Topic overview
A bill of material (BOM) is one of the most important master data elements used in production. It is usually a table with the list of components that make up a manufactured part. It contains basic information about the materials used to produce the finished product. For the system, it is a data set that allows defining subsequent production/material usage operations.
The Bills of material application is composed of:
- Header – it contains function buttons, a description, and additional resource list settings
- Work pane – it is divided into:
- Table – it contains items or material lists assigned to a bill of material
- Line item editor – it allows adding and changing a line item selected in the table
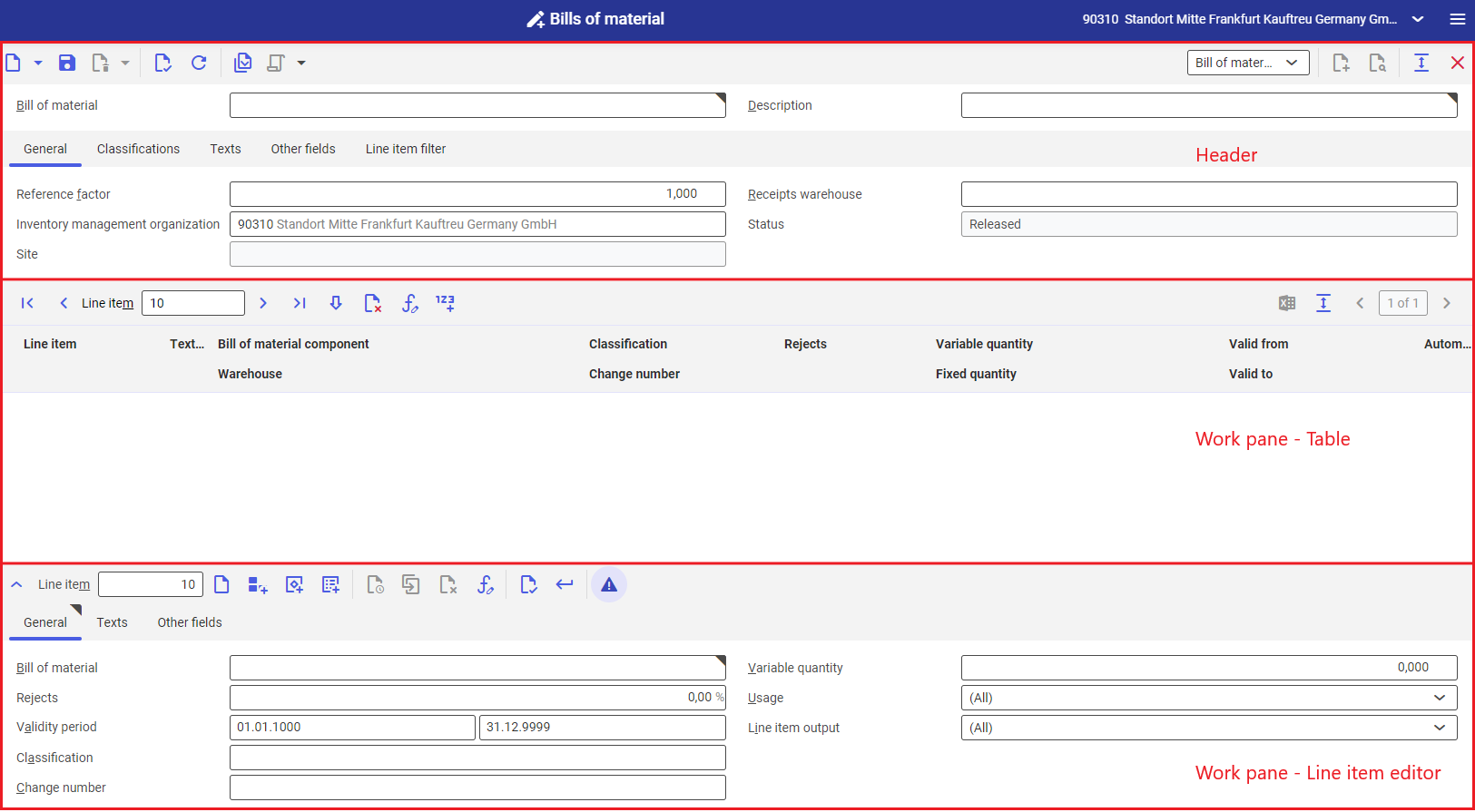
Header
Buttons available in the application header:
- [New] – it makes it possible to add, duplicate, or create a new version of a bill of material
- [Delete] – it makes it possible to set or remove a deletion marker
- [Select action] – it makes it possible to assign a status to a bill of material. The following actions are available:
- [Release version] – it accepts a bill of material and allows its usage
- [Edit version] – it restores the possibility to edit a bill of material
- [Approve version] – it assigns a status that requires the verification and confirmation of a bill of material
- [Lock version] – it prevents the usage of a bill of material
The fields in the header include:
- Bill of material (required) – the description/ID number of a bill of resources
- Description (required) – an additional bill of resources name.
- Valid from time point – the validity date and time of a bill of resources. The field is editable if a new version of an existing bill of material is created.
The application header is composed of the following tabs:
General tab
- Reference factor – it indicates the number of pieces of a target item that will be created after using a given bill of material
- Receipts warehouse – it indicates which warehouse will take receipt of a finished product created from a given bill of material
- Inventory management organization – it is an organization in which a given bill of material is defined. The field is filled in automatically with the data of an organization to which the user is assigned.
- Status (information field) – depending on the defined action, a bill of material may be assigned the following statuses:
- Released – it is accepted and ready to use
- In process – it is being edited/modified
- Under approval – it is to be checked
- Blocked – it cannot be used
- Site (filled in automatically) – it displays the organization of a defined receipts warehouse
Classifications tab
The tab makes it possible to assign a classification number for the purpose of data structuring. Data classifications are defined in the Classifications application. In order to add a classification to a bill of material, it is necessary to add a bills of resources classification.
Texts tab
The tab makes it possible to add a description/text to a bill of material.
Other fields tab
The tab makes it possible to adjust additional fields for a bill of material. An additional field may be used to enter data that is not provided in the system’s default tabs.
The tab contains the following buttons:
- [Properties] – it allows editing existing fields
- [New] – it adds a new field
- [Delete] – it makes it possible to delete defined field parameters
- [Arrange] – it makes it possible to adjust the view of fields in columns
- [Generate table schema] – it defines a field table schema, enabling the user to use such a schema
The number of fields defined for a bill of material is not limited.
Line item filter tab
It makes it possible to filter table line items. Available filters include:
- Validity – it makes it possible to filter table data by the validity date of a given resource. By default, it is set as today.
- Line item classification – it makes it possible to filter table data by item classification
- Change number – it makes it possible to filter table data by an item change number
- Item – it makes it possible to filter table data by a given item from the table
Work pane – Table
In the table, items are assigned to a bill of material.
The table contains the following buttons:
- [Edit] – it makes it possible to change line item data in the line item editor
- [Mark/unmark for deletion] – it makes it possible to delete a resource from the table. Line items are deleted from the table after saving changes.
- [Edit condition with substitute or formula of selected line item] – it makes it possible to edit defined formulas and usage conditions of a resource
- [Renumber] – it makes it possible to change the numbering method for a line item in the table
The following fields are available in the bill of material table:
- Icons displayed by table line items:
Semi-finished product
Material
Bill of material
Co-product
Line item to be deleted
Line item to be edited/unsaved line item
- Line item – a line item number (non-editable)
- Text note – a comment on a line item
- Bill of material component – the name of a line item added to a bill of material
- Warehouse – the site of a line item added to the list
- Classification – it displays the classification of a table line item
- Change number – it displays a number used in a bill of material, routings and work elements or resource lists to enable the registration of changes to defined line items
- Rejects – the percentage value of a material rejects quantity
- Variable quantity – a quantity depending on a quantity specified in a production order, required to manufacture a given product
- Fixed quantity – in the case of a fixed quantity defined for a line item, such a quantity is not recalculated after defining the quantity of a production order – quantities will always be assigned the same value
- Valid from/Valid to – line items may be determined in a time-dependent manner by using a time range defined in the column
- Automatic reporting – it enables automatic warehouse movements
Work pane – Line item editor
The line item editor makes it possible to edit a selected table line item or add a new one.
The following buttons and fields are available in the line item editor’s toolbar:
- Line item – it displays the number of the currently edited table line item or shows which item number is entered into the table when adding a new material
- [New line item of selected category] – it allows the user to add a new line item of the currently selected category
- [New material line item] – it allows the user to add a new item to a bill of material
- [New co-product line item] – it allows the user to add a co-product to a bill of material
- [New bill of material line litem] – it allows the user to add a bill of material to another bill of material – and thus create multi-level materials
- [New version] – it allows the user to add a new version of an existing material from the table. The button is activated after adding a material to the table and editing it.
- [Duplicate] – it allows the user to duplicate a material. The button is activated after adding a material to the table and editing it.
- [Edit condition with substitute or formula of selected line item] – it makes it possible to edit defined formulas and usage conditions of a material
- [Validate] – the feature verifies the correctness of entered data
- [Accept current line item] – it adds a newly defined line item to the table
- [Validate when accepting] – a selection button; once selected, data is validated when the [Accept current line item] button is used
Line item editor – [New material line item]
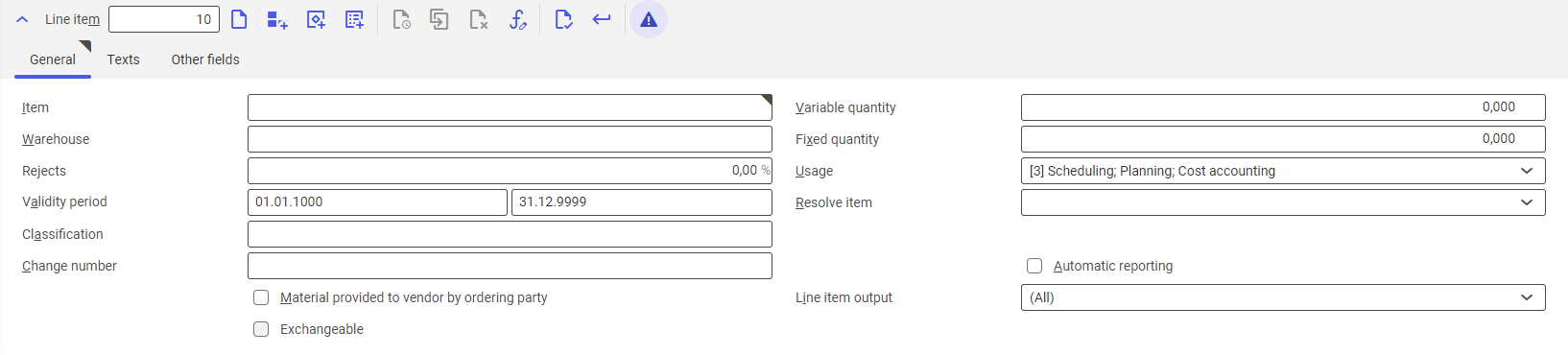
General tab
The following fields and parameters are available on the tab when adding a new material:
- Item – the name of an item added to the table. It must first be defined in the Items
- Variable quantity – a quantity depending on a quantity specified in a production order, required to manufacture a given product
- Warehouse – the site of a line item added to the list
- Fixed quantity – in the case of a fixed quantity defined for a line item, such a quantity is not recalculated after defining the quantity of a production order – quantities will always be assigned the same value
- Rejects – the percentage value of a material rejects quantity
- Usage – it makes it possible to select a process in which a given material is to be used:
- (All) – it selects all the following options
- Cost Accounting
- Planning
- Scheduling
- Validity period – the validity date of an added line item. By default, it is set as 01.01.1000 – 31.12.9999.
- Resolve item – it makes it possible to change the category of a line item. Line items affect production planning. If a line item is treated as a semi-finished good, the production order for a given bill of material will also plan the line item’s production.
- Resolve – it treats a material as a semi-finished good, that is a manufactured item
- Do not resolve – it treats a bill of material line item as a material
- Classification – a classification number assigned to structure data. Data classifications are defined in the Classifications In order to add a classification to a material added to a bill of material, it is necessary to add a bills of resources line item classification.
- Change number – a number assigned in the Change numbers It makes it possible to register changes to a line item.
- Automatic reporting – automatic feedback information displayed after completing a process. It is only available in the case of items.
- Line item output – a document where a given line item is to be included upon export.
Texts tab
It makes it possible to add a description/text to a line item.
Other fields tab
The tab makes it possible to adjust additional fields for an item. An additional field may be used to enter data that is not provided in the system’s default tabs.
The tab contains the following buttons:
- [Properties] – it allows editing existing fields
- [New] – it adds a new field
- [Delete] – it makes it possible to delete defined field parameters
- [Arrange] – it makes it possible to adjust the view of fields in columns
- [Generate table schema] – it defines a field table schema, enabling the user to use such a schema.
The number of fields defined for an item is not limited.
Line item editor – [New co-product line item]
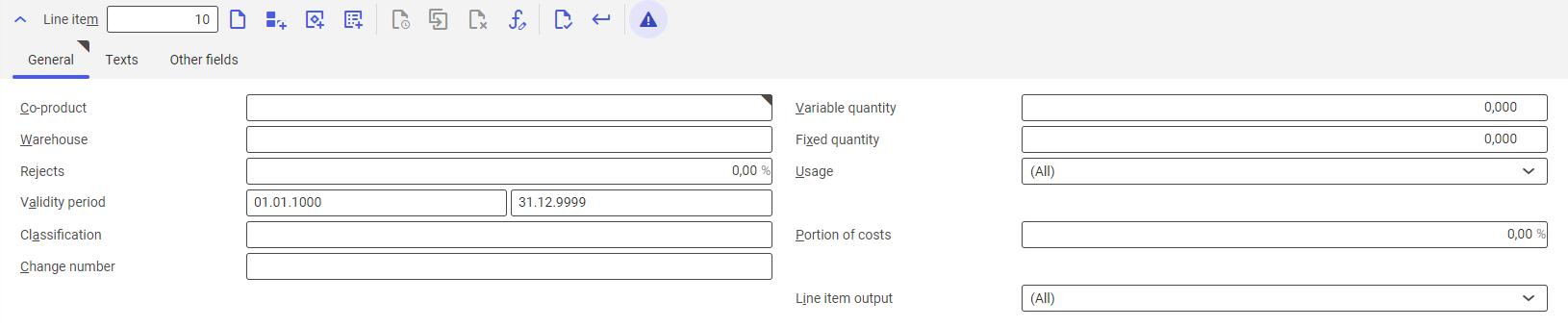
General tab
The General tab in the line item editor displayed when adding a co-product line item contains the following fields:
- Co-product – the name of a co-product added to the table. It must first be defined in the Items
- Variable quantity – a quantity depending on a quantity specified in a production order, required to manufacture a given product
- Warehouse – the site of a line item added to the list
- Fixed quantity – in this case quantity will not be recalculated if a quantity is defined in a production order – the fixed quantity will always have the same value
- Rejects – the percentage value of a material rejects quantity
- Usage – it makes it possible to select a process in which a given material is to be used:
- (All) – it selects all the following options
- Cost Accounting
- Planning
- Scheduling
- Validity period – the validity date of an added line item. By default, it is set as 01.01.1000 – 31.12.9999.
- Classification – a classification number assigned to structure data. Data classifications are defined in the Classifications In order to add a classification to a material added to a bill of material, it is necessary to add a bills of resources line item classification.
- Portion of costs – the percentage value of a portion of costs of producing a by-product in the production cost calculation
- Change number – a number assigned in the Change numbers It makes it possible to register changes to a line item.
- Line item output – a document where a given line item is to be included upon export.
Texts tab
It makes it possible to add a description/text to a line item.
Other fields tab
The tab makes it possible to adjust additional fields for an item. An additional field may be used to enter data that is not provided in the system’s default tabs.
The tab contains the following buttons:
- [Properties] – it allows editing existing fields
- [New] – it adds a new field
- [Delete] – it makes it possible to delete defined field parameters
- [Arrange] – it makes it possible to adjust the view of fields in columns
- [Generate table schema] – it defines a field table schema, enabling the user to use such a schema.
The number of fields defined for an item is not limited.
Line item editor – [New bill of material line item]

General tab
The General tab in the line item editor displayed when adding a bill of material line item contains the following fields:
- Bill of material – the name of a bill of material added to the table. It must first be defined in the Bills of material
- Variable quantity – a quantity depending on a quantity specified in a production order, required to manufacture a given product
- Rejects – the percentage value of a material rejects quantity
- Usage – it makes it possible to select a process in which a given material is to be used:
- (All) – it selects all the following options
- Cost Accounting
- Planning
- Scheduling
- Validity period – the validity date of an added line item. By default, it is set as 01.01.1000 – 31.12.9999.
- Line item output – a document where a given line item is to be included upon export.
- Classification – a classification number assigned to structure data. Data classifications are defined in the Classifications In order to add a classification to a material added to a bill of material, it is necessary to add a bills of resources line item classification.
- Change number – a number assigned in the Change numbers It makes it possible to register changes to a line item.
Texts tab
It makes it possible to add a description/text to a line item.
Other fields tab
The tab makes it possible to adjust additional fields for a bill of material. An additional field may be used to enter data that is not provided in the system’s default tabs.
The tab contains the following buttons:
- [Properties] – it allows editing existing fields
- [New] – it adds a new field
- [Delete] – it makes it possible to delete defined field parameters
- [Arrange] – it makes it possible to adjust the view of fields in columns
- [Generate table schema] – it defines a field table schema, enabling the user to use such a schema.
The number of fields defined for a bill of material is not limited.