Actions available in Production orders application are used to process a production order. Below is the description and the possibilities of the available buttons:
- [Recalculate due date and quantity]:
- [Recalculate due date and quantity] – opens a dialog window Change due date and/or quantity
- [Midpoint rescheduling] – opens a dialog window Midpoint rescheduling
- [Select action]:
- [Dispatch] – retrieves data to production order if a bill of resources or routing with a bill of material is specified under the settings. It also reserves materials and resources.
- [Dispatch and release] – retrieves data and releases a production order at the same time.
- [Release] – releases a production order for further processing. This action activates after dispatching the production order.
- [Reserve inventory quantities] – reserves manually inventory quantities for the materials necessary in the production process.
- [Set allocated quantities] – assigns material quantities to a specific production order. This is only possible for a Released production order with selected option Use allocated quantities available in the production order type. Only then is it possible to allocate materials using the Resource allocation application and post the inventory quantities.
- [Generate picking orders and output picking slips] – outputs picking slips for materials. This is applicable only when the material needs to be collected from a warehouse other than the production warehouse.
- [Output production documents] – prints production vouchers.
- [Output production document copies] – prints the copies of production vouchers. This action activates after exporting the source documents.
- [Calculate availability] – used to manually specify the availability of materials in warehouses. The specified availability is presented in the table.
- [Delete line items] – removes a line item from a production order.
- [Split order] – divides the processing of a production order into stages.
- [Block] – blocks a production order.
- [Complete order] – processes all operations and material reservations and changes the production order status to Processed.
- [Create/update distribution order for internal invoicing] – settles the in-house external production operation.
[Recalculate due date and quantity] → [Recalculate due date and quantity]
[Recalculate due date and quantity] – opens a dialog window Change due date and/or quantity.

The dialog window is composed of Parameters and Batch settings tabs. Fields available in the Parameters tab are following:
- Automatically confirm warnings – activates automatic acceptance of warnings.
- Target quantity – changes the quantity of the manufactures item, against which the production order will be recalculated.
- Move:
- Next – postpones the start date by the number of days specified against the defined reference date.
- Back – changes the start date by the number of days back against the defined reference date.
-
- To date – used to indicate a specific start date of a production order.
- Number of work days – if Next or Back option is selected in the Move field, it specifies the number of days by which the start date of a production order is to be postponed.
- Reference date – proposed date to which the start date of a production order is to be postponed. It is retrieved automatically from the Current begin field available in the Scheduling It can be specified when the To date option is selected in the Move field.
- Scheduling type – changes the mode of operation scheduling. Selectable options are:
- Forward – scheduling mode that starts production at the earliest possible date by reserving operations from the first one to the last one.
- Backward – scheduling mode that starts production at the latest possible date by reserving operations from the last one to the first one.
- Use finite capacity – determines whether to take into consideration available material and resource capacities.
- Note resource reservation settings – if selected, it is possible to use work models with data defined in the Resources application under Valuation of gaps as interruption
- Recalculate quantities and times – determines whether quantities and times are to be recalculated next time the production order is run.
- Use target quantities –
- Reset print status – specifies the document export proceedings.
- Reset – deletes published production order documents and generates new ones.
- No – maintains the previously published production order documents.
- According to order type – uses the settings from the Production order types application for the defined production order type.
- Include administration time – takes into account the production order preparation time for calculations.
In the Batch settings tab you can define the standard settings for processing a task in the background.
[Recalculate due date and quantity] → [Midpoint rescheduling]
[Midpoint rescheduling] – opens a dialog window Midpoint rescheduling.
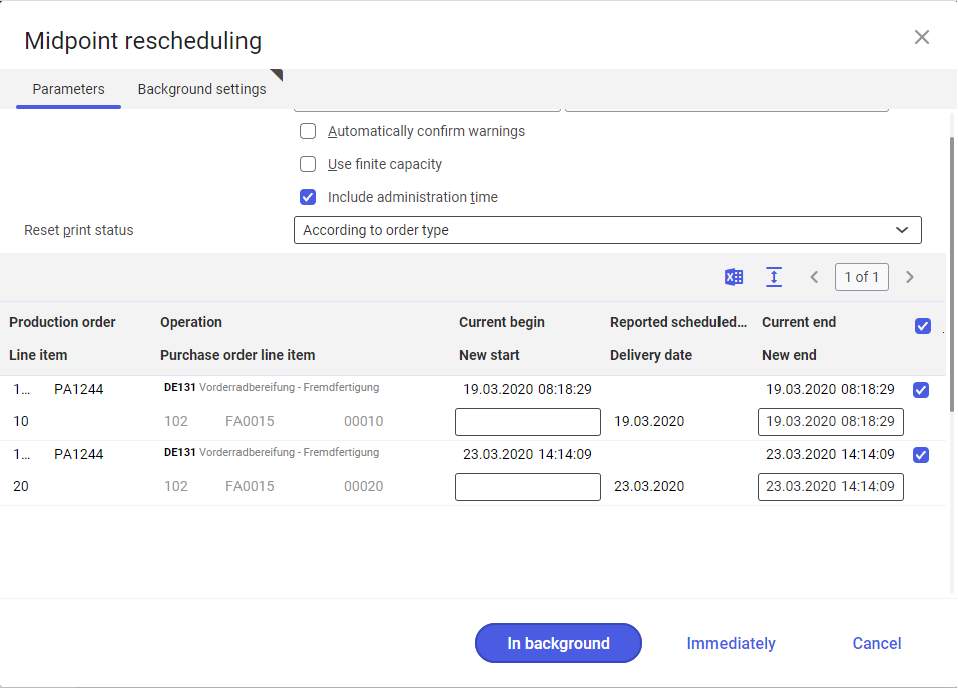
The dialog window is composed of the Parameters and Batch settings tabs.
The Parameters tab is composed of the following fields and a line item table:
- Order (automatically completed field) – represents the type and number of edited production order.
- Automatically confirm warnings – activates automatic acceptance of warnings.
- Use finite capacity – determines whether to take into consideration available material and resource capacities.
- Include administration time – takes into account the production order preparation time for calculations.
- Target quantity – changes the quantity of the manufactured item, against which the production order will be recalculated.
- Reset print status – specifies the document export proceedings.
- Reset – deletes published production order documents and generates new ones.
- No – maintains the previously published production order documents.
- According to order type – uses the settings from the Production order types application for the defined production order type.
- [Output pages already displayed into file] button – exports the table data to a file. The exported file format is XLS.
The line item table is composed of the following columns:
- Production order – displays the number and type of a production order.
- Line item – line item number in the table.
- Operation – operation name in the table.
- Purchase order line item – purchase order number. The line item contains data if external production operation is defined in a production order.
- Current begin – start date of a production order. Value of this field is retrieved automatically from a production order.
- New start – in this column you can specify a new start date of a production order.
- Reported scheduled start of operation – the actual operation start date, if it is already reported in a production order.
- Delivery date – material date of delivery to a supplier.
- Current end – end date of a production order. Value of this field is retrieved automatically from a production order.
- New end – in this column you can specify a new end date of a production order.
- Reschedule – allows the selection of operations to be rescheduled.
In the Batch settings tab, you can define the standard settings for processing a task in the background.
[Select action] → [Dispatch]
[Select action] → [Dispatch] – retrieves data to production order if a bill of resources or routing with a bill of material is specified under the settings. It also reserves the materials and resources. It opens the dialog window:
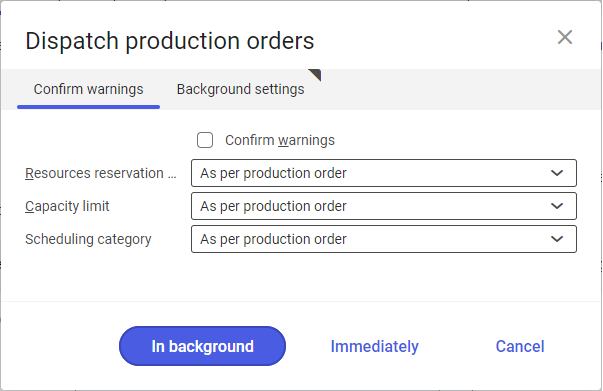
The dialog window is composed of Confirm warnings and Batch settings tabs. Following fields and parameters are available in the Confirm warnings tab:
- Confirm warnings – activates automatic acceptance of warnings.
- Resources reservation settings:
- Comply settings – reserves the resources according to the settings applied for resources in the line item editor.
- Ignore settings – ignores the settings applied for resources in the line item editor and in the production order under Scheduling
- As per production order – reserves resources according to the settings applied in a production order under Scheduling
- Capacity limit – specifies whether reservation is to take into account the resource capacity defined as a percentage of productivity.
- Use finite capacity – includes resource availability.
- Without capacity limit – does not include resource availability.
- As per production order – applies the value as defined in a production order under Scheduling
- Scheduling category – defines the production order planning process:
- Forward one level – order completion date is calculated on the basis of order start date. It does not include necessary production of internally manufactured semi-finished goods.
- Backward single-level – order start date is calculated on the basis of order completion date. It does not include necessary production of internally manufactured semi-finished goods.
- Forward multiple levels – order completion date is calculated on the basis of order start date. It does include necessary production of internally manufactured semi-finished goods. For this purpose, it creates additional production orders that include the production of semi-finished goods.
- Backward multi-level – order start date is calculated on the basis of order completion date. It does include necessary production of internally manufactured semi-finished goods. For this purpose, it creates additional production orders that include the production of semi-finished goods.
- Forward multiple levels in order – order completion date is calculated on the basis of order start date. It does include necessary production of internally manufactured semi-finished goods by adding them to the newly created production order.
- Backward multi-level in order – order start date is calculated on the basis of order completion date. It does include necessary production of internally manufactured semi-finished goods by adding them to the newly created production order.
- As per production order – applies the value as defined in a production order under Scheduling
In the Batch settings tab you can define the standard settings for processing a task in the background.
[Select action] → [Dispatch and release]
[Dispatch and release] – retrieves data and releases a production order at the same time. The buttons can be used to process further the production order via the above-described dialog window Dispatch production orders.
[Select action] → [Release]
[Release] – releases a production order for further processing. This action activates after dispatching the production order.
[Select action] → [Reserve inventory quantities]
[Reserve inventory quantities] – reserves manually inventory quantities for the materials necessary in the production process. It opens the Reserve inventory quantities dialog window.
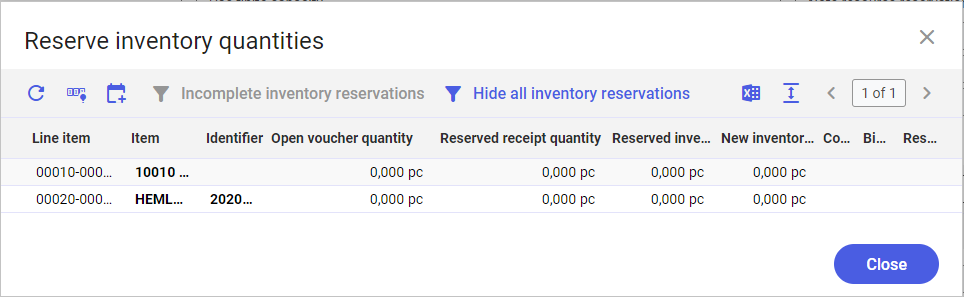
Following buttons are available in the dialog window:
- [Refresh] – refreshes data in the table
- [Set default reservation quantities for the column “New inventory quantity reservation”] – enters quantities necessary to process a production order into the column New inventory quantity reservation
- [Reserve] – reserves the quantities from the column New inventory quantity reservation
- [Incomplete inventory reservations] – filters the records for which no complete reservation has been created as specified in the column New inventory quantity reservation. The button activates upon selecting the [Reserve] button.
- [Hide all inventory reservations] – filters the records for which no complete reservation has been created.
- [Output pages already displayed into file] – exports the table data to a file. The exported file format is XLS.
The table in the dialog window is composed of the following columns:
- Line item – a line item number for the material is retrieved from the production order table.
- Item – item name
- Identifier – material identifier defined in Items application
- Open voucher quantity – production demand for material as specified in a production order
- Reserved receipt quantity – the quantity already processed by the production order
- Reserved inventory quantity – the quantity reserved in the warehouse to process a currently open production order
- New inventory quantity reservation – user-defined quantity to be reserved in the warehouse to the currently open production order.
- Binding unit – graphic visualization of unit as defined in Items application
- Reservation status – presents the material reservation status as a dot symbol:
- No material reservation
- Complete material reservation
- Incomplete material reservation: Entered manually
- No material reservation: Entered manually
- Complete material reservation: Entered manually
[Select action] → [Set allocated quantities]
[Set allocated quantities] – assigns material quantities to a specific production order. This is only possible for a Released production order with selected option Use allocated quantities available in the production order type. Only then is it possible to allocate materials using the Resource allocation application and post the inventory quantities.
[Select action] → [Generate picking orders and output picking slips]
[Generate picking orders and output picking slips] – outputs picking slips for materials. This is applicable only when the material needs to be collected from a warehouse other than the production warehouse.
[Select action] → [Output production documents]
[Output production documents] – prints production vouchers.
[Select action] → [Output production document copies]
[Output production document copies] – prints the copies of production vouchers. This action activates after exporting the source documents.
[Select action] → [Calculate availability]
[Calculate availability] – used to manually specify the availability of materials in warehouses. The specified availability is presented in the table.
[Select action] → [Delete line items]
[Delete line items] – removes a line item from a production order.
[Select action] → [Split order]
[Split order] – divides the processing of a production order into stages. It opens the Split order dialog window.
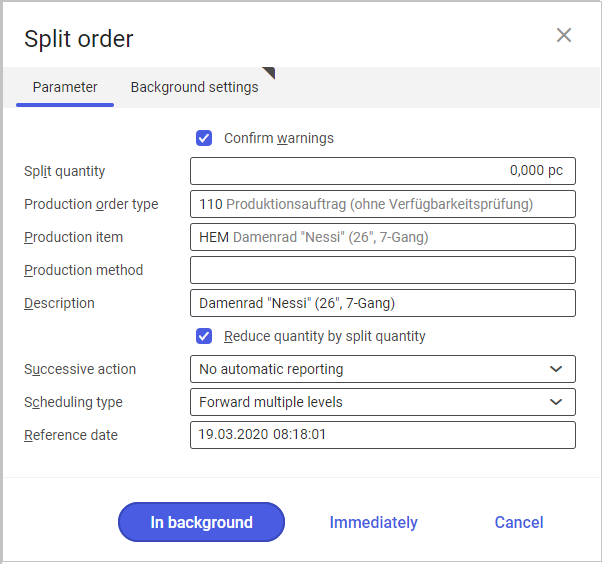
The dialog window Split order is composed of two tabs: Parameters and Background settings. Fields and parameters available in the Parameters tab are following:
- Confirm warnings – activates automatic acceptance of warnings.
- Split quantity – the quantity that will be defined for a new production order created as a result of splitting.
- Production order type – in this field you can select a production order type that will be created as a result of splitting.
- Production item – in this field you can select a production item for the new production order created as a result of a split.
- Production method – in case of using alternative production methods, in this field you can select one for the new production order created as a result of a split.
- Description – additional description of new production order created as a result of a split.
- Reduce quantity by split quantity – if selected, the quantity in a production order will be reduced by the value from the Split quantity field
- Successive action – in this field you can select one of the actions:
- No automatic reporting – none action is performed upon activation of order split.
- Dispatch – dispatches automatically the production order upon acceptance of order split
- Dispatch and release – dispatches and releases automatically the production order upon acceptance of order split
- Scheduling type – defines the process of planning a production order that will be created as a result of a split.
- Forward one level – order completion date is calculated on the basis of order start date. It does not include necessary production of internally manufactured semi-finished goods.
- Backward single-level – order start date is calculated on the basis of order completion date. It does not include necessary production of internally manufactured semi-finished goods.
- Forward multiple levels – order completion date is calculated on the basis of order start date. It does include necessary production of internally manufactured semi-finished goods. For this purpose, it creates additional production orders that include the production of semi-finished goods.
- Backward multi-level – order start date is calculated on the basis of order completion date. It does include necessary production of internally manufactured semi-finished goods. For this purpose, it creates additional production orders that include the production of semi-finished goods.
- Forward multiple levels in order – order completion date is calculated on the basis of order start date. It does include necessary production of internally manufactured semi-finished goods by adding them to the newly created production order.
- Backward multi-level in order – order start date is calculated on the basis of order completion date. It does include necessary production of internally manufactured semi-finished goods by adding them to the newly created production order.
- As per production order – applies the value as defined in a production order under Scheduling
- Reference date – reference date for new production order created as a result of a split.
In the Batch settings, tab you can define the standard settings for processing a task in the background.
[Select action] → [Block]
[Block] – blocks a production order.
[Select action] → [Complete order]
[Complete order] – processes all operations and material reservations and changes the production order status to Processed.
[Select action] → [Generate/update distribution order for inter-company billing]
[Generate/update distribution order for inter-company billing] – settles the in-house external production operation.