Introduction
The configuration of items is always used if certain properties or parameters of an item are specified only according to the requirements of the ordering party during the quotation phase for instance.
The product configurator can be used to generate production variants of an item with the help of an individual bill of resources. The easiest case here will be that you wish to query configuration characteristics in a specific sequence from the user and on the basis of the user’s decision, you evaluate the parameters in the bill of materials and routing, demand materials, operations and resources and recalculate quantities and times using formulae.
You must be clear about the scope of use of the routings and bills of materials. You can evaluate all configuration characteristics in one bill of material (nested as well) and a routing and then produce several different items. And you can uniquely identify a configurable item occurring in many variants only if you specify an identifier for it. Therefore, in certain conditions, it is logical to create a configurable item that is managed with identifiers and use the automatic identifier opening. With that, an identifier is automatically issued in the sales order while saving the configurable item. This identifier is also entered in the production order generated.
Three components for a product configuration are necessary:
- an item that can be configured (this item must have production data)
- configuration rules according to which configuration can take place:
- configuration steps and configuration parameters
- the rule system – conditions and actions
In order to be able to determine the sales price and cost of goods for the configured item, the calculation schema and calculation type is entered in the product configuration rule, with which the item can be calculated. In the calculation schema you can also view the calculation line items that contain the sales price and cost of goods. If supplementary line items are generated with the configuration, then the definitions for the quantities and price calculations are also created in the product configuration rule. The prices for supplementary line items can be determined from sales price lists.
The actual configuration dialog that queries the configuration characteristics, checks the entries and runs the configuration according to the rule system.
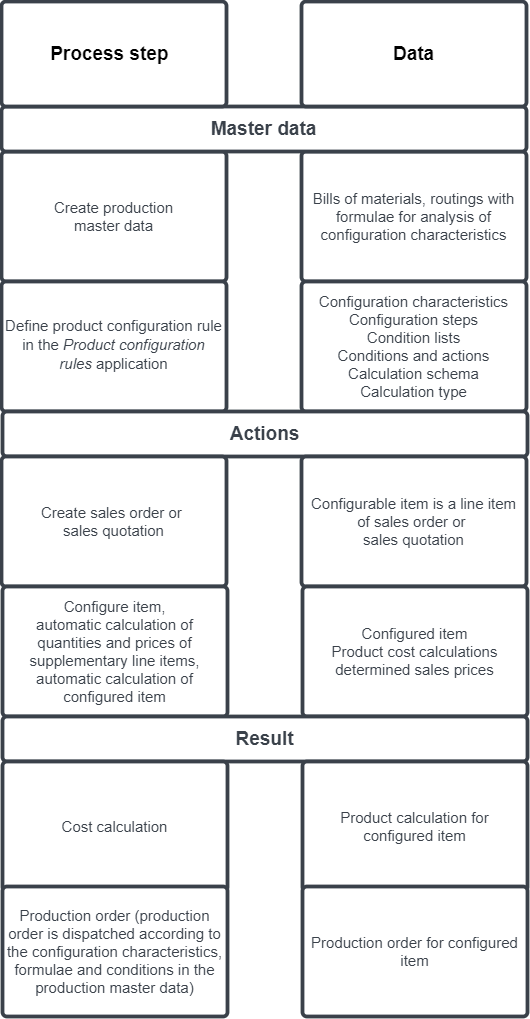
The illustrated process initiates production of a configured and calculated item.
Formulae and conditions are used in the production structures so that the configuration characteristics are incorporated into the production structure. Materials and resources or operations can be selected according to the identifiers of the configuration characteristics in order to calculate the times and quantities. So, for each configured item, a special production order is created during dispatching. The same is applicable for production cost calculations. According to the characteristic values, the item is calculated and the sales price and cost of goods determined individually and made available in the sales quotation and/or sales order. The product cost calculation is then linked with the sales quotation or sales order by way of voucher references chain.
Definition of terms
Item characteristics
Item characteristics are used to describe specific features of items (such as items which are machine parts). Item characteristics are assigned to item characteristic classifications. Item characteristics are defined in the Item characteristic classifications application and assigned to items (based on the created classification) in the Item characteristics application. Any classification systems can be built up with the aid of definable item characteristic classifications. Item characteristics are adopted within a classification.
Characteristic values
Characteristics values are the specific values that a characteristic can assume. Characteristics values can consist both of a selection of attributes, e.g., steel, carbon, or aluminum, and of any discrete values within a value range, e.g., 10.01, 12.19 or 28.00.
Maximum routing
A maximum routing lists all possible operations that could be used in manufacturing a production item. Via criteria in the routing, exactly those operations are selected that are needed for production of a specific item.
Maximum bill of materials (BOM)
A maximum BOM lists all materials that could be used in manufacturing a production item. Via criteria in the BOM, exactly those materials are selected that are needed for production of a specific item.
Applications
The applications and systems settings below are necessary in order to properly define a configurable item.
Items
The production configuration rule, assigned to one or more items in the Items application under the Production view must match with the production data (bill of materials and routing) which must also be assigned to this item/these items. In order to guarantee that, it is recommended to use the production methods which can be activated in the Customizing application → Method function.
In works without production method, bills of materials and routings can be assigned to production orders. If this being the case, it is not verified whether the configuration characteristics of the bills of resources used in the conditions and formulae match with those of the item configuration. The dispatching and calculation do not function in some conditions, since configuration characteristics used in formulae and conditions are not available.
An item can either be configured:
- with the help of item characteristics classification and the configuration characteristics defined in it or
- with the help of product configuration rules.
A standard product configuration can be entered in the Items application → Production view → Production data grouping → [Create item configuration] button. It is used for item cost calculation.
Product configuration rules
The Product configuration rules application consists of four views presenting the following information:
- the configuration steps and their sequence
- the configuration characteristics that must be specified in the configuration dialog window (at least one characteristic is required)
- the condition list (at least condition list is required when conditions and actions are entered)
- conditions and actions
For a detailed description of this application, refer to article Product configuration rules.
Sales quotations and sales orders
The system recognizes a line item in the sales quotation or sales order as configurable. The configuration dialog window is opened while checking or accepting the line item in the line item table.
Accepting a configured item
A configurable item can be completely configured and calculated in the sales quotation itself. Configurations of the line items are accepted while:
- duplicating the configured line items
- adding a line item with the [Find and add line items] button
- generating a sales order from a sales quotation with the [Generate from quotation] button
Pricing through product cost calculation
The sales price of a configured line item is determined in the product cost calculation. It must be calculated as gross unit price. A net margin percent rate saved in the sales item is also used for line items with configured items for net margin check.
If the price is successfully determined through a product cost calculation, then the category of price origin is Item configuration (the precondition is that a calculation schema and calculation type must be saved in the product configuration rule). If the calculation was carried out successfully, then the quotation or order line item cannot be accepted in the line item table.
For more information, refer to articles Product cost calculations and Trade cost calculations.
Voucher relationships
While saving the sales quotation with the configured item, a voucher reference is automatically generated for the quotation calculation and product cost calculation.
While saving the sales quotation with the configured item, a voucher reference is automatically generated for the order calculation and product cost calculation. Additionally, a production order is generated for which a voucher reference is also generated.
Automatic generation of a production order is determined in the Sales order types application under the Production data tab. A production order is generated automatically after releasing the line item with the Release action.
If a sales order is generated from a sales quotation, then the quotation calculation is retained. An order calculation is generated in addition.
From the view of the production order, the sales order is contained in the voucher references chain. The relationship to the quotation, order calculation and production order is visible in the voucher references chain of the sales order.
Supplementary line items in sales quotations and sales orders
Supplementary line items are generated in the product configuration rule using a relevant action. These supplementary line items are accepted in the sales quotation or sales order and displayed there as sub-items for the configured production item. These supplementary line items must be sales items. For the definition of the Generate supplementary line item action in the Conditions and actions view of the Product configuration rule application, there are fields for the sales item to be made supplementary line item (its unit of measure and formula fields for the calculation of the quantity and the price of the supplementary line item).
For more information on how to generate supplementary line items for the configured items, refer to article Product configuration rules.
Material requirements planning
Material requirements planning has some special features and limitations while including configured items. They are described below:
- For an item configured in the sales process, a production order is generated from the order. This means that for one demand origin, there is also exactly one demand coverage. If the production order is dispatched, then the material required for production is uniquely determined through the dispatching. This case does not create any special features for planning.
- If the production order was not generated or dispatched, then the planning must determine the secondary demand on the basis of the configuration.
- A standard configuration is created in the production item data for configured items (Items application → Production view → Production data grouping → [Create item configuration] button). This standard configuration is used if a minimum or reorder level has been created in the planning data. The secondary demand for this demand is then determined for the standard configuration.
- Configured items for which there is a demand origin are considered independent of minimum and reorder level. Own planning recommendations are generated per configured item. Planning recommendations for primary demand for configured items are always considered separately and never summarized.
- Configuration is included while triggering the secondary demands. Material demand of the first level of production structure is calculated in planning. Secondary demands are not initialized with the configuration.
- If there is more than one planning recommendation for a planning period, the value cannot be changed manually.
- For configurable planning recommendations, generally no production recommendations can be generated; for instance, neither for the items configured in sales order, nor for items leading to a planning recommendation on account of a minimum or reorder level.