Introduction
The Product cost calculations application makes part of the Calculations module. By using the product cost calculations, through a defined calculation schema, the user can calculate item costs.
Within the product cost calculations, the items are priced on the basis of:
- Calculation schema
- Production process structures (bill of materials, routing)
- Production process
- Quantities (production lot size)
The product cost calculation allows for executing the following calculation types:
- Pre-calculations – calculation for a production item based on the data defined manually in the Product cost calculations application. The source of data is represented by defined production structures of the production item.
- Pre-calculation with order reference – the calculation is created in reference to the sales order and production order for a production item The source of data is represented by defined production structures of the production item.
- Pre-calculation with quotation reference – the calculation is created in reference to the sales quotation for a production item. Costs are calculated on the basis of the item production structure. The source of data is represented by defined production structures of the production item.
- Pre-calculations with service – calculation for a service based on the data defined manually in the Product cost calculations application.
- Production order calculations – costs are calculated in the same way as in the case of the pre-calculation, but the source of data is represented by the reservations of resources and materials created by selected production order
- Final calculation of the production order – costs are calculated on the basis of the actual time and quantities posted for the production order
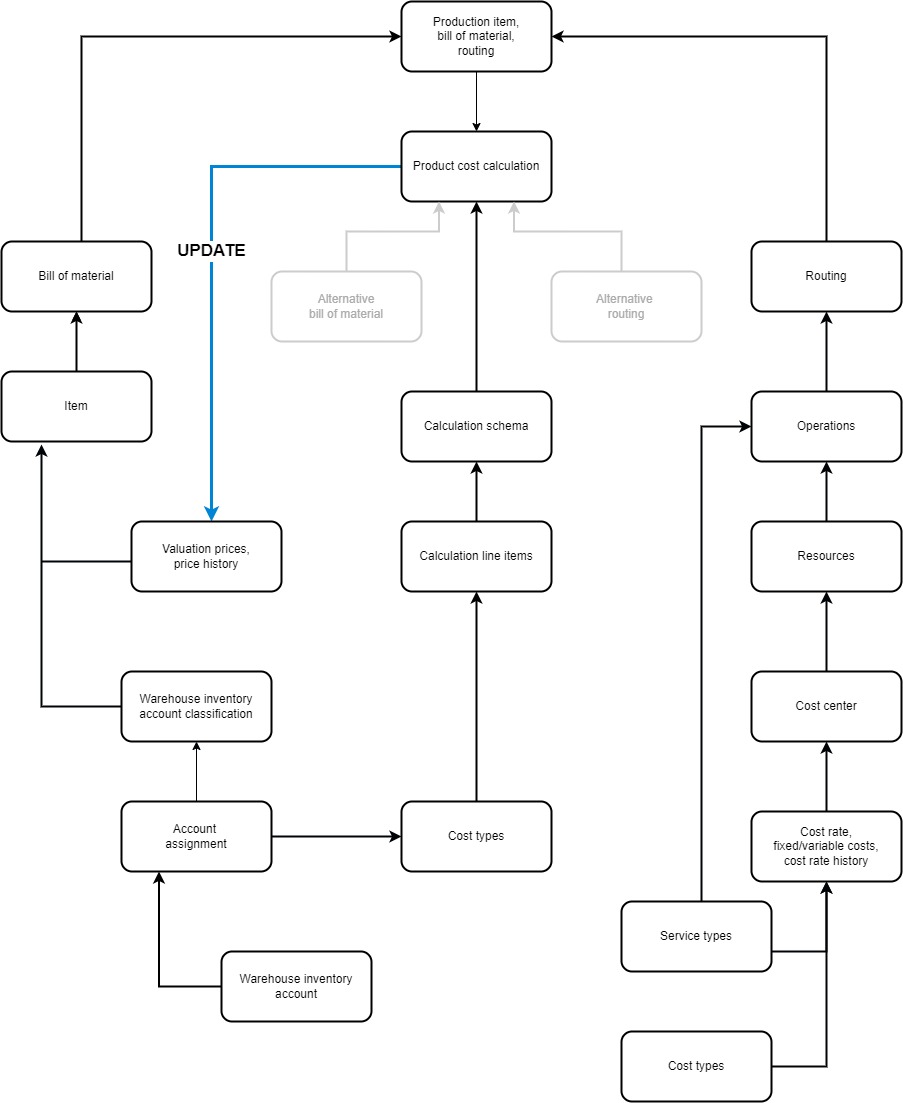
As a result of the product cost calculations, calculations of line items defined for a selected calculation schema are displayed in the Calculation results tab. Regardless of defined calculation schema, in the tab Calculation information, costs of the components of the production structure (materials, resources and operations), are displayed in a tree form.
In the product cost calculations, conditions, formulas and dependencies defined for the production process, are included.
The calculation can be executed for a configurable item, which makes it possible to calculate the price of a configurable item for the sales order with the use of the calculation.
Co-products generated in the production process are included in the calculation and displayed in the Co-products tab. The co-products produced in the production process can be semi-products for another production process or sales products. The system allows for distributing incurred production costs between co-products and production items.
The following cost are distinguished in the calculations:
- Material costs – they are retrieved from the application Items, Financials view. One of the following prices can be used for the calculation:
- Price1 to 5
- Inventory count price
- Average price – price retrieved for material pricing. It is the average value of the material pricing and gets automatically updated after each material receipt.
- Labor costs – they are defined on the basis of cost centers defined for the resources. The production structure is retrieved from routing or bill of resources. Partial or full costs are available depending on the settings in the Customizing application, function Controlling.
- External manufacturing costs – for it is possible to price an external manufacturing, an item of External manufacturing type must be created in the system. The external manufacturing item price is retrieved from the purchasing price list. The price list is determined on the basis of the supplier’s price list. The logics of calculation is the same as in the case of the material costs.
The Product cost calculations application is composed of the following elements:
- Identification pane – allows for defining the basic parameter for performed calculations
- Work pane – displays performed calculations and their results
Identification pane
The identification pane of the Product cost calculations allows for defining the settings for the calculation method. Besides the standard buttons, on the identification pane bar, the following buttons are available:
- [Add] → [Duplicate header] – allows for creating new calculation through copying the settings of the header of an existing product cost calculation
- [Select action] → [Calculate] – performs calculations in order to create or update calculations in accordance with formulas defined in the calculation schema. This action can be repeated Once it is selected, the Update item prices dialog window is displayed.
The Update item prices dialog window allows for defining the settings regarding calculations. The following tabs, fields and parameters are available:
- Tab Parameters – allows for defining the settings for item price calculation. The following fields and parameters are available:
- Validity period – for calculation purposes, production structures valid in a defined period, are retrieved. By default, the field assumes the current date and hour.
- Employee responsible – allows for defining the employee responsible for a given calculation. The employee must be an internal employee assigned to the organization (firm).
- Warehouse – allows for selecting the warehouse from which the data used for pricing materials will be retrieved. If it is not possible to determine the storage area on the basis of the calculation data, the prices are determined on the basis of:
- Storage area line item in the bill of material for the pre-calculation, pre-calculation in reference to order, pre-calculation in reference to quote
- Data of the production order for calculation order calculation and calculation of the actual cost of the production order
-
- Use valuation prices at warehouse level – if the parameter is checked, the prices are determined on the level of the storage areas. If no prices are available on the level of the storage areas, they are determined on the line item level.
- Create comparison of preliminary and final values – if the parameter is checked, the calculation of the final cost of the production order will be compared with the calculation of the production order. The parameter is available only for product cost calculations of Final calculation of the production order value type.
- Reference type – allows for selecting the comparison type on the basis of which the calculation comparison will be executed. This field is available only for product cost calculations of Final calculation of the production order value type.
- Use valuation prices from history – if the parameter is checked, prices for the calculation are retrieved from the history of prices. For materials, this applies to the history of line item prices and for labor costs, this applies to the history of cost rates.
- Automatically confirm warnings – after checking this parameter, warnings generated during the calculation process will be automatically confirmed
The Batch settings tab allows for defining the settings for the task batch processing.
- [Select action] → [Update sales price] – sales price in a specific sales price list is updated. This action can be repeated With the use of this action it is possible to create new line item in the sales price list. The new line item for the sales price list is entered with the date on which the action was called. Once the action is selected, the Update sales price list dialog window is displayed. The action is available only if the product cost calculation has Confirmed status.
The Update sales prices dialog window allows for defining settings regarding the transferring of prices from the calculation to a selected price list. The following tabs, fields and parameters are available:
- Tab Parameters – allows for defining the settings regarding the transferring of a price to a price list. The following fields and parameters are available:
- Confirm warnings – if the parameter is checked, warnings related to the transferring of prices to a price list are automatically confirmed.
- Price level – allows for defining the level of price changes. The following options are available for selection: Item (the price will be changed for the item sales price list) and Item + Customer (the price will be changed for the item sales price list and for the customer)
- Valid from – date from which the price will be valid in the price list
- Valid until – date until which the price will be valid in the price list
The Batch settings tab allows for defining the settings for the task batch processing.
- [Select action] → [Update valuation prices] – valuation prices defined in the Items application (Financials view) are updated, including defined cost shares (in case there are co-items). The calculation row for which the price value will be retrieved, must be defined for the used calculation scheme. This action can be executed only one time. If necessary, the rounding function should be included. Otherwise, the rounding is made in accordance with decimal places of used currency. The action is available only if the product cost calculation has Confirmed status.
Update valuation prices dialog window
The dialog window is composed of the following fields and parameters:
- Update level – allows for selecting price update level. Available options:
- At item level
- At warehouse level
- Warehouse – allows for selecting the warehouse on the level of which valuation prices will be updated. If the action is carried out for a calculation of Calculation of the production order type or Final calculation of the production order, the field assumes the default value of the destination warehouse of the calculated production order.
- Create valuation price at warehouse level – if the parameter is checked, valuation prices are generated also for storage areas without defined price.
- [Select action] → [Update billing price] – the billing price is for a distribution order line item is updated. The action is available only if the product cost calculation has Confirmed status.
- [Select action] → [Release] – makes the calculation available for calculation purposes
- [Select action] → [Block] – blocks calculation
- View selection drop-down menu – allows for selecting product cost calculation type. Available values:
- Pre-calculation
- Pre-calculation with order reference
- Pre-calculation with quotation reference
- Calculation of the production order
- Final calculation of the production order value.
- Preliminary calculation with service item
Calculation view can be selected after defining the calculation type and clicking on the [Add] button.
In the identification pane, the following fields are available:
- Number – field divided into two sections. The first part of the filed allows for selecting calculation type on the basis of which the calculation will be defined in accordance with the settings in the Calculation types application. The second part of the field contains the calculation number assigned in accordance with the number range defined for the selected calculation type. The number can be also changed manually, if necessary, before starting or saving the calculation.
- Calculation status – symbol presenting calculation processing status. The following statuses are available:
- Entered – the basic data necessary for calculations has been entered and saved. The calculation has not been executed yet and it cannot be released.
- Released – the calculation has been released for further processing with the use of the Release action
- Created – the basic data necessary for calculations has been entered and saved.
- Calculated – calculations have been made; no errors have been detected
- Valuation prices updated – the price has been updated on the basis of the calculations. In case calculations are repeated, the status will change to Calculated.
- Incomplete – executed calculations has showed errors or the input data of the calculation has been changed. In case of changes of the calculation input data, to change the status it is necessary to repeat the Calculate action. Below, errors which might cause the Incomplete status, are presented:
- Inability to determine production structure costs, e.g., incorrectly assigned cost centers
- When distributing the production structure, it was impossible to determine formulas and conditions which made it impossible to determine precise production structure
- For a configurable item, it was impossible to determine configuration properties, which made it impossible to determine the production structure.
- Description – allows for entering the description of created calculation. It is freely defined by the user, that’s why several product cost calculations have the same description. In order to avoid a mistake and to ensure an easier identification, it is recommended to enter different descriptions.
- Calculation schema – allows for selecting the calculation schema which will be used for calculations. The field is filled-in automatically in accordance with selected calculation type. The system allows for changing the value. Once the Calculate action is executed, it is not possible to change the product costs for created calculation. Only calculation schemas with Released status can be used in calculations.
- Calculation date – allows for selecting the time point for which the calculation will be executed
- Production item – allows for selecting the production item for which the calculation will be executed The item must have the Production view created in the Items application. The item can be changed only for calculations not referring to other documents. e.g., Production order calculation. Once the Calculate action is executed, it is not possible to modify the field.
- Last calculation date – displays the date and the hour of the last execution of the Calculate action (this field cannot be edited).
- Calculation quantity – allows for defining the item quantity for which the calculation will be executed. If a pre-calculation without sales order or production order reference is created, [Additional data] is created, which allows for defining tree additional values of quantities for the calculation. For the values, separate pre-calculations and comparison are generated. The calculations for additional values and the comparison are available in the voucher references chain. The actions for the calculation are available only from the pre-estimate with the base calculation quantity. Once the Calculate action is executed, it is not possible to modify the data. The quantity can significantly influence the result of the calculations. For quantity reasons, when solving production structure, it is possible to use other operations or resources which may cause different labor costs for a unit.