This article describes how inventory orders are represented in the system and how the corresponding application is structured. You will learn about the relationship between an inventory order and other applications as well as business entities, and how inventory order is integrated into the business processes.
Article Inventory order types explains the role of different types of inventory orders and how they are created or generated in the system. The procedures for handling inventory orders, such as how to report inventory orders, can be found in article Procedures: Inventory orders.
Definition of terms
Identifiers – an identifier identifies a specific item. For example, a TV is identified not only by its item number but also by its serial number, which makes it unique. The system supports the following identifiers: batch, lot and serial number.
Loading unit – a loading unit is a combination of items in or on a suitable storage unit in order to store or ship them. A loading unit can also include other loading units.
Inventory order – an inventory order determines the transport of items inside a warehouse. The inventory order specifies which item in what quantity is to be transferred from a warehouse zone, from a storage location or from a warehouse to another location. A manual inventory order is formulated in the form of an inventory requisition.
Warehouse – a warehouse is a logically or physically separated area where items are stored. If storage location control is activated in the Customizing application, then a warehouse can be further subdivided into warehouse zones and storage locations. The exact warehouse structure is determined by the warehouse organization.
Storage location – a storage location is the exact point in a warehouse where items can be stored. A storage location within a warehouse always lies in a warehouse zone and is determined precisely on the basis of a row, a level, and a storage location number. Each storage location has a storage location category that establishes the use of the storage location. The availability of storage locations is essential for storage location control.
Warehouse zone – if storage location control is activated in the Customizing application, a warehouse can be subdivided into warehouse zones. A warehouse can have any number of warehouse zones.
Serial number – serial numbers are possible identifiers for items. Serial number identification means that every unit of an item is given a serial number that identifies it uniquely throughout the system. In contrast to batches and lots, a serial number is assigned to exactly one item in the 1st item unit. The assignment of serial numbers is differentiated into serial numbers with inventory management and serial numbers without inventory management.
Storage slot – a storage slot is a subunit of a storage location. It is the smallest component of a warehouse and it can accept exactly one storage unit. The number of storage slots is the maximum number of storage units allowed for the storage location.
Application description
Inventory orders application is used for processing inventory orders, especially for reporting transported items. Inventory orders cannot be created in this application. If you wish to initiate a manual inventory movement, you need to use the Inventory requisitions application to record an inventory requisition and then generate an inventory order from the inventory requisition.
The application consists of an identification pane and a work pane.
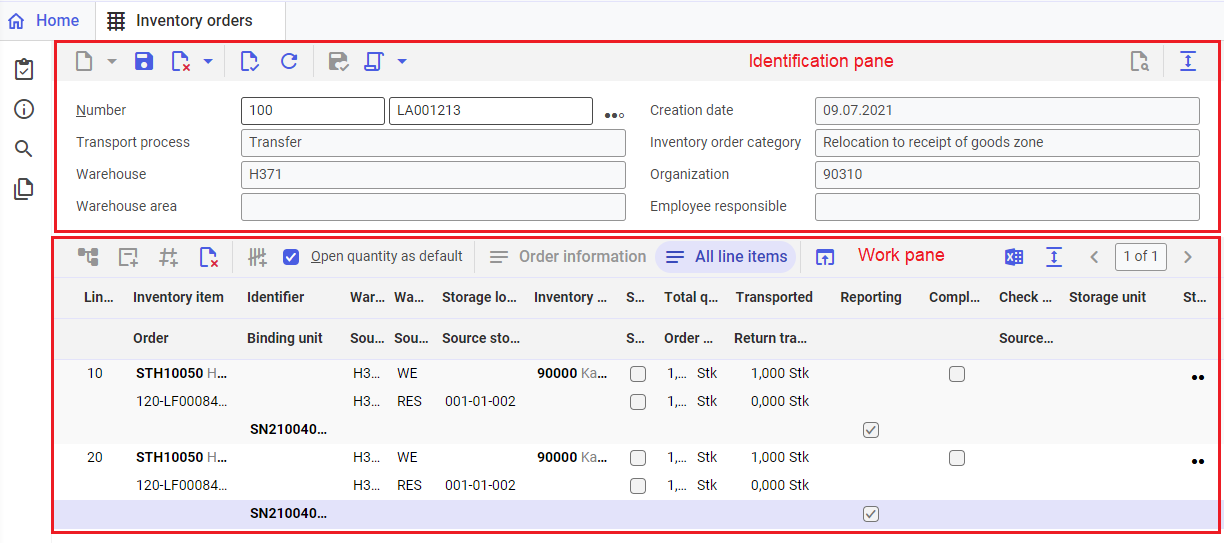
Identification pane
The identification pane contains the fields that uniquely identify the inventory order. The work pane consists of the following fields:
- Category (in the Number field) – enter an existing category of inventory order as search criteria of the inventory order to be displayed or edited in the work pane. The used inventory order category together with inventory order number is used to identify the inventory order.
- Number – enter an existing inventory order number as search criteria of the inventory order to be displayed or edited in the work pane. Inventory order number is generated automatically by the system based on the number ranges defined in the inventory order category. The number cannot be assigned manually. The used inventory order number together with inventory order category identifies uniquely the inventory order.
- Status – the icon informs about the status of inventory order. It shows the following values:
- Generation status
- General status
- Output status
- Creation date – it shows the inventory order creation date.
- Transport process – the following types of inventory order operations are available in this field:
- Put away
- Withdraw
- Transfer
- Put back
- Revaluate
In the Put away transport process, the source location is the receipt of goods zone. In the Withdraw transport process, the destination location is the issue of goods zone. In the Put back transport process, the source location is the issue of goods zone. This information is not displayed in the inventory order line item.
In the Transfer transport process, the inventory order has values in the Source warehouse field and, if the source storage location is reported back with a check digit, it has also values in the Source warehouse check digit. The [Order information] button is activated when opening the inventory order in such as case.
If the Revaluate transport process, no inventory posting takes place. It is only possible in the non-subdivided warehouse zones.
- Inventory order category – the field shows a more detailed division of a transport operation. Available options are:
- Relocation for withdrawal
- Relocation for put away
- Direct relocation
- Relocation to receipt of goods
- Return transfer
- Receipt of goods
- Issue of goods
- Relocation of picking point
- Revaluation
- Warehouse – the field shows the main warehouse of inventory order. If the inventory order is used for a transfer posting, the source warehouse is displayed, except when the warehouse is not divided into storage locations.
- Organization – this field shows the inventory owner. The inventory owner is the legal owner on inventory and is defined for each storage location. It is used for multiple processes in inventory management, such as stocktaking and inventory valuation.
- Warehouse area – warehouse area for which a specific inventory order has been generated. The warehouse area is only displayed if it was grouped during generation of an inventory order and if a storage area is assigned to the identified zones and slots.
- Employee responsible – if necessary, enter the identifier of the partner with the Employee role, who is responsible for the inventory order. By specifying a responsible employee, you can distribute the workload among employees. You can assign a responsible employee until the inventory order is completed.
Work pane
The work pane contains a list of line items to transport. It consists of the following columns:
- Line item – indicates the number of inventory order line item.
- Item – indicates an inventory item to be transported. An item is specified during inventory order generation and cannot be later changed.
- Identifier – presents a possible identifier of an inventory item. Depending on the nature of the inventory order, the column may be either read-only or editable. If you change the suggested identifier, both the reservation and the storage location reservation for that identifier are canceled. Subsequently, a new reservation and storage location reservation are made for the newly entered identifier. The newly entered identifier can only be saved if
- both reservations are canceled for the total quantity,
- both reservations are canceled for the total quantity,
If the identifier is not entered during put-away from the receipt of goods and the generation method is set to Automatic for the item, a new identifier will be generated automatically. You can also enter an identifier using the Identifiers application.
For serial number without inventory management, it is not possible to enter an identifier for put-away.
HintThis column is only visible if the Identifiers function is activated in the Customizing application.
- Warehouse – a warehouse is displayed in this column. In the Withdraw transport process, the source warehouse is displayed. In the transport processes Put away, Transfer or Put back, the destination warehouse is displayed. A warehouse is specified during inventory order generation and cannot be changed.
- Warehouse zone – a warehouse zone is displayed in this column. In the Withdraw transport process, the source warehouse zone is displayed. In the transport processes Put away, Transfer or Put back, the destination warehouse zone is displayed. Depending on the nature and status of the inventory order, the column may be either read-only or editable. Value in this column cannot be changed if the quantity is already accepted for a specific line item or if the inventory order is in the status Completed. If an inventory order is generated from an inventory requisition, this field cannot be changed even if the warehouse zone is already specified in the inventory requisition. If you change the suggested warehouse zone, the storage location reservation is canceled and a new storage location reservation is made for the new storage location.
- Storage location – a storage location is displayed in this column. For an inventory order with the transport process Withdraw, the source storage location is displayed. For an inventory order used for Put away, Transfer or Put back, the destination storage location is displayed. If a storage location is divided into storage slots, the storage slot identification is also displayed. Depending on the nature and status of the inventory order, the column may be either read-only or editable. The warehouse cannot be changed if the quantity is already accepted for a specific line item or if the inventory order is in the status Completed. If the inventory order originates from an inventory requisition and a storage location or a warehouse zone is already entered in the inventory requisition, then the column cannot be changed. If you change the suggested storage location, the storage location reservation is canceled and a new storage location reservation is made for the new storage location.
- Inventory owner – the owner of the reported inventory is displayed in this column. The column is editable if no inventory order is entered in the associated picking order or inventory order. In this case, you should enter the inventory owner for reporting. Since a storage location can only store inventory belonging to a single inventory owner, there is no need to create an inventory owner during reporting in the storage location. Inventory owner must, however, be created during the reporting in the warehouse zone. After the reporting, including also partial reporting, the inventory owner can no longer be changed.
- Total quantity – the total quantity is displayed in this column. This quantity represents the quantity intended for transport. The displayed quantity is not editable. For inventory order line items with loading units, this column shows the number of loading units to be transported, which is always displayed as 1. In the case of unsaved split line items, this column is not visible. When saving a split line item, the total quantity is populated with the quantity entered into the reporting. Such transfer of quantity will occur with each saved split line item. During splitting, the total quantity of the original line item is reduced by the total quantity of the split line item. Changing the total quantity of a split line item updates the total quantity of the original line item.
- Transported – the quantity already transported is displayed in this column. The transported quantity is derived from the sum of all the reportings carried out for this line item. The displayed quantity is not editable. For inventory order line items with loading units, this column shows the number of already transported loading units. It displays 0 if the inventory order line item is not yet reported or 1 if the line item is already reported.
- Reporting – the quantity to be reported is displayed in this column. If open quantity is set as the default value in the Customizing application, the system will report the difference between the quantity of the inventory order (or the target quantity) and the quantity not yet reported. For split line items, the total quantity is always suggested, regardless of the settings in the Customizing application.
HintYou can additionally use the function Open quantity as default, so that the system suggests the open quantity or zero quantity.
The following special features apply:
- Serial numbers with inventory management and loading units can only be reported in the quantity equal to (1). For this reason, a checkbox is displayed in the quantity column for the line item with a loading unit or for the line item with only one serial number. Reporting is processed by activating this checkbox.
- For serial numbers without inventory management, quantity entry has different meaning. The meaning of the quantity column depends, inter alia, on the voucher from which an inventory order was generated:
- Receipt of goods
If the inventory order was generated from a receipt of goods, this column is used for entering the quantity to be reported. In this case, it is not possible to enter a serial number.
- Picking order, delivery order
If the inventory order originates from a picking order or a delivery order, the column is used to determine the quantity to be reported, provided that a single serial number should only be reported. A serial number must be created. If the quantity to be reported is greater than 1, the column is used to determine the number of serial numbers to be generated automatically using the first serial number registered. Upon generation, this number is set to 0. Reporting without a serial number is not possible.
- Inventory requisition
If the inventory order originates from an inventory requisition, the column is used both for reporting and to determine the number of serial numbers to be generated automatically. In this case, reporting is possible both with and without a serial number specification.
HintInventory requisition determines the maximum number that can be reported. Overdelivery is therefore not possible, even if the corresponding setting in the inventory order category so provides. - For an item that is managed in only one item unit, the quantity can be reported in one of its packaging units
Line items with multiple serial numbers do not have a checkbox for reporting. Reporting is carried out for them using the checkboxes in the lines with serial number assignments, which are displayed for each serial number.
If open quantity is set as the default value in the Customizing application, the checkbox will be activated after the inventory order is opened
- Complete after reporting – if this is activated, the line item is marked Completed after reporting. Any reporting quantity entered is reported as usual. The original voucher is not updated for the quantity that is still open, so that a new inventory order can be created for the quantity that has not yet been transported. The setting of this function has no impact on saving an inventory order without reporting. After opening the inventory order, this function is not activated. The function cannot be set for split and completed line items.
- Check digit – if the function Report using check digit is activated for a warehouse, you must enter the check digit of the storage location in the Check digit column when reporting the inventory orders. You can only confirm the inventory order successfully if you have entered the correct check digit for all inventory order line items with a check digit. You can check the check digit of the storage location in the Storage locations application.
- Storage unit (checkbox) – using the function With storage unit, you can specify whether the transport process is to be carried out with or without storage units. In addition, the storage unit is displayed, which is specified automatically or by the following vouchers:
- Inventory requisition
- Picking order
- Delivery order
- Change of a storage location with storage units into a non-structured warehouse zone or into a storage location without storage units.
- Change of a non-structured warehouse zone or a storage location without storage units into a storage location with storage units
- Status – the status of inventory order line item is displayed in this column. The status is composed of two individual statuses. Following statuses are available:
- General status
- Generated
- Completed
- Reserved quantity not available
- Reporting status
- Not reported
- Reported partially
- Reported completely
HintReserved quantity not available status is assigned when the inventory count list line item is closed if the quantity in a warehouse zone or in a storage location is reduced by the inventory count to such an extent that the required quantity of open processes and vouchers for this warehouse zone or storage location is no longer covered.If a line item is reported as Reserved quantity not available, the system checks again whether the required quantity of open processes and vouchers can be covered. If the quantity is sufficient, it is reported and completed. If the quantity is not sufficient, the line item can be completed or deleted without reporting.
- General status
The default setting of this function is specified automatically during generation of an inventory order based on a storage location and the quantity to be transported. For example, storage in the storage location of storage location category Storage location with storage unit is only allowed for a storage unit when the storage location is empty. On the other hand, it is only permissible to fill up an existing opened storage unit without any storage units.
HintIt is recommended to change the default setting of this function only when the suggested storage location is changed.If any changes are made, the following should be taken into account:
In this case, the function With storage unit is no longer displayed on the user interface after selecting the button Validate or Save.
In this case, select the button [Validate] to activate the function With storage unit on the user interface to be able decide before reporting whether to make changes with or without storage units.
If the value does not correspond to the nature of the storage location, an error message is displayed during reporting. If you change the default setting of this function, the storage location reservation is canceled and a new storage location reservation is made with the changed storage unit data.
NoteYou cannot change the setting of this function if the inventory order originates from an inventory requisition in which a storage location has already been entered.This function is active and not editable if the inventory order assigns a picking order though a picking point to the storage location without an identifier (batch or lot only). For more information, refer to article: Introduction: Picking with storage location-managed warehouses
Serial number assignments
Inventory order line items with multiple serial numbers can only be reported via serial number assignment. The assignments are either created during inventory order generation or must be assigned manually to report the line item. For serial number assignments, the following columns are used:
- Identifier – the serial number to be reported is displayed in this column. Depending on the nature and status of the inventory order, the column may be either read-only or editable. The column is no longer editable if the item is already completed or the assigned serial number is already reported. Otherwise, the column is always editable for serial numbers without inventory management. For serial numbers with inventory management, the column is editable only if the serial number is not specified in the original voucher. An exception is the receipt of goods as an original voucher: the column is editable even if the serial number is already specified in the receipt of goods.If you change the default serial number, both the reservation and the storage location reservation for that identifier are canceled and a new reservation and storage location reservation are made for the newly entered serial number. The newly entered serial number can only be saved if
- reservations are canceled
- a new serial number is generated for both reservations
If the serial number was not created during a put away from the receipt of goods and the creation method for the item is set to Automatic, then a new serial number will be generated automatically. You can also enter serial numbers manually using the Identifiers application.
When reporting serial numbers without inventory management, you can have the serial number assignments generated with an automatic assignment of the serial numbers. To do this, you must create a serial number assignment manually. In this assignment, you have to enter a serial number from which onwards counting up can start. In the quantity field, you enter the desired number of serial numbers and the next time you check or save, serial number assignments will be generated automatically.
- Reported (checkbox) – the checkbox in this column is only visible when the identifier assignment is saved. An active field means that the serial number included in this assignment is to be reported the next time you save and report.
Loading unit assignments
Loading units can only be reported via loading unit assignment. The assignments are either created during inventory order generation or can be assigned manually to report the line item. For loading unit assignments, the following columns are used:
- Loading unit – the loading unit that is assigned is displayed in this column. Depending on the nature and status of the inventory order, the column may be either read-only or editable. Value in this column cannot be changed if the unit is already reported or if the inventory order is in the status Inventory order completed. Value in this column can also no longer be changed in the inventory order was generated from a receipt of goods or an inventory requisition and the loading unit was already specified there. If you change the suggested loading unit, the storage location reservation for that loading unit is canceled and a new storage location reservation is made for the new loading location.
Buttons and actions in the work pane
The toolbar contains a list of actions for editing line items; they are described in the following chapters:
- Action [Split line item]
- Action [Add serial number field]
- Action [Add loading unit]
- Action [Report additional quantity for completed line items]
You can additionally use the function Open quantity as default, so that the system suggests the open quantity or zero quantity.
The buttons in the work pane can be used to show and hide additional information about the inventory order line item. These buttons are described in the following chapters:
Action [Split line item]
With this action you can split a created line item once or multiple times. Whether you can split a line item depends, among other things, on the transport process, the item identifier, the specifications in the original voucher and existing return transfer orders.
To be able to report a split line item, the warehouse zone or storage location(s) must be different from the original line item. A split item can also be reported during the Withdraw transport process if the line item is managed in batches or lots and has a different identifier from the original line item.
When splitting, the quantity suggested as the reported quantity is the difference between the open line item quantity and the reported quantity entered for the split line item. In addition, the total quantity of the original line item is reduced by the reported quantity of the split line item. When saving, the total quantity of a split item is always set to the amount of the entered reported quantity. The total quantity of the original line item is adapted accordingly.
To be able to guarantee a storage location reservation, a reported quantity must always be entered for a split line item. If the corresponding original line item is already completed, the reported quantity of the split line item can no longer be changed and may only be reported in full.
When deleting a split line item that has not yet been completed, the total quantity of this line item is transferred back to the original line item. If the original line item is already completed, then a split item can no longer be deleted.
It is not possible to split line items that have already been split. Only those line items can be split that were created during generation of an inventory order.
Action [Add serial number field]
With this action you can add one or more serial numbers to an inventory order line item. The serial number can only be added if the inventory order quantity is grater than one. If the order quantity is exactly one, then the assignment of the serial number takes place via the identifier column in the line item. Reporting regarding the serial number already assigned during inventory order generation takes place via the checkbox in the serial number assignment. The added serial numbers subsequently can either be saved first or also reported immediately using the [Save and report] action.
To be able to add a serial number to an inventory order line item, the warehouse, storage location and warehouse zone in which the item with the serial number is stored must match the information in the inventory order line item. The serial number cannot be reserved.
If the serial number could not be added or reported, an error message is displayed.
HintSerial number can only assigned to an item if the Identifiers function is activated in the Customizing application.How to add a serial number field without inventory management
In the Inventory orders application, serial numbers without inventory management can also be added to an inventory order line item using the action Add serial number field. In contrast to serial numbers with inventory management, some special features must be taken into account.
If the original voucher is a receipt of goods or an inventory requisition, then it is not allowed to add serial numbers without inventory management to the inventory order item. If this being the case, reporting is only allowed via a quantity specification.
For inventory orders generated from a picking order or a delivery order, reporting can only be done via serial number assignment. In contrast to serial numbers without inventory management, for the line item with serial number without inventory management, the quantity column is available. The quantity column is used for reporting if the order quantity is 1. In such case, the assignment of the serial number takes place via the identifier column in the line item. For line items with the order quantity greater than one, the column is used for entering the number of serial numbers to be reported. Using the combination of the number of serial numbers and the serial number assignments, further serial number assignments are generated automatically. These assignments show serial numbers that could be generated starting from the first serial number. The specified number is automatically set to 0 after the serial numbers have been generated. The generation itself is executed by selecting the [Validate] or the [Report] button.
Action [Add loading unit]
With this action you can add one or more loading units to an inventory order line item. Whether one or more loading units can be assigned to a line item depends, among other things, on the type of storage location in which put-away or withdrawal takes place.
To add a loading unit to an inventory order line item, the following must be fulfilled:
- The loading unit has the same items as the inventory order line item and has a status that corresponds to the transport process.
- The loading unit can have the same identifiers, unless a return transfer exists for the inventory order line item.
- The warehouse, warehouse zone and storage location, in which a loading unit is stored, match the data in the inventory order line item.
If the loading unit could not be added or reported, an error message is displayed.
Action [Report additional quantity for completed line items]
With this action you can report an additional quantity for the line items that have already been completed. The Reporting column becomes ready for input, so that you can enter a quantity and report the line item again. The checkbox in the Storage unit column also becomes adjustable, so that you can report the additional quantity with or without a storage unit. The warehouse zone and the storage location cannot be changed.
The action is only available for inventory orders within the Withdraw transport process. An additional quantity can also be reported for inventory orders that have already been completed. The action is not available for line items with serial number-managed items and with loading units.
HintThis action is not available when importing inventory order reportings. For inventory order line items that have already been completed, no additional quantity can be reported via the import.Button [Order information]
This button is used to show and hide order information. If the inventory order is used for the Transfer transport process, the [Order information] button is already activated when the inventory order is opened and the order information is displayed.
The following columns are displayed:
- Order – this column shows the identification of the source voucher from which an inventory order was created. The source voucher can have one of the following voucher types:
- Inventory requisition
- Picking order
- Delivery order
- Receipt of goods
If there is no source voucher, e.g., for a replenishment for a picking point, then the column is empty.
- Binding unit – this column shows with an icon which setting for binding units is defined in the source voucher. The inventory order item was created according to this setting. For simple warehouses it follows from this setting in which units the reporting can be processed. Following settings are available:
- Included in packaging structure – the quantity can be retrieved either in the unit resulting from the source voucher or in the packing unit containing the requested unit according to the packaging structure of the item.
- Binding – the quantity must be retrieved in the unit resulting from the source voucher.
- Nonbinding (no icon) – the quantity can be retrieved in any unit that can be recalculated into 1st item unit.
For Put away and Transfer transport processes, the unit must be reported in the unit resulting from the source voucher.
- Source warehouse – this column shows the inventory orders of Transfer and Put back transport processes for the source warehouse. In the Put away and Withdraw transport processes, the warehouse is also source warehouse.
- Source warehouse zone – this column shows the inventory orders of Transfer and Put back transport processes for the source warehouse zone. Depending on the nature and status of the inventory order, the column may be either read-only or editable. Value in this column cannot be changed if the quantity is already reported for the line item or if the inventory order is in the status Completed. If the inventory order originates from an inventory requisition and a warehouse zone is already entered in this inventory requisition, then the column cannot be changed. If you change the suggested warehouse zone, the storage location reservation is canceled and a new storage location reservation is made for the new storage location.
- Source storage location – this column shows the inventory orders of Transfer and Put back transport processes for the source storage location. If a storage location is divided into storage slots, the storage slot identification is also displayed. Depending on the nature and status of the inventory order, the column may be either read-only or editable. Value in this column cannot be changed if the quantity is already reported for the line item or if the inventory order is in the status Completed. If the inventory order originates from an inventory requisition and a storage location or a source warehouse zone is already entered in the inventory requisition, then this column cannot be changed. If you change the suggested storage location, the storage location reservation is canceled and a new storage location reservation is made for the new storage location.
- Source inventory owner – for inventory orders of the transport operation Revaluate, the previous inventory owner is displayed. In the case of revaluations for the transfer of consignment inventory to own inventory, this is the partner involved in the consignment transaction as supplier.
- Order quantity – this column shows the maximum quantity that is reported to the source voucher. The quantity displayed is not editable in this column, but it is updated via certain actions, such as line item split.
- Return transfer quantity – this column shows the quantity that will be stored back by any existing return transfer order. The quantity displayed is not editable in this column, but it is updated when the quantity of the associated return transfer order is changed. This column is only available for inventory orders of types Relocation for withdrawal and Issue of goods.
- Source warehouse check digit – if the function Report using check digit is activated for a source warehouse, you must enter the check digit of the source storage location in the Source warehouse check digit column when reporting the inventory orders. You can only report the inventory order successfully if you have entered the correct check digit for all inventory order line items with a check digit. You can check the check digit of the source storage location in the Storage locations application.
Button [All line items]
If you activate this button, then both inventory order line items with the open quantity zero (0) and already reported serial numbers and loading unit assignments will be displayed.
Button[Edit logistic units]
Selecting this button opens the corresponding application in a dockable window at the edge of the application’s work pane. Using the Edit logistic units application, you can pack items whose packaging units are kept in inventory into the desired packaging units or unpack the packed items.
To do so, select in the work pane the line with the item or identifier whose logistic unit you want to edit and then select the [Edit logistic units] button. The required information is transferred to the dockable window.
Description of the Edit logistic units application can be found in article How to edit logistic units.
This button is available if the function Manage inventory in logistic units is activated in the Customizing application → Inventory management → Warehouse inventory.
Application-related actions
The toolbar contains a list of actions for handling the Inventory orders application; they are described in the following chapters:
- Action [Save and report]
- Action [Complete without reporting]
- Action [Discard an open put-away]
- Action [Sort line items]
- Action [Output inventory order]
- Action [Output storage labels]
- Action [Put in process]
- Action [End processing]
- Action [Generate inventory requisition for return transport]
Action [Save and report]
With this action you can save changes and also report the line item quantities for which the reported quantity has been entered. In contrast to the [Save] action, the [Save and report] action is followed by an additional default value determination for the items. The confirmation triggers a material posting.
In the case of inventory orders of Revaluation category for the transfer of consignment inventory to own inventory within the framework of consignment sale, reporting results in a consignment withdrawal.
Action [Complete without reporting]
This action is used to complete an inventory order without reporting any open quantities.
The target quantity or partial quantities of specific inventory order line items should be reported before the action Complete without reporting is carried out.
When completing without reporting the inventory orders to which a return transfer order is associated, the return transfer order is also completed without reporting. If the return transfer order is completed without reporting first, the original inventory order is not changed and the quantity of the return transfer order is updated accordingly. Note that a normal reporting of this order also results in a withdrawal to the issue of goods zone of the quantity that otherwise would have been returned by that return transfer order.
Every completion without reporting results in the status of the original voucher not being updated. Another inventory order can in such a case be generated only for the quantity that is still open.
Action [Discard an open put-away]
This action is used to discard unprocessed line items of inventory order so that they are marked as Put-away in full in the corresponding receipt of goods and consequently it is not possible to generate another inventory order for them from the receipt of goods.
The prerequisite for executing this action is that an inventory order with the transport process of Put away type is open, contains at least one line item that has not yet been reported, and the application is in display mode.
During this action, the unreported line items with open put-away quantities are marked as Reported completely and Completed. The warehouse reservations generated for put-away are canceled. The open put-away quantities remain in the receipt of goods zone. The line items in the receipt of goods receive the status Put-away in full.
Already reported line items are ignored. If all the inventory order line items have the status Completed after this action is carried out, the status of the inventory order changes automatically to Completed.
Action [Sort line items]
With this action, the line items are sorted as per the sorting criteria specified for inventory order type and warehouse.
This action can only be carried out for inventory orders that are not yet completed and are still editable.
Action [Output inventory order]
This action is used to output an inventory order according to a voucher template.
If Automatically output inventory orders parameter is selected in the Customizing application → Inventory management → Documents, then each inventory order will be output right after an inventory order is generated by the inventory management server. To output an inventory order automatically, use the action [Output inventory order].
Action [Output storage labels]
This action is used to output storage labels for inventory order line items according to a voucher template.
Action [Put in process]
This action is used to change the status of inventory order to In process. According to the inventory order type used and the setting for the change of the responsible employee defined in it, the specification of the responsible employee in the inventory order is also changed. This action is available only for inventory orders in the Not in process status.
Action [End processing]
This action is used to change the status of inventory order to Not in process. It is available only for inventory orders in the In process status.
Action [Generate inventory requisition for return transport]
This action is used to generate an inventory requisition to reverse a transport process. The new inventory requisition refers to a completed inventory order and includes the item quantities transported with the inventory order. This action is only available for completed inventory orders that were generated for one of the following transport processes:
- Put away
- Withdraw
- Transfer
For inventory orders without an original voucher, such as a replenishment for a picking location, this action cannot be carried out. For the new inventory requisition, you can decide, among other things, whether the storage locations of the referenced inventory order are to be used or others.
Depending on the settings in the inventory requisition type, you must then first release the generated inventory requisition and generate an inventory order so that the return transport can take place.
Generate inventory requisition for return transport dialog window
Before the action is carried out, a dialog window opens where you can enter the required data.
The work pane consists of the following fields:
- Site – this field displays the logistics organization for which an inventory requisition is generated.
- Inventory requisition category – this field displays the category of inventory requisition that should be generated for a return transport. If you execute this action in the Inventory orders application, then the corresponding category is displayed and cannot be changed. In cockpit applications, the category is Relocation is suggested so that you can change it if necessary. For more information, refer to chapter Generated inventory requisition.
- Inventory requisition type – in this field, enter the type of inventory requisition; the value must match the entry in the Inventory requisition category field. This type is used to generate an inventory requisition for the return transport. The corresponding inventory requisition type for return transport is suggested in this field, which is defined in the Customizing application → Inventory management function.
- Employee responsible – in this field, enter the partner identification of the employee who is responsible for the inventory requisition to be generated.
- Text – in this field, you can enter any text for the inventory requisition to be generated.
- Warehouse origin – in this type, specify the warehouse for which an inventory requisition for the return transport is to be generated. Following options are selectable:
- Inventory order – an inventory requisition is generated for the warehouse defined in the inventory order. The inventory is transferred back to the warehouse from which it was originally withdrawn.
- Manual – an inventory requisition is generated for the warehouse defined in the dialog window in the Warehouse field. The defined inventory order is not taken into account in the inventory order. With this selection, you can redirect the return transport to another warehouse. For example, you can redirect the item quantities that originally were put away from the receipt of goods directly to the issue of goods zone.HintThis field is only available for input if the Transfer option is selected as the inventory requisition category.
- Warehouse – if the Warehouse origin field is set to Manual, then in this field you need to enter the identification of a warehouse as a destination of the return transport. If the warehouse is structured into storage locations, you can additionally define a warehouse zone in the corresponding field.
- Warehouse zone – if the Warehouse origin field is set to Manual and the warehouse is structured to storage locations, then in this field you need to enter the warehouse zone of the warehouse as destination of the return transport.
- Include current inventory situation (checkbox) – if you activate this function, storage location information from the inventory order is not transferred to the inventory requisition for serial number-managed line items and loading units. Instead, the storage location information is retrieved from the current inventory data. If the serial number or the loading unit is no longer inventory effective or cannot be included in the inventory order due to other properties, then the warehouse order line item is not included and an error message is displayed.
- Automatically confirm warnings (checkbox) – with this parameter, you can determine whether to confirm automatically the warnings displayed during pending actions. If this parameter is activated, the action will be executed successfully even if warnings occur. If this parameter is deactivated, the action will be aborted when warnings occur.
Generated inventory requisition
Decisive for the generated inventory order are inventory order category and the transport process from the respective inventory order.
Description:
Inventory order category | Transport process | Inventory requisition to generate |
---|---|---|
Relocation for withdrawal | Transfer (for inventory requisition) | Inventory requisition of Transfer type from the destination (issue of goods zone) back to the source (withdrawal location of line items) |
Relocation for withdrawal | Withdraw (for picking order) | |
Relocation for put away | Transfer (for inventory requisition) | Inventory requisition of Transfer type from the destination (withdrawal location of line items) back to the source (receipt of goods zone) |
Relocation for put away | Put away (for picking order) | |
Direct relocation | Transfer (for inventory requisition) | Inventory requisition of Transfer type from the destination back to the source |
Relocation to receipt of goods | Transfer (for inventory requisition) | Inventory requisition of Transfer type from the destination (receipt of goods zone) back to the source |
Relocation to receipt of goods | Withdraw (for put away cancellation) | |
Relocation of picking point | Transfer (for inventory requisition) | Inventory requisition of Transfer type from the destination back to the source (issue of goods zone) |
Return transfer | Transfer (from picking point) | Inventory requisition of Transfer type from the destination (issue of goods zone) back to the source |
Receipt of goods | Put away | Inventory requisition of Withdrawal type with destination as source |
Issue of goods | Withdraw | Inventory requisition of Put-away type with source as destination |
Statuses and how to change the status
An inventory order can be marked with statuses described under:
Generation status
Following statuses are possible for inventory order generation:
- Generation canceled – the generation of the inventory order could not be completed properly. This status usually indicates a technical problem. You can find more information about it in the message log. An inventory order with this status does not include all the line items it should have. Nevertheless, it is error-free and can be processed in the same way as an inventory order with the status Generated completely. Once the technical problem is solved, the inventory order generation should be executed again to obtain another inventory order with the remaining line items.
- Generated for partial quantity – the inventory order does not include the complete quantities due to the current inventory situation. For example, it was not possible to collect the entire quantity for a picking order to issue goods from the warehouse. Nevertheless, the inventory order is error-free and can be processed in the same way as an inventory order with the status Generated completely. Once the inventory situation is changed, the inventory order generation should be executed again to obtain another inventory order with the remaining line items.
- Generated completely – the inventory order was generated for the complete quantity.
General status
The general status can have the following options:
- Not in process – the inventory order is generated and not editable. The inventory order can be edited as long as it is not completed. This status serves as information and has no effect on the reporting of the inventory order.
- In process – the inventory order is being edited. The inventory order can be edited as long as it is not completed. This status serves as information and has no effect on the reporting of the inventory order.
- Completed – the inventory order is completed. This status is assigned automatically if one of the following conditions is fulfilled:
- The order quantities of all line items were reported completely.
- The inventory order was completed upon reporting.
- The inventory order was completed without reporting.
The inventory order is completed when all not yet completed line items are removed.
For completed inventory orders with transport process of Withdraw type you can use the action [Report additional quantity for completed line items]. More information can be found under: Action [Report additional quantity for completed line items].
- Reorganization started – an inventory order receives the general status Reorganization started at the beginning of the reorganization process.
- Invalid – an inventory order receives the general status Invalid during the generation process of its line items. This excludes the possibility that a reporting is already made during the generation process. After generation, the inventory order receives the general status Not in process. If, for technical reasons, the inventory order also retains the general status Invalid, then no processing action can be carried out for the inventory order. An inventory order with the permanent general status Invalid can be deleted. You can then generate a new inventory order by the system. Note the generation status of the inventory order as it may not have been possible to create all the line items.
Output status
Following statuses are possible for inventory order output:
- Not output – the inventory order was not output.
- Output – the inventory order was not output at least once. It is irrelevant whether the output was done with the generation of the inventory order or via the application Inventory orders.
Customizing
For the Inventory orders application, various settings are relevant in the Customizing application, which are described under:
Inventory management function
For the Inventory orders application, various settings are relevant in the Customizing application → Inventory management function.
- Do not assign
- Assign
Serial numbers assigned to put-away or withdrawal are not assigned to inventory order line item. In the inventory order line item, the item appears in its total quantity. The serial numbers must be added manually to the inventory order items in the stock order using the [Add serial number] button. During reporting, the added serial numbers are reported to the upstream process.
Serial numbers assigned to put-away or withdrawal are assigned to inventory order line item. The inventory order line item receives the determined serial numbers as default values.
For a put-away, the creation method in the item master data has priority over the setting in the Customizing application. If the creation method Automatic is defined for the line item, the serial numbers are always assigned to the inventory order line items.
- Open quantity as default (checkbox) – in this field, you can define that the quantity still open is suggested as a default value when reporting an inventory order. For loading units and serial numbers, this causes the checkbox for reporting to be activated already after opening the inventory order.
Warehouse inventory function
The following settings of the Warehouse inventory function under Inventory management function are relevant for the Inventory orders application:
- Manage inventory in logistic units – if this function is activated, then the inventory order line items are generated according to the unit settings and the corresponding column informing about the order becomes available.
Documents function
The following settings of the Documents function under Inventory management function are relevant for the Inventory orders application:
- Automatically output inventory orders – activation of this function means that after the inventory management server generates an inventory order, a batch job is automatically created and generates a voucher for the inventory order.
Storage location control function
Dieses Steuerelement enthält Metadaten und darf nicht gelöscht werden.For the Inventory orders application, various settings are relevant in the Customizing application → Inventory management function.
- Order type for replenishment – in this field, you define an inventory order type for the automatic generation of replenishment orders. If no inventory order type is defined, then no inventory orders are generated for replenishing picking locations.
Business entities
The following business entity is relevant for the Inventory orders application, which you use, for instance, to:
- assign authorizations,
- set up activity definitions,
- export or import data.
Inventory order
com.cisag.app.inventory.obj.TransportOrder
The business entity is part of the following business entity group:
Warehouse Voucher data
com.cisag.app.inventory.OrderData
Authorizations
Authorizations can be assigned by means of authorization roles as well as by assignment of organizations. The authorization concept is described in the technical documentation Authorizations.
Special capabilities
There are no special capabilities for the Inventory orders application.
Organization assignments
If the Content-based authorizations function is activated in the Customizing application, a person can only view the Inventory orders application if an organization that is linked to the Inventory Management structure has been assigned to him or her in the partner master data.
Special features
There are no special features for the Inventory orders application.
Authorizations for business partners
The Inventory orders application is not released for business partners.