Topic overview
Production orders are the most important element of the Production framework. They are the result of data collected from such applications as Bills of material, Operations, Resources, Routings, and Bills of resources. Based on input data, a production order generates allocations for production and reserves defined resources or materials. Also, it enables production planning to deliver items to customers within a required period.
Production orders application
The Production orders application is composed of:
- Header – it contains function buttons, a description, and additional resource list settings
- Work pane – it is divided into:
- Table – it contains the reservations of resources and materials for production purposes
- Line item details – it allows previewing the data of table line items
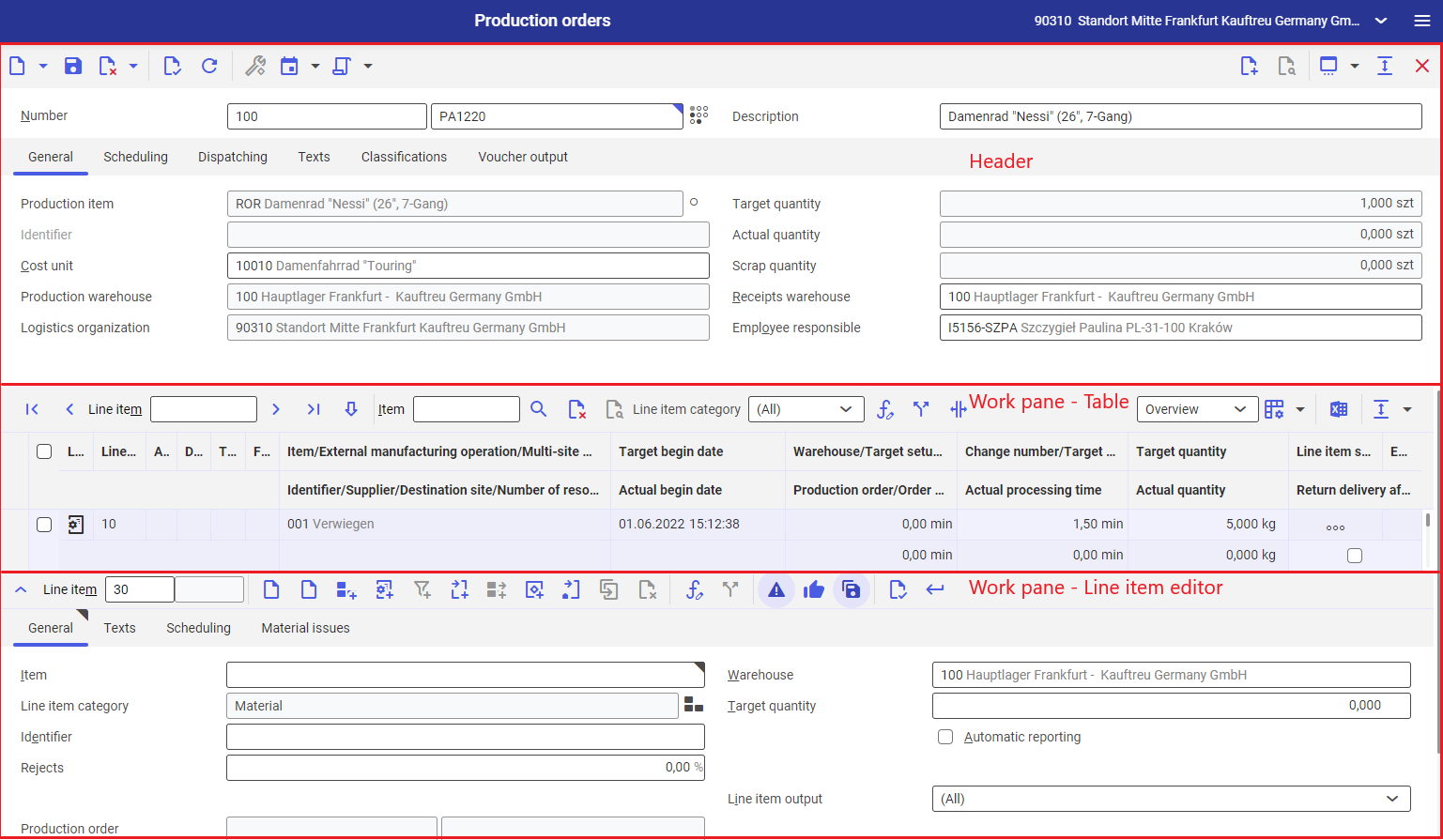
Header
Buttons available in the application header:
- [New] – it makes it possible to add a new production order. An order can be created after entering a production order type in the Number field.
- [New] → [Duplicate header] – it makes it possible to copy the header of a production order to once again initiate the production of an item defined in the Production item field.
- [Delete] – it makes it possible to immediately delete a production order if it has not been dispatched yet. Otherwise, it allows marking/unmarking an order for deletion.
- [Configure item] – if a production item is configurable, this button may be used to define what configuration type is to be produced
- [Recalculate due date and quantity]:
- [Recalculate due date and quantity] – selecting the button opens the dialog window Change due date and/or quantity
- [Midpoint rescheduling] – selecting the button opens the dialog window Midpoint rescheduling
- [Select action]:
- [Dispatch] – it retrieves data for a production order if a bill of resources or a routing with a bill of material has been defined in settings. Also, it reserves materials and resources.
- [Dispatch and release] – it makes it possible to complete two steps at once – retrieve data and release a production order
- [Release] – it makes it possible to release a production order for further processing. The action is activated after dispatching the order.
- [Reserve inventory quantities] – it allows the manual reservation of inventory quantities of materials required in the production process
- [Set allocated quantities] – it allows allocating material quantities to a given production order. Such a production order must have the status Released and the option Use allocated quantities selected for its production order type. It is then possible to manually allocate materials using the Resource allocation application and post inventory quantities.
- [Generate picking orders and output picking slips] – it enables the user to export picking slips for materials. It only refers to cases where a material must be retrieved from a warehouse other than the production warehouse.
- [Output production documents] – it allows outputting production documents
- [Output production document copies] – it allows outputting production document copies. The action is activated after exporting original documents.
- [Calculate availability] – it allows the user to manually determine the availability of materials in warehouses; it will be displayed in the table
- [Delete line items] – it makes it possible to delete production order line items
- [Split order] – it makes it possible to split the processing of an order into separate parts
- [Block] – it blocks a production order
- [Complete order] – it processes all operations and material reservations, and changes the status of a production order to Completed
- [Generate/update distribution order for inter-company billing] – it allows settling a multi-site manufacturing operation
Fields available in the application header:
- Number (required) – the field is divided into two parts. The first part makes it possible to define a production order type. After defining the type and selecting the [New] button, a number is assigned to the new production order according to a defined number range.
- Order status – a dot symbol displaying the 8 statuses of a production order:
- Order status – it describes the current production order status
- Operation status – it describes the current execution status of an operation
- Material status – it describes the current status of material utilization
- Dispatch status – it describes the current execution status of a production order
- Production receipts – it describes the status of produced materials
- Output – it describes the status of documentation of a production order
- Material availability – it describes the current status of verification of material availability
- Picking order status – it describes if materials required for production have been released from the warehouse
- Description (required) – an additional production order name
Production orders application tabs
The application header is composed of the following tabs:
General tab

The tab defines production order master data. It contains the following fields:
- Production item (required) – an item to be ordered for production. In order to be processed with a production order, the item must have be assigned correct data in the Production view in the Items application.
- Target quantity (required) – an item quantity to be produced
- Identifier – the identifier of a production item. This option can be activated in the Items application (Inventory Management view) and defined in the Identifiers application.
- Actual quantity – an actual item quantity manufactured in the production process. The field retrieves data from the Operation postings application.
- Cost unit – it allows selecting a cost unit defined in the Cost units application
- Scrap quantity – a quantity of scrap produced
- Production warehouse – a warehouse where production takes place
- Receipts warehouse – a warehouse where a production item is to be stored
- Logistics organization – an organization responsible for inventory management, i.e. for material movements and warehouses
- Employee responsible – a person responsible for the processing of a production order. By default, it is the user entering the order into the system.
Scheduling tab

The Scheduling tab makes it possible to adjust production scheduling parameters. It contains the following fields:
- Scheduling category:
- Forward one level – an order’s end date is calculated based on its start date. This option does not take into account the need to produce semi-finished goods that are manufactured internally.
- Backward single-level – an order’s start date is calculated based on its end date. This option does not take into account the need to produce semi-finished goods that are manufactured internally.
- Forward multiple levels – an order’s end date is calculated based on its start date. This option takes into account the need to produce semi-finished goods that are manufactured internally. For this purpose, it creates additional production orders that include the production of the semi-finished goods.
- Backward multi-level – an order’s start date is calculated based on its end date. This option takes into account the need to produce semi-finished goods that are manufactured internally. For this purpose, it creates additional production orders that include the production of the semi-finished goods.
- Forward multiple levels in order – an order’s end date is calculated based on its start date. This option takes into account the need to produce semi-finished goods that are manufactured internally, adding them to the production order being created.
- Backward multi-level in order – an order’s start date is calculated based on its end date. This option takes into account the need to produce semi-finished goods that are manufactured internally, adding them to the production order being created.
- Buffer time reduction – a percentage value by which a buffer time will be reduced
- Use finite capacity – this parameter makes it possible to determine whether a given order is to take into account defined data related to the reservation of materials and resources
- Note resource reservation settings – if this parameter is active, the system enables using work time models including data defined in the Valuation of gaps as interruption field in the Resources application
- Earliest begin – it allows defining a start point for production order time calculations
- Current begin – it is displayed after dispatching a production order as the calculated, precise start time of the order
- Latest end – it allows defining an end point for production order time calculations
- Current end – it is displayed after dispatching a production order as the calculated, precise end time of the order
- Creation date – a production order’s creation date
- Completion date – a production order’s completion date
- Transitional goods receipt – it makes it possible to define a transition time following the completion of a production order
Dispatching tab

The Dispatching tab contains the input data of a given production process. It contains the following fields:
- Bill of resources – a bill of resources assigned to a production item, retrieved from the Items The field is filled in automatically after selecting the [Dispatch] action.
- Production method – it makes it possible to select an alternative production method if it has been previously defined in the Items application (Production view) for a given production item
- Bill of material – a bill of material assigned to a production item, retrieved from the Items application. The field is filled in automatically after selecting the [Dispatch] action.
- Routing – a production routing assigned to a production item, retrieved from the Items application. The field is filled in automatically after selecting the [Dispatch] action.
- Dispatching date – a production order’s dispatching date and time. The field is filled in automatically after selecting the [Dispatch] action.
- Delivery priority – it makes it possible to define a delivery priority from 0 (highest) to 8 (lowest). The field is for informational purposes only.
- Order priority – it makes it possible to define the priority of a production order. It allows defining an additional filter in applications of the Cockpit type.
Texts tab
The tab makes it possible to add a description/text to a production order.
Classifications tab
It enables the user to assign a production order to classifications created in the application Classifications → Production order classification. This allows the optimization of data management. Production orders can be assigned to the following classifications:
- Classification 1 – Production order classification 1
- Classification 2 – Production order classification 2
- Classification 3 – Production order classification 3
- Classification 4 – Production order classification 4
- Classification 5 – Production order classification 5
Voucher output tab
The tab contains a table with the list of voucher documents that will be generated once a given production order is dispatched. The table’s data can be adjusted in the application Customizing → Production → Documents. The table is composed of the following columns:
- Voucher document – the type of a voucher document exported for a production order
- Medium – the medium of export defined in the application Customizing → Production → Documents.
- Communication connection – the contact details of a person to which voucher documents are to be sent. It is possible to define multiple recipients; to do so, individual contact details should be separated with commas.
Work pane – Table
The table displays the reservations of required resources and materials, created to process a production order. Table data may be filled in automatically by selecting the button [Select action] → [Release] or entered manually with the use of the line item editor. When filled in automatically, the data is retrieved from the applications Bills of material and Routings or Bills of resources, provided that it is assigned to an item to be produced in the Items application (Production view).
The table contains the following buttons and fields:
- [Line item] – the ordinal number of a line item selected in the table
- [Edit line item] – it displays the details of a given line item in the line item editor
- Item – it displays the name of a selected item or allows entering an item name
- [Find item] – it allows searching an item in the table according to a name entered in the Item field
- [Set/remove deletion marker] – it allows setting/deleting a deletion marker for a table line item. Such a line item is deleted after saving a given production order. It is not possible to delete a table line item from a production order with the Completed status.
- Line item category – it makes it possible to filter table data. The following filters are available:
- (All) – it displays all line item categories
- Co-product – it displays co-products
- Equipment – it displays equipment
- External manufacturing operation – it displays external manufacturing operations
- Material provided to vendor – it displays materials provided to a vendor
- Material reservation – it displays material reservations
- Multi-site production operation – it displays multi-site production operations
- Operations – it displays operations
- Production item – it displays production items
- Resource reservation – it displays resource reservations
- [Edit condition with substitute or formula of selected line item] – it makes it possible to change formulas for a selected line item or create new formulas, defined in the Bills of material or Routings applications
- [Display list of alternative items] – it allows the user to select an alternative item for a material reservation line item, provided it has been defined in the Bills of material application. After the button is selected, a dialog window with available alternative items is displayed.
- [Split or replace operation] – it allows changing or editing an operation. Selecting the button displays the Split or replace operation dialog window, composed of two sections with the following fields:
- Current operation – it displays the data of an operation to be split or replaced:
- Operation – the name of the operation being edited
- Target quantity – the quantity of the operation being edited
- New operation – it displays the data of a new operation:
- New operation – the name of the new operation
- Target quantity – the quantity of the new operation
- Transfer material – it makes it possible to define whether the new operation should retrieve materials defined in a bill of materials
- Replace original operation – it makes it possible to define whether the new operation is to replace an operation displayed in the Current operation section
- Current operation – it displays the data of an operation to be split or replaced:
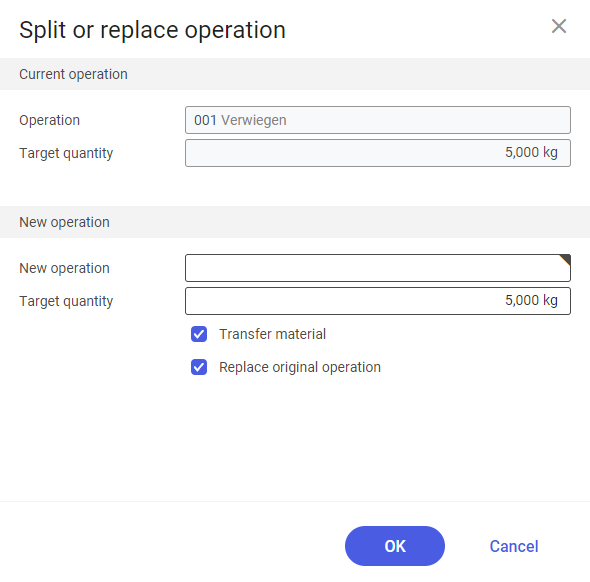
- View selection menu – it makes it possible to select a table view:
- Planning data – it displays planning master data in the table
- Overview – it displays additional data on material reservations
- [Output pages already displayed into file] – it exports table data into an XLS file
- Hide/show ranges:
- Hide/Show list header – it hides/displays table column titles
- Hide/Show line status – it hides/displays the first column the line statuses.
The production order table is composed of the following columns:
- Line item status:
Line item to be deleted
Line item to be edited/unsaved line item
- Select all – a parameter enabling the user to select table line items
- Line item category:
Material reservation
Resource reservation
Product
Operation
External manufacturing operation
External manufacturing material
Multi-site production operation
- Line item – ordinal numbers of line items
- Alternative item exists – the system displays the icon
if an alternative item exists
- Dependency exists – the system displays the icon
if there is a dependency defined for a line item
- Text note – texts – a line item note
- Formula exists – the system displays the icon
if there is a formula defined for a line item
- Item/External manufacturing operation/Multi-site manufacturing operation/Operation/Resource – the name of a line item defined in the table
- Identifier/Supplier/Destination site/Number of resources – it displays the following data:
- For items – identifiers
- For external manufacturing production – suppliers
- For multi-site production – organizations where production takes place
- For resources – the number of defined resources
- Target begin date – a planned start date for an operation/material picking
- Actual begin date – the actual start date of a picking operation, retrieved from a production report
- Warehouse/Target setup time – it displays the following data:
- For items – a warehouse where semi-finished products are stored
- For operations – a target setup time
- Production order/Order at destination site/Actual setup time – it displays the following data:
- For a semi-finished product – the number of a production order as part of which a given item is to be produced
- For operations – an actual setup time retrieved from a production report
- For multi-site operations – the number of a production order at a destination site
- Change number/Target processing time – it displays the following data:
- For items – a change number
- For operations – a target processing time
- Actual processing time – an operation processing time retrieved from a production report
- Target quantity – a planned material quantity to be produced as part of an operation or picked from a warehouse, depending on whether a given line item is an operation or material reservation
- Actual quantity – a quantity picked/produced, retrieved from a production report or material output job
- Line item status – it displays dot symbols designating stage statuses for a given production order line item
- External manufacturing status – it displays the processing status of an external manufacturing operation
- Return delivery after processing/Automatic reporting – it makes it possible to enable the features of automatic reporting after the processing of an operation or automatic return delivery after the processing of an external manufacturing operation. Changes in inventory levels will be generated automatically.
Additionally, if the Planning data view is active, the following columns are displayed:
- Available production warehouse quantity – a material quantity available in a warehouse
- Reservation status f. product. warehouse quantity
- Reserved quantity
- Reservation status for reserved quantity
- Open picking quantity – a quantity to be picked
- Allocated quantity – a quantity assigned to an order line item
Work pane – Line item editor
The work pane’s line item editor contains detailed data of table line items. It allows the user to preview line item details retrieved automatically for a production item from a bill of resources or a bill of material and a routing, or to manually enter data into the table. The editor’s toolbar contains the following fields and buttons:
- Line item – the field is divided into two parts which display a line item being edited along with its subitem, e.g. an operation’s resource
- [Create new basic item] – it allows adding a material reservation for a production order
- [New] – it allows adding a new line item of the previously edited/added category
- [Create new material line item] – it allows adding a material reservation to a production order
- [Create new operation line item] – it allows adding an operation reservation to a production order
- [Create new resource line item] – it allows adding a resource reservation to a production order. The button is activated after an operation is selected, since resources must be assigned to a specific operation.
- [New external manufacturing operation] – it allows the user to add an external manufacturing operation to a production order
- [New co-product] – it allows adding a new external manufacturing operation’s co-product to a production order. The button is activated after an external manufacturing operation is selected, since a given co-product needs to be assigned to that operation.
- [New internal external manufacturing operation] – it allows adding a new multi-site manufacturing operation
- [Duplicate] – it allows duplicating a production order line item
- [Set/remove deletion marker] – it allows setting/deleting a deletion marker for a line item. Such a line item is deleted after saving a given production order. It is not possible to delete a table line item from a production order with the Completed status.
- [Edit condition with substitute or formula of selected line item] – it makes it possible to edit formulas assigned to line items
- [Display list of alternative items] – it allows the user to select an alternative item for a particular material
- [Validate when accepting] – if the button is selected, data is validated when the [Accept] button is used
- [Save automatically when accepting and when change limit is reached] – if the button is selected, data is automatically saved when the [Accept] button is used
- [Validate] – it verifies the correctness of data entered in the line item editor
- [Accept] – it enters a given line item into the table
The work pane’s view changes according to the category of a line item added to a production order. The detailed description of each line item may be found in the following subchapters.
Work pane view for a new material line item
This view allows adding a material reservation to a production order. It is composed of the following tabs:
General tab
The tab contains basic information on a material reservation being added to the table. The tab contains the following fields:
- Item – the name of an item added to the table
- Warehouse – a warehouse from which an item is to be picked for a production order
- Line item category – the field is filled in automatically based on a line item being added to the table and displays the line item’s category
- Target quantity – a material quantity to be reserved for a production order
- Identifier – an item identifier defined in the Identifiers application
- Automatic reporting – if the parameter is selected, a given process will be automatically reported once it has been completed. The system will automatically retrieve materials for production and change inventory levels after the completion of a given production order.
- Rejects – the percentage value of material rejects
- Line item output – it allows selecting production order documents that will display a given line item. Available options include:
- (All)
- Production order slip
- Job ticket
- Material voucher
- Work document
- External manufacturing delivery
- Production order – if a given item is a semi-finished product and needs to be manufactured internally, the system will display the number of a production order assigned to the semi-finished product’s production process
- Replaced – if the [Split or replace operation] option is used for a given line item, this parameter will be selected automatically
- Current begin – an item’s picking date
Texts tab
The tab makes it possible to add a text note to a line item being added/edited.
Scheduling tab
The tab contains data related to the scheduling of a line item being added. It contains the following fields:
- Current begin – it displays the current start date for processing a production order line item
- Current end – it displays the current end date for processing a production order line item
- Earliest begin – the earliest start date defined for a line item, being a time limit for calculations performed as part of a production order
- Earliest end – the earliest end date defined for a line item, being a time limit for calculations performed as part of a production order
- Latest begin – the latest date defined for a line item, being a time limit for calculations performed as part of a production order
- Latest end – the latest end date defined for a line item, being a time limit for calculations performed as part of a production order
Work pane view for a new operation line item
This view allows adding an operation reservation to a production order. It is composed of the following tabs:
General tab
The tab contains basic information on an operation being added to the table. The tab contains the following fields:
- Operation – the name of an operation being added, defined in the Operations application
- Line item category – the field is filled in automatically based on a line item being added to the table and displays the line item’s category
- Target quantity – it allows defining an operation’s quantity
- Automatic reporting – if the parameter is selected, a given process will be automatically reported once it has been completed.
- Target setup time – a preparation time retrieved from resources assigned to an operation
- Target processing time – an operation’s duration retrieved from resources assigned to an operation
- Rejects – the percentage amount of rejects generated by an operation
- Line item output – it allows selecting production order documents that will display a given line item. Available options include:
- (All)
- Production order slip
- Job ticket
- Material voucher
- Work document
- External manufacturing delivery
- Transport time – it adds a defined transport time to the operation time
- Replaced – if the [Split or replace operation] option is used for a given line item, this parameter will be selected automatically
- Current begin – the date of operation execution
Texts tab
The tab makes it possible to add a text note to a line item being added/edited.
Scheduling tab
The tab contains data related to the scheduling of a line item being added. It contains the following fields:
- Current begin – it displays the current start date for processing a production order line item
- Current end – it displays the current end date for processing a production order line item
- Earliest begin – the earliest start date defined for a line item, being a time limit for calculations performed as part of a production order
- Earliest end – the earliest end date defined for a line item, being a time limit for calculations performed as part of a production order
- Latest begin – the latest date defined for a line item, being a time limit for calculations performed as part of a production order
- Latest end – the latest end date defined for a line item, being a time limit for calculations performed as part of a production order
- Fixed begin – it allows assigning a precise date and time to start processing a line item
- Fixed end – it allows assigning a precise date and time to end processing a line item
Parameters tab
The tab makes it possible to preview parameters defined for an operation being added.
Constraints tab
It makes it possible to associate line items assigned to a processing order with each other. The Constraints tab contains the following buttons:
- [New] – it defines a new line item dependency and adds a new row in the table below
- [Delete] – it deletes a defined line item dependency
- Predecessor exists – this parameter does not allow a resource to start without completing the work of the preceding resource. It cannot be activated for the first line item.
The table is composed of the following columns:
- Constraints – it makes it possible to define an association between line items; available options include:
- Begins no earlier than
- Begins after
- Begins parallel to
- Ends parallel to
- Ends no later than
- Begins overlapping with
- Reference line item
- Line item – it allows defining the number of a table line item to which a given dependency is to refer to, e.g. Begins no earlier than line item no. 10
- Predecessor – it always refers a condition to the previous table line item, e.g. Line item no. 20 begins no earlier than the predecessor (line item no. 10)
- Line item – it defines the number of a line item to which a condition is to refer. The field is only active if the option Line item has been selected in the Reference line item field.
- Line item number – it defines the number/name of a given item/operation
- Overlap time – it determines the maximum overlap time between table line items.
Work pane view for a new resource line item
This view allows adding a resource reservation to a production order. It is composed of the following tabs:
General tab
The tab contains basic information on resources being added to the table. The tab contains the following fields:
- Resource – the name of a resource/resource group entered into the table
- Number of resources – a resource quantity allocated to an operation
- Line item category – the field is filled in automatically based on a line item being added to the table and displays the line item’s category
- Target quantity – a quantity used by the system to define the required number of operation runs
- Target setup time – a resource’s preparation time
- Target processing time – an operation’s duration for a given resource
- Performance rate – a resource’s performance factor expressed as a percentage value, that is taken into account when planning production and reserving the resource’s operation time
- Service type – it is defined in the Service types application. It makes it possible to recalculate units and associate an operation with a cost center.
- Line item output – it allows selecting production order documents in which a given line item will be printed. Available options include:
- (All)
- Production order slip
- Job ticket
- Material voucher
- Work document
- External manufacturing delivery
- Current begin – the date of resource reservation by the production process
Texts tab
The tab makes it possible to add a text note to a line item being added/edited.
Scheduling tab
The tab contains data related to the scheduling of a line item being added. It contains the following fields:
- Current begin – it displays the current start date for processing a production order line item
- Current end – it displays the current end date for processing a production order line item
- Earliest begin – the earliest start date defined for a line item, being a time limit for calculations performed as part of a production order
- Earliest end – the earliest end date defined for a line item, being a time limit for calculations performed as part of a production order
- Latest begin – the latest date defined for a line item, being a time limit for calculations performed as part of a production order
- Latest end – the latest end date defined for a line item, being a time limit for calculations performed as part of a production order
- Valuation of gaps as interruption – it allows defining additional conditions for calculations. Available options include:
- Reservable with time interruption – it makes it possible to reserve a resource’s work time with a break during the execution of a job
- Reservable with interruption through work time model – it makes it possible to reserve a resource’s work time with a break according to a work time model defined for the resource in the Resources application
- Reservable without time interruption – it prevents reserving a resource’s work time with breaks
- Interruption-free reservation duration – it allows defining a method of reservation without breaks. Available options include:
- No time division – interruption-free duration reserved for a given resource
- Time division according to set up and processing time in operation – duration divided into individual component times of production order execution
Parameters tab
The tab makes it possible to preview parameters defined for a resource being added.
Constraints tab
It makes it possible to associate line items assigned to a processing order with each other. The Constraints tab contains the following buttons:
- [New] – it defines a new line item dependency and adds a new row in the table below
- [Delete] – it deletes a defined line item dependency
- Predecessor exists – this parameter does not allow a resource to start without completing the work of the preceding resource. It cannot be activated for the first line item.
The table is composed of the following columns:
- Constraints – it makes it possible to define an association between line items; available options include:
- Begins no earlier than
- Begins after
- Begins parallel to
- Ends parallel to
- Ends no later than
- Begins overlapping with
- Reference line item
- Line item – it allows defining the number of a table line item to which a given dependency is to refer to, e.g. Begins no earlier than line item no. 10
- Predecessor – it always refers a condition to the previous table line item, e.g. Line item no. 20 begins no earlier than the predecessor (line item no. 10)
- Line item – it defines the number of a line item to which a condition is to refer. The field is only active if the option Line item has been selected in the Reference line item field.
- Line item number – it defines the number/name of a given item/operation
- Overlap time – it determines the maximum overlap time between table line items.
Work pane view for a new external manufacturing operation
The view allows adding an external manufacturing operation to a production order. It is composed of the following tabs:
General tab
The tab contains basic information on an operation being added to the table. The tab contains the following fields:
- External manufacturing operation – the name of an external manufacturing operation
- Externally manufactured item – created in order to enable delivery receipt in stock. Such an item is a semi-finished product from a supplier, used in an operation.
- Line item category – the field is filled in automatically based on a line item being added to the table and displays the line item’s category
- Target quantity – a quantity to be processed by an operation in order to complete a production order
- Target setup time – it allows defining a time before and after an external operation
- Target processing time – a target order processing time
- Rejects – the percentage amount of rejects generated by an operation
- Line item output – it allows selecting production order documents that will display a given line item. Available options include:
- (All)
- Production order slip
- Job ticket
- Material voucher
- Work document
- External manufacturing delivery
- Purchasing related to – it makes it possible to define an ordering process through an operation. Available options include:
- Purchase order – it automatically generates a purchase order for an external manufacturing operation
- Purchasing recommendation – it generates a purchasing recommendation that must be converted into a purchase order
- Purchasing organization – a purchasing organization in the user’s organization
- Lot size – the size of a lot sent to a subcontractor
- Purchase order – the generated number of a purchase order document for an external manufacturing operation
- Return delivery after processing – this parameter makes it possible to define an item return to an internal process
- Transport time – it allows defining a transport time (if required)
- Supplier – a vendor who is a subcontractor to an external manufacturing operation
- Replaced – if the [Split or replace operation] option is used for a given line item, this parameter will be selected automatically
- Current begin – the date of operation execution
Texts tab
The tab makes it possible to add a text note to a line item being added/edited.
Scheduling tab
The tab contains data related to the scheduling of a line item being added. It contains the following fields:
- Current begin – it displays the current start date for processing a production order line item
- Current end – it displays the current end date for processing a production order line item
- Earliest begin – the earliest start date defined for a line item, being a time limit for calculations performed as part of a production order
- Earliest end – the earliest end date defined for a line item, being a time limit for calculations performed as part of a production order
- Latest begin – the latest date defined for a line item, being a time limit for calculations performed as part of a production order
- Latest end – the latest end date defined for a line item, being a time limit for calculations performed as part of a production order
- Fixed begin – it allows assigning a precise date and time to start processing a line item
- Fixed end – it allows assigning a precise date and time to end processing a line item
Parameters tab
The tab makes it possible to preview parameters defined for an operation being added.
Constraints tab
It makes it possible to associate line items assigned to a processing order with each other. The Constraints tab contains the following buttons:
- [New] – it defines a new line item dependency and adds a new row in the table below
- [Delete] – it deletes a defined line item dependency
- Predecessor exists – this parameter does not allow a resource to start without completing the work of the preceding resource. It cannot be activated for the first line item.
The table is composed of the following columns:
- Constraints – it makes it possible to define an association between line items; available options include:
- Begins no earlier than
- Begins after
- Begins parallel to
- Ends parallel to
- Ends no later than
- Begins overlapping with
- Reference line item
- Line item – it allows defining the number of a table line item to which a given dependency is to refer to, e.g. Begins no earlier than line item no. 10
- Predecessor – it always refers a condition to the previous table line item, e.g. Line item no. 20 begins no earlier than the predecessor (line item no. 10)
- Line item – it defines the number of a line item to which a condition is to refer. The field is only active if the option Line item has been selected in the Reference line item field.
- Line item number – it defines the number/name of a given item/operation
- Overlap time – it determines the maximum overlap time between table line items.
Work pane view for a new material provided to a vendor
The view allows adding a material provided to a vendor to a production order. It is composed of the following tabs:
General tab
The tab contains basic information on a material provided to a vendor being added to the table. The tab contains the following fields:
- Item – the name of an item added to the table. It must first be defined in the Items application.
- Warehouse – the site of a line item added to the list
- Line item category – the field is filled in automatically based on a line item being added to the table and displays the line item’s category
- Target quantity – a material quantity to be reserved for a production order
- Identifier – an item identifier defined in the Identifiers application
- Rejects – the percentage value of material rejects
- Line item output – it allows selecting production order documents that will display a given line item. Available options include:
- (All)
- Production order slip
- Job ticket
- Material voucher
- Work document
- External manufacturing delivery
- Production order – the number of a service production order
- Replaced – if the [Split or replace operation] option is used for a given line item, this parameter will be selected automatically
- Material provided to vendor by ordering party – it allows defining whether a material is an additional material required to complete an external manufacturing operation
- Current begin – the date of delivery of a material for external manufacturing
- Replaced – if the [Split or replace operation] option is used for a given line item, this parameter will be selected automatically
Texts tab
The tab makes it possible to add a text note to a line item being added/edited.
Scheduling tab
The tab contains data related to the scheduling of a line item being added. It contains the following fields:
- Current begin – it displays the current start date for processing a production order line item
- Current end – it displays the current end date for processing a production order line item
- Earliest begin – the earliest start date defined for a line item, being a time limit for calculations performed as part of a production order
- Earliest end – the earliest end date defined for a line item, being a time limit for calculations performed as part of a production order
- Latest begin – the latest date defined for a line item, being a time limit for calculations performed as part of a production order
- Latest end – the latest end date defined for a line item, being a time limit for calculations performed as part of a production order
Material issues tab
It makes it possible to define limitations to be followed by persons handling a material. It contains the following fields:
- Permit multiple inventory owners – it allows defining whether a given material is to be available for different organizations
- Inventory owner sequence – it allows defining the priority of organizations if there are multiple inventory owners
- Owners of inventory – an organization owning a given resource
Work pane view for a new co-product
This view allows adding a co-product to a production order. It is composed of the following tabs:
General tab
The tab contains basic information on a co-product being added to the table. The tab contains the following fields:
- Item – the name of an item added to the table. It must first be defined in the Items application.
- Warehouse – the target warehouse for a co-product
- Line item category – the field is filled in automatically based on a line item being added to the table and displays the line item’s category
- Target quantity – a co product’s quantity that will be produced as part of the production process
- Identifier – an item identifier defined in the Identifiers application
- Rejects – the percentage value of material rejects
- Line item output – it allows selecting production order documents that will display a given line item. Available options include:
- (All)
- Production order slip
- Job ticket
- Material voucher
- Work document
- External manufacturing delivery
- Transitional goods receipt –
- Current begin – an item’s picking date
Texts tab
The tab makes it possible to add a text note to a line item being added/edited.
Scheduling tab
The tab contains data related to the scheduling of a line item being added. It contains the following fields:
- Current begin – it displays the current start date for processing a production order line item
- Current end – it displays the current end date for processing a production order line item
Work pane view for an internal external manufacturing operation
The view allows adding an internal external manufacturing operation to a production order. It is composed of the following tabs:
General tab
The tab contains basic information on an operation being added to the table. The tab contains the following fields:
- Internal external manufacturing operation – the name of an internal external manufacturing operation being entered
- Line item category – the field is filled in automatically based on a line item being added to the table and displays the line item’s category
- Target quantity – a quantity to be processed by an operation in order to complete a production order
- Target setup time – it allows defining a time before and after an external operation
- Target processing time – a target order processing time
- Rejects – the percentage amount of rejects generated by an operation
- Line item output – it allows selecting production order documents that will display a given line item. Available options include:
- (All)
- Production order slip
- Job ticket
- Material voucher
- Work document
- External manufacturing delivery
- Transport time – it allows defining a transport time (if required)
- Current begin – the date of line item entry
- Replaced – if the [Split or replace operation] option is used for a given line item, this parameter will be selected automatically
Transport tab
- Transport time for return transport –
- Pseudo item for outbound transport – a semi-finished product defined as a Pseudo item in the Items application. It is created to enable inventory management in the case of external production.
- Pseudo item description for outbound transport – an additional description of a pseudo item
- Outbound transport distribution order type – the way orders are passed between the company’s internal organizations, defined in the Distribution order types application
- Source warehouse for outbound transport – a warehouse from which a product is retrieved for outbound transport
- Destination warehouse for outbound transport – a warehouse to which a product is delivered
- Destination site – it is defined automatically after the user selects a destination warehouse assigned to a given site
- Item(s) for return transport – an item returning to the production process
- Item description for return transport – an additional description of an item returning to the production process
- Production order type – defined in the Production order types application
- Production method – a process defined in the Production methods application
- Service item – a service defined in the Items application
- Order at destination site – the number of a production order at an organization responsible for a given process
- Order for outgoing transport – the number of a document associated with outgoing transport
Texts tab
The tab makes it possible to add a text note to a line item being added/edited.
Scheduling tab
The tab contains data related to the scheduling of a line item being added. It contains the following fields:
- Current begin – it displays the current start date for processing a production order line item
- Current end – it displays the current end date for processing a production order line item
- Earliest begin – the earliest start date defined for a line item, being a time limit for calculations performed as part of a production order
- Earliest end – the earliest end date defined for a line item, being a time limit for calculations performed as part of a production order
- Latest begin – the latest date defined for a line item, being a time limit for calculations performed as part of a production order
- Latest end – the latest end date defined for a line item, being a time limit for calculations performed as part of a production order
- Fixed begin – it allows assigning a precise date and time to start processing a line item
- Fixed end – it allows assigning a precise date and time to end processing a line item
Parameters tab
The tab makes it possible to preview parameters defined for an operation being added.
Constraints tab
It makes it possible to associate line items assigned to a processing order with each other. The Constraints tab contains the following buttons:
- [New] – it defines a new line item dependency and adds a new row in the table below
- [Delete] – it deletes a defined line item dependency
- Predecessor exists – this parameter does not allow a resource to start without completing the work of the preceding resource. It cannot be activated for the first line item.
The table is composed of the following columns:
- Constraints – it makes it possible to define an association between line items; available options include:
- Begins no earlier than
- Begins after
- Begins parallel to
- Ends parallel to
- Ends no later than
- Begins overlapping with
- Reference line item
- Line item – it allows defining the number of a table line item to which a given dependency is to refer to, e.g. Begins no earlier than line item no. 10
- Predecessor – it always refers a condition to the previous table line item, e.g. Line item no. 20 begins no earlier than the predecessor (line item no. 10)
- Line item – it defines the number of a line item to which a condition is to refer. The field is only active if the option Line item has been selected in the Reference line item field
- Line item number –
- Overlap time – it determines the maximum overlap time between table line items