispatched as late as possible
- A bill of resources is processed from the last item
- Forward single-level with a capacity limit:
- It allows the earliest dispatching taking into account capacities of resources (regarding their use and reservations)
- Scheduling is performed based on an available resource capacity. Unavailability of materials does not affect scheduling.
- Based on a defined begin date, the end date is calculated
- Based on an entered begin date, due dates are calculated according to the earliest possible dates
- Idle times are accepted for co-products that are not on the critical path
- Backward single-level with a capacity limit:
- It allows the latest dispatching taking into account capacities of resources (regarding their use and reservations)
- Scheduling is performed based on an available resource capacity. Unavailability of materials does not affect scheduling.
- Based on an defined end date, the begin date is calculated
- Based on an entered end date, due dates are calculated according to the latest possible dates
The following variants are possible for multi-level dispatching:
- Forward multi-level (with or without a capacity limit)
- Backward multi-level (with or without a capacity limit)
- Forward multi-level in order (with or without a capacity limit)
- Backward multi-level in order (with or without a capacity limit)
Multi-level dispatching
Multi-level dispatching makes it possible to produce multi-level production structures while creating a single production order. The following multi-level dispatching types are distinguished:
- Multi-level dispatching – the system generates additional production orders for semi-finished goods that will be produced in order to cover the requirements of a production order being created. It is characterized by the following features:
- Begin and end dates of new production orders for semi-finished goods are determined according to the requirements of the superior production order
- When generating subsequent production orders, the system does not take into account lot data or planning data defined in the Items application
- If a superior production order is dispatched again, subordinate orders created in the course of the previous dispatching are deleted and, if there is no reporting regarding these orders, new ones are created
- Created subordinate orders are displayed on the standard Voucher references chain tab
- If the [Dispatch and release] action has not been selected, orders should be released separately
- Transport times are taken into account before initiating the operations of each subsequent production order
- Idle times before warehouse receipts are taken into account only at the end of the main production order
- Buffer times are always taken into account
- Multi-level dispatching in order – the system plans the entire production in a single production order. It retrieves data for semi-finished goods, importing it into the production order. It is characterized by the following features:
- Material and resource reservations are generated for the entire production structure
- Transport times are taken into account before initiating operations
- Idle times before warehouse receipts are taken into account only at the end of the production order
- Buffer times are always taken into account
Begin and end dates
Dispatching is connected with the definition of production order begin and end dates. Begin and end dates are used for calculations as base dates.
- In the case of backward scheduling, dispatching is handled according to capacity profiles from midnight of the previous day.
- In the case of forward scheduling, dispatching is handled according to capacity profiles from midnight of the current day.
Begin and end dates are taken into account or calculated in a different way, depending on the scheduling category and the production structures of a given production item:
- The default date for the earliest begin time is always the current date, i.e. today
- The default date for the latest end time is the maximum date, i.e. 31.12.9999
The methods of calculating begin and end dates are different, depending on the generation of production orders for production items that:
- Contain only a bill of material
- Contain a bill of material and a routing or bill of resources
Time calculations for production orders containing only a bill of material
For items containing only a bill of material, production times are calculated depending on the selected scheduling category:
- Backward scheduling with the latest end date specified:
- Entering the earliest begin date has no impact
- From a defined latest end date, the system deducts an item’s turnaround time; the result is the current begin date
- The current end date is the same value as a defined latest end date
- Backward scheduling with the latest end date not specified (i.e. with the date 31.12.9999 in the Latest end field):
- To a selected earliest begin date, the system adds an item’s turnaround time; the result is the current end date
- The current begin date is the same value as a defined earliest begin date
- Forward scheduling:
- Entering the latest end date has no impact
- To a defined earliest begin date, the system adds an item’s turnaround time; the result is the current end date
- The current begin date is the same value as a selected earliest begin date
Time calculations for production orders containing only a bill of resources
- Backward scheduling with the latest end date specified:
- Entering the earliest begin date has no impact
- The current end date is the same value as a defined latest end date
- The current begin date is calculated based on the current end date of a given production order
- Backward scheduling with the latest end date not specified (i.e. with the date 31.12.9999 in the Latest end field):
- To a selected earliest begin date, the system adds an item’s turnaround time; the result is the current end date
- The current begin date is calculated based on a given production order’s dispatch date
- Forward scheduling:
- Entering the latest end date has no impact
- The current begin date is the same value as a selected earliest begin date
- The current end date is calculated based on a given production order’s dispatch date