Operations application
In the Operations application, the user can define individual activities of the production process. The application is composed of a header and work pane. The work pane contains a table with the list of resources assigned to a given operation and a line item editor enabling the user to edit and enter data in the table.
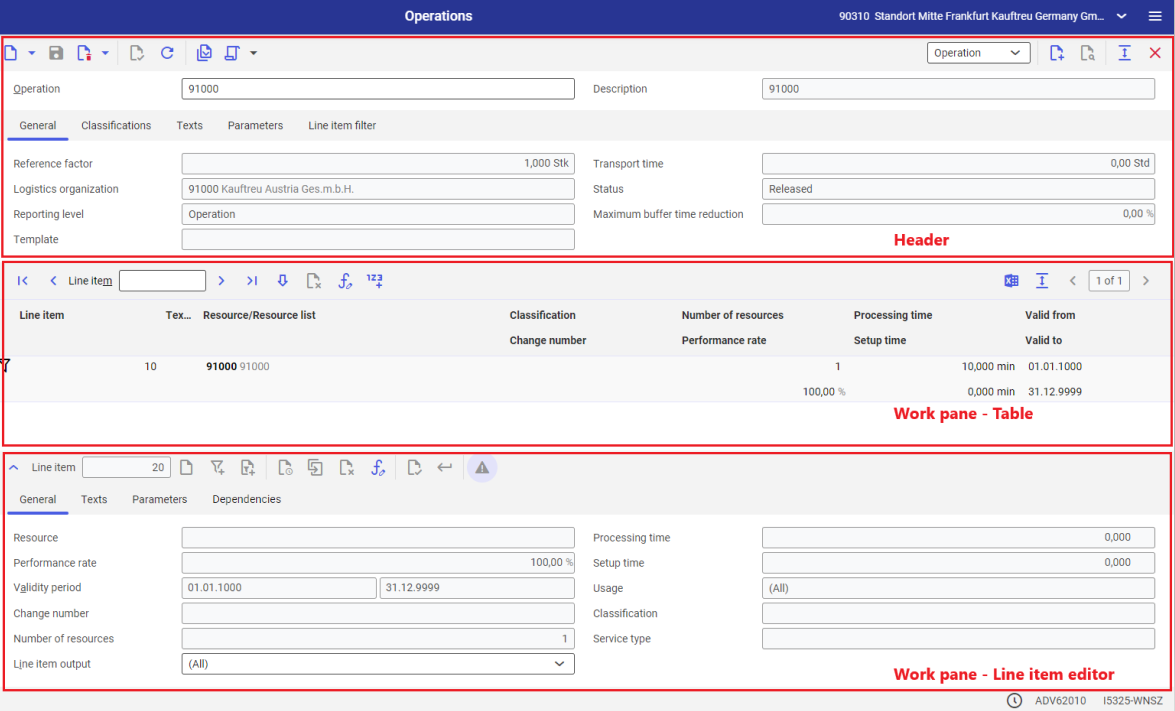
Header
The application header allows the user to add a new operation, edit an existing one, and release data for further processing. The header of the Operations application contains the following buttons:
- [New operation] → [Operation] – it makes it possible to add a new operation in the system
- [New operation] → [External manufacturing operation] – it makes it possible to define operations required by external manufacturing. After this button is selected, the work pane view changes accordingly. More information may be found in chapter Work pane – Adding an external manufacturing operation.
- [New operation] → [Multi-site production operation] – it makes it possible to define an operation to be carried out by the company but within another organization. More information may be found in chapter Work pane – Adding a multi-site production operation.
- [New operation] → [New from template] – it makes it possible to create a new operation on the basis of a previously created template. It opens the dialog window Generate and link.
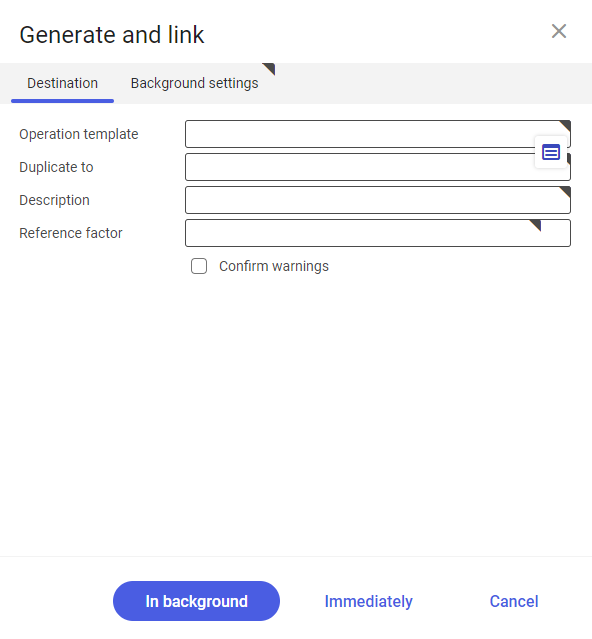
The dialog window is composed of two tabs: Destination and Background settings. The Destination tab contains the following fields:
- Operation template – a template defined in the Operation template application
- Duplicate to – it makes it possible to select operations the selected template is to be assigned to
- Description – an additional operation description
- Reference factor – a quantity for which the operation is to be defined
- Confirm warnings – a parameter enabling the automatic confirmation of warnings upon the generation of operations
The Background settings tab enables the user to define batch job parameters, including the job’s name, processing queue, application server, etc.
- [New operation] → [Duplicate] – it makes it possible to duplicate an operation. It is activated after selecting a defined operation.
- [New operation] → [New version] – it makes it possible to create a new version of an operation. It activates the field Valid from time point. The button itself is activated after selecting a defined operation.
- [Delete] – it makes it possible to delete an operation or mark/unmark it for deletion. If an operation is used in the Routings application, the system will not allow the user to delete it and will display a message indicating where it is used.
- [Check all line items] – it makes it possible to verify the correctness of data entered for all line items added in the operation table
- [Select action] → [Link to template] – it links a selected operation to a previously defined template
- [Select action] → [Separate from template] – it unlinks a selected operation from a template
- [Select action] → [Release version] – it accepts an operation for further processing
- [Select action] → [Edit version] – it changes the status of an operation version to In process. The button is activated after selecting [New operation] → [New version].
- [Select action] → [Approve version] – it changes the status of an operation version to Under approval. The button is activated after selecting [New operation] → [New version].
- [Select action] → [Lock version] – it prevents further use of an operation. Attempting to use a locked operation in the Routings application will display a relevant notification on the Messages tab.
Buttons belonging to the [Select action] group are activated after saving a defined operation.
- Drop-down context menu for views – it makes it possible to select one of the following views:
- Operation – this view enables the user to define a new operation
- Tree view – this view enables the user to preview an operation in the form of a tree structure with defined levels and associated elements of a given production process, defined on the basis of data entered in the Operation view
The application header contains the following fields:
- Operation (required) – an operation name, short identification description
- Description (required) – an additional operation name that can be defined in different languages
- Valid from time point – it makes it possible to define a date from which an operation is to be valid. The field is grayed-out and becomes active only after creating a new operation with the button [New operation] → [New version].
- [Back] and [Next] buttons – they make it possible to switch between operation versions.
General tab
The General tab allows the user to enter basic data defining an operation; it contains the following fields:
- Reference factor – it is used to define a quantity (to be produced) to which the details of assigned resources, resource groups, or resource lists refer
- Transport time – it adds a defined transport time to the operation time
- Logistics organization – an organization used for bill of resources data. By default, an organization selected in the toolbar is used in this field.
- Status – an operation processing status. The status changes accordingly after selecting the button [Select action]. The status affects the possibility to use an operation in further processes. The following statuses are available:
- In process – the operation is currently edited
- Released – the operation is approved and accepted for further use
- Blocked – the operation is blocked and cannot be used
- Expired – this status is assigned to an operation version if a newer version is created with the button [New operation] → [New version].
- Under approval – this status is assigned to an operation that requires the verification of data correctness
- Reporting level:
- Operation – operation reporting is carried out at the level of work
- Resource – operation reporting is carried out at the level of resources added to a given operation
- Maximum buffer time reduction – in this field, it is necessary to enter the percentage value of the maximum buffer time reduction. Buffer time reduction is a production process optimization method allowing flexible buffering times. This feature makes it possible to determine a buffering time reduction limit that can be managed in the Production orders application or during production planning.
- Template – exactly one template can be assigned to an operation. However, a single template may be used for purposes of multiple operations. It is possible to save an operation with no template assigned. An operation created from a template is duplicated along with all resource line items.
Classifications tab
It enables the user to assign an operation to classifications created in the application Classifications → Bill of resources classification. Operations can be assigned to the following classifications:
- Classification 1 – Bill of resources classification 1
- Classification 2 – Bill of resources classification 2
- Classification 3 – Bill of resources classification 3
- Classification 4 – Bill of resources classification 4
- Classification 5 – Bill of resources classification 5
Texts tab
It makes it possible to add a description/text to an operation.
Parameters tab
This tab allows the user to adjust additional operation parameters. A parameter can be the quantity of produced items or the production time for a given item. It is also possible to define parameters that could be used to build formulae or usage conditions for a given operation in the Routings application.
The Parameters tab contains the following buttons:
- [Properties] – it makes it possible to define an editable field. The function may be used to build a template if information in the header is not sufficient enough for the organization. The user can be used after at least one parameter has been defined.
- [New] – it makes it possible to add a new parameter
- [Delete] – it makes it possible to delete defined parameters
- [Arrange] – it makes it possible to adjust the view of parameters in columns
Line item filter tab
It makes it possible to filter table line items. Available filters include:
- Validity – it makes it possible to filter table data by validity date. By default, the field is assigned the value today.
- Line item classification – it makes it possible to filter table data by data classification
- Change number – it makes it possible to filter table data by change number
Work pane – Adding an operation
Resources are assigned to an operation in the table. The first resource assigned to an operation (and given the lowest line item number) is defined as the base resource. Operation line items (resources, resource groups, and resource lists) are saved individually in the line item editor.
The table contains the following buttons:
- [Edit] – it makes it possible to change line item data in the line item editor
- [Mark/unmark for deletion] – it makes it possible to delete a resource from the table. A line item marked for deletion is deleted from the table after saving changes.
- [Edit condition with substitute or formula of selected line item] – it makes it possible to edit defined formulae and usage conditions of a resource
- [Renumber] – it makes it possible to change the numbering method for a line item in the table
- [Output pages already displayed into file] – it exports table data into an XLS file
The following fields are available in the operation line item table:
- Icons in the column headers:
Resources
Resource groups
Resource lists
Line item to be deleted
Line item to be edited/unsaved line item
- Line item – it displays a number assigned to a line item in the table
- Text note – it displays an appropriate icon if a text has been assigned to a line item in the line item editor on the Texts tab
- Resource/Resource list – it displays the name of a resource, resource group, or resource list entered in the table
- Classification – it displays the classification of a table line item
- Change number – it displays a number used in a bill of material, routings and work elements or resource lists to enable the registration of changes
- Number of resources – it defines the number of resources on which the operation can be performed simultaneously. It does not apply to resource lists for which the number of resources has been specified in the Resource lists application.
- Performance rate – a resource’s performance factor expressed as a percentage value, that is taken into account when planning production and reserving the resource’s operation time
- Processing time – an operation’s duration for a given resource
- Setup time – time needed to prepare a resource for operation
- Valid from/Valid to – a validity period of a given table line item
Work pane – Line item editor

This area makes it possible to edit a selected table line item or add a new one The area is composed of the tabs described below. The line item editor’s toolbar contains the following fields and options:
- Line item – it displays the number of the currently edited table line item or shows which item number is entered into the table when adding a new resource
- [New line item of current type] – it allows the user to add a new line item to the list according to the current type
- [New resource line item] – it allows the user to add a resource or resource group to an operation
- [New resource list line item] – it allows the user to add a resource list to an operation
- [New version] – it allows the user to add a new version of a given resource from the table. The button is activated after adding a resource to the table and editing it.
General tab
When adding a resource/resource group to the table, the General tab contains the following fields:
- Resource (required) – the name of a resource/resource group entered to the table
- Processing time – an operation’s duration for a given resource or resource group
- Performance rate – a resource’s performance factor expressed as a percentage value, that is taken into account when planning production and reserving the resource’s operation time
- Setup time – time needed to prepare a resource for operation
- Validity period (required) – the validity date of an added resource/resource group. By default, it is set as 01.01.1000 – 31.12.9999.
- Usage – it makes it possible to select a process in which a given resource is to be used:
- (All) – it selects all the following options
- Cost Accounting
- Planning
- Scheduling
- Change number – a number assigned in the Change numbers application. It allows grouping resources and resource groups.
- Classification – a classification number assigned to structure data. Data classifications are defined in the Classifications application. In order to add a classification to a resource added to an operation, it is necessary to add a bills of resources line item classification.
- Number of resources – it defines the number of resources on which the operation can be performed simultaneously.
- Service type – it is defined in the Service types application. It makes it possible to recalculate units and associate an operation with a cost center.
- Line item output – a document where a given line item is to be included upon export. The field makes it possible to select one of the following options:
- (All) – it selects all the following documents
- Production order slip
- Job ticket
- Material voucher
- Work document
- External manufacturing delivery
Texts tab
It allows the user to add a text/note to a line item.
Parameters tab
It allows the user to edit parameters defined previously in the Resources application in the Variable operation parameters field.
Dependencies tab
It makes it possible to associate line items assigned to an operation with each other. The Dependencies tab contains the following buttons:
- [New] – it defines a new line item dependency and adds a new row in the table below
- [Delete] – it deletes a defined line item dependency
- Predecessor exists – this parameter does not allow a resource to start without completing the work of the preceding resource. It cannot be activated for the first line item.
The table is composed of the following columns:
- Constraints – it makes it possible to define an association between line items; available options include:
- Begins no earlier than
- Begins after
- Begins parallel to
- Ends parallel to
- Ends no later than
- Begins overlapping with
- Reference line item
- Line item – it allows defining the number of a table line item to which a given constraint is to refer to, e.g. Begins no earlier than line item no. 10
- Predecessor – it always refers a condition to the previous table line item, e.g. Line item no. 20 begins no earlier than the predecessor (line item no. 10)
- Line item – it defines the number of a line item to which a condition is to refer. The field is only active if the option Line item has been selected in the Reference line item field.
- Overlap time – it determines the maximum overlap time between table line items
Work pane – Adding an external manufacturing operation
After selecting the button [New operation] → [External manufacturing operation], the work pane view changes accordingly. The view displayed is composed of:
- Header – it makes it possible to define basic data concerning an external manufacturing operation
- Work pane – it contains separate tabs where it is required to fill in necessary data to carry out a procedure related to an external manufacturing operation
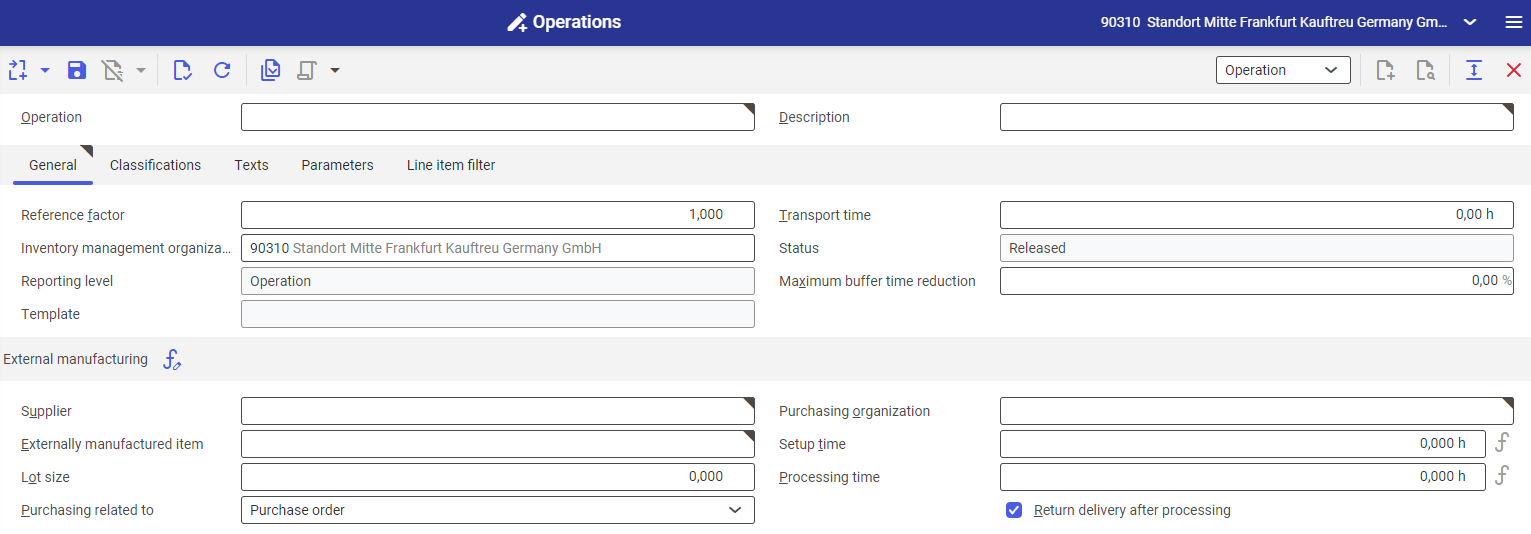
Header
The header of the dialog window contains the following fields:
- Operation (required) – an operation name, short identification description
- Description (required) – an additional operation name
- Valid from time point – it makes it possible to define a date from which an operation is to be valid. The field is grayed-out and becomes active only after creating a new operation with the button [New operation] → [New version].
Work Pane
The work pane displayed for an external manufacturing operation is composed of the following tabs:
General tab
The General tab makes it possible to define basic data concerning an external manufacturing operation. The tab contains the following fields:
- Reference factor – it is used to define a quantity (to be produced) to which the details of assigned resources, resource groups, or resource lists refer
- Transport time – it adds a defined transport time to the operation time
- Logistics organization – an organization used for bill of resources data. By default, an organization selected in the toolbar is used in this field.
- Status – an operation processing status. The status changes accordingly after selecting the button [Select action]. The status affects the possibility to use an operation in further processes. The following statuses are available:
- In process – the operation is currently edited
- Released – the operation is approved and accepted for further use
- Blocked – the operation is blocked and cannot be used
- Expired – this status is assigned to an operation version if a newer version is created with the button [New operation] → [New version].
- Under approval – this status is assigned to an operation that requires the verification of data correctness
- Reporting level:
- Operation – operation reporting is carried out at the level of work
- Resource – operation reporting is carried out at the level of resources added to a given operation
- Maximum buffer time reduction – in this field, it is necessary to enter the percentage value of the maximum buffer time reduction. Buffer time reduction is a production process optimization method allowing flexible buffering times. This feature makes it possible to determine a buffering time reduction limit that can be managed in the Production orders application or on the basis of buffer time reduction settings adjusted during production planning.
- Template – it may be used for several operations; however, only one template may be assigned to a single operation. An operation does not need to have a template assigned.
The External manufacturing section contains the following fields:
- Supplier (required) – a partner who is a subcontractor to an external manufacturing operation
- Purchasing organization (required) – a purchasing organization in the user’s organization
- Externally manufactured item (required) – created in order to enable delivery receipt in stock. Such an item is a semi-finished product from a supplier, used in an operation.
- Setup time – preparation time
- Lot size – the size of a lot sent to a subcontractor
- Processing time – an operation’s duration
- Purchasing related to – it makes it possible to define an ordering process through an operation.
- Purchase order – it automatically generates a purchase order for an external manufacturing operation
- Purchasing recommendation – it generates a purchasing recommendation that must be converted into a purchase order
- Return delivery after processing – this parameter makes it possible to define an item return to an internal process
Classifications tab
It enables the user to assign an operation to classifications created in the application Classifications → Bill of resources classification. Operations can be assigned to the following classifications:
- Classification 1 – Bill of resources classification 1
- Classification 2 – Bill of resources classification 2
- Classification 3 – Bill of resources classification 3
- Classification 4 – Bill of resources classification 4
- Classification 5 – Bill of resources classification 5
Texts tab
It makes it possible to add a description/text to an operation.
Parameters tab
This tab allows the user to adjust additional operation parameters. A parameter can be the quantity of produced items or the production time for a given item. It is also possible to define parameters that could be used to build formulae or usage conditions for a given operation in the Routings application.
The Parameters tab contains the following buttons:
- [Properties] – it makes it possible to define an editable field. The function may be used to build a template if information in the header is not sufficient enough for the organization. The user can be used after at least one parameter has been defined.
- [New] – it makes it possible to add a new parameter
- [Delete] – it makes it possible to delete defined parameters
- [Arrange] – it makes it possible to adjust the view of parameters in columns
Work pane – Adding a multi-site production operation
After selecting the button [New operation] → [Multi-site production operation], the work pane view changes accordingly. The view displayed is composed of:
- Header – it makes it possible to define basic data concerning an external manufacturing operation
- Work pane – it contains separate tabs where it is required to fill in necessary data to carry out a procedure related to an external manufacturing operation
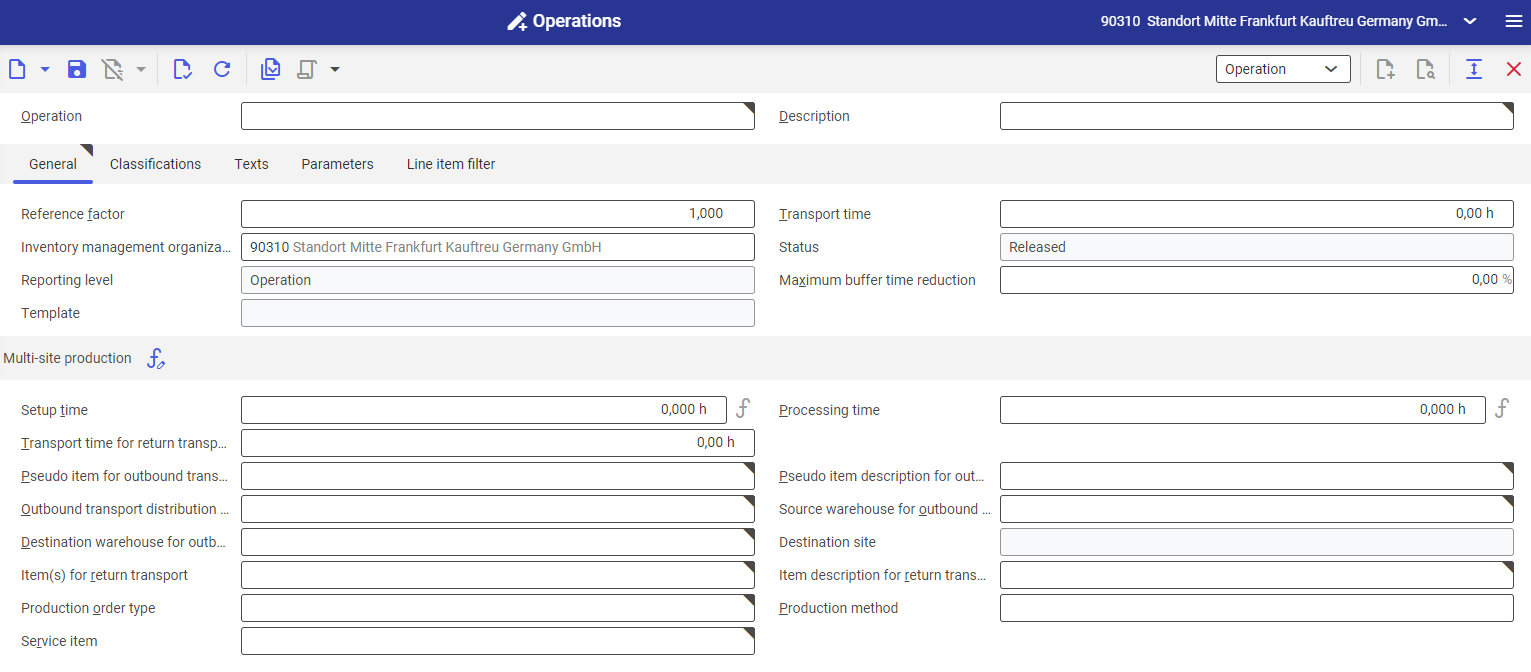
Header
The header of the dialog window contains the following fields:
- Operation (required) – an operation name, short identification description
- Description (required) – an additional operation name
- Valid from time point – it makes it possible to define a date from which an operation is to be valid. The field is grayed-out and becomes active only after creating a new operation with the button [New operation] → [New version].
Work pane
The work pane displayed for a multi-site production operation is composed of the following tabs:
General tab
The General tab makes it possible to define basic data concerning a multi-site production operation. The tab contains the following fields:
- Reference factor – it is used to define a quantity (to be produced) to which the details of assigned resources, resource groups, or resource lists refer
- Transport time – it adds a defined transport time to the operation time
- Logistics organization – an organization used for bill of resources data. By default, an organization selected in the toolbar is used in this field.
- Status – an operation processing status. The status changes accordingly after selecting the button [Select action]. The status affects the possibility to use an operation in further processes. The following statuses are available:
- In process – the operation is currently edited
- Released – the operation is approved and accepted for further use
- Blocked – the operation is blocked and cannot be used
- Expired – this status is assigned to an operation version if a newer version is created with the button [New operation] → [New version]
- Under approval – this status is assigned to an operation that requires the verification of data correctness
- Reporting level:
- Operation – operation reporting is carried out at the level of work
- Resource – operation reporting is carried out at the level of resources added to a given operation
- Maximum buffer time reduction – in this field, it is necessary to enter the percentage value of the maximum buffer time reduction. Buffer time reduction is a production process optimization method allowing flexible buffering times. This feature makes it possible to determine a buffering time reduction limit that can be managed in the Production orders application or on the basis of buffer time reduction settings adjusted during production planning.
- Template – it may be used for several operations; however, only one template may be assigned to a single operation. An operation does not need to have a template assigned.
- Setup time – preparation time
- Processing time – an operation’s duration
The Multi-site production section contains the following fields:
- Pseudo item for outbound transport (required) – a semi-finished product defined as a Pseudo item in the Items It is created to enable inventory management in the case of external production.
- Pseudo item description for outbound transport (required) – an additional description of a pseudo item
- Outbound transport distribution order type (required) – the way orders are passed between the company’s internal organizations, defined in the Distribution order types application
- Source warehouse for outbound transport (required) – a warehouse from which a product is retrieved for outbound transport
- Destination warehouse for outbound transport (required) – a warehouse to which a product is delivered
- Destination site (automatic) – it is defined automatically after the user selects a destination warehouse assigned to a given site
- Item(s) for return transport (required) – an item returning to the production process
- Item description for return transport (required) – an additional description of an item returning to the production process
- Production order type (required) – defined in the Production order types application
- Production method – a process defined in the Production methods application
- Service item (required) – a service defined in the Items application
Classifications tab
It enables the user to assign an operation to classifications created in the application Classifications → Bill of resources classification. Operations can be assigned to the following classifications:
- Classification 1 – Bill of resources classification 1
- Classification 2 – Bill of resources classification 2
- Classification 3 – Bill of resources classification 3
- Classification 4 – Bill of resources classification 4
- Classification 5 – Bill of resources classification 5
Texts tab
It makes it possible to add a description/text to an operation.
Parameters tab
This tab allows the user to adjust additional operation parameters. A parameter can be the quantity of produced items or the production time for a given item. It is also possible to define parameters that could be used to build formulae or usage conditions for a given operation in the Routings application.
The Parameters tab contains the following buttons:
- [Properties] – it makes it possible to define an editable field. The function may be used to build a template if information in the header is not sufficient enough for the organization. The user can be used after at least one parameter has been defined.
- [New] – it makes it possible to add a new parameter
- [Delete] – it makes it possible to delete defined parameters
- [Arrange] – it makes it possible to adjust the view of parameters in columns
Operation template application
The Operation template application makes it possible to create an operation template that could be duplicated when defining new production processes. The interface is the same as in the case of the Operations application. A created template can be used in the Operations application after selecting the button [New operation] → [New from template].