Production items are understood as goods (items, parts, materials) which can be produced by a company. The special characteristics and properties of the item can be configurated according to the needs of a given production process.
This document contains information regarding view Production of the application Items. Detailed information regarding the application Items can be found in document <<Items>>.
Working pane
The Production view is composed of the following tabs:
- General
- Texts
- Other fields
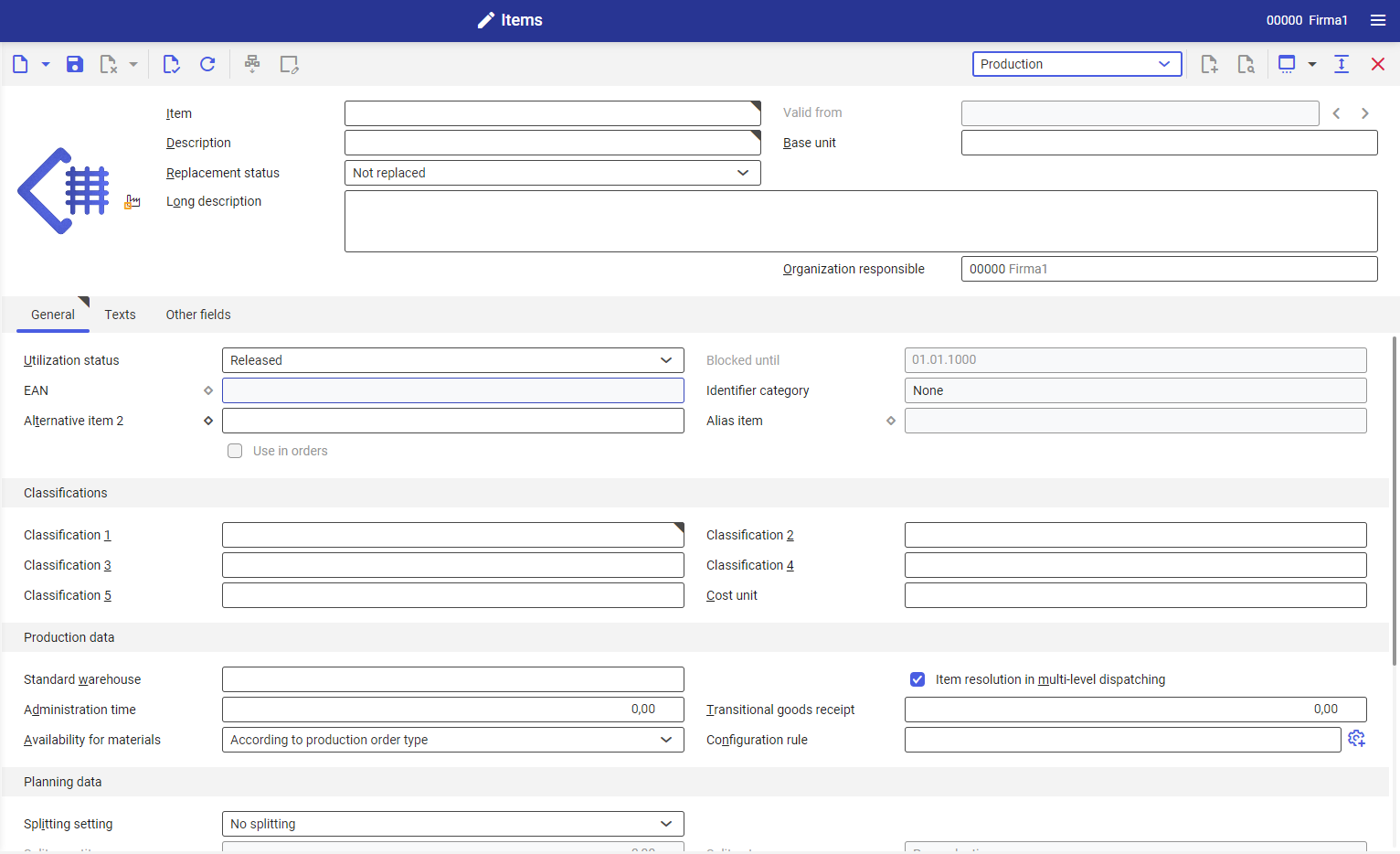
Tab General
Allows for defining the basic data and specifying item status.
Felds Ean, Identifier type, Alias item and use in orders (parameter) are not subject to edition and present data configured in the Base view.

- Alternative item − if no alternative item is selected in the Base view, you can select one or more alternative items in this field.
- Utilization status − here, you can decide whether an item can be used in the production process. Available options:
- Released − in Customizing, Released is default setting for this status. After selecting it, you can use item production data in the production process.
- Blocked − indicates blockade of item production data in the production process. After selecting this option, you also have to set the time point until which the item will be blocked.
- Blocked until − if the production item utilization status is Blocked, enter in this field the date until which the item is to be considered blocked in the production process
Classifications section
Here, you can enter classifications for a given item Assigning an item to a classification facilitates further search of that item as well as its analysis in the production process.

- Classification 1 (mandatory field) − select classification of Product item classification type (e.g., of finished products or of half−finished product, depending on its destination). You can define this type of classification in <<Classifications>> application.
- Classifications 2−5 (optional fields) − allow for additional item classification.
- Cost unit − select an available cost unit. The entered cost unit will be accepted as default in the production order. The cost units allow for a unique identification of costs and are defined in Cost unit application.
Production data section
This section allows for specifying item data important for the production process.

- Standard warehouse − select a warehouse as default for receipts warehouse in the production order.
- Item resolution in multi-level dispatching − parameter checked by default. With this checkbox, you can influence the procedure while dispatching the item if this item is a semifinished good that appears in a bill of material of another item as a finished product. If you deactivate this checkbox, this item is considered to be like a purchasing item and no production order is generated on dispatch. This setting is also applicable for product calculation.
- Transitional time − in this field, you can specify time range before the first operation
- Transitional goods receipt − in this field, you can specify time range in which product availability may be delayed (e.g., because of quality control processes which can affect the number of goods available in the warehouse)
- Availability for materials − here you can specify the availability in the production order. Available options:
- Check as per production order type − the availability check is carried out according to the setting in the production order type from Production order types application.
- Check − the availability is always checked
- Do not check − the availability is not checked
- Configuration rule − assign a configuration rule here if the properties of the item are to be determined during the sales processes or in the production order. Configuration rules are created in <<Product configuration rules>> application.
- [Create item configuration] − enter a standard or example configuration here for the production item if you have entered a configuration rule
Planning data section
This section allows for specifying item data important for the planning process.

- Splitting setting − setting of production order splitting. Available options:
- No splitting − it means that production order will not be divided into further orders. If this option is selected, other fields of the section are not subject to edition.
- Split when generating production recommendations − this field indicates splitting of production order at the moment of generating production recommendation
- Split when generating planning recommendations − this field indicates splitting of production order at the moment of generating planning recommendation
- Split category − the following options are available for selection:
Post−production − means that the partial quantities are scheduled according to the split intervals after the real demand due date
Pre−production − means that the partial quantities are scheduled according to the split intervals before the real demand due date - Split quantity − if you want to complete this item in several orders, enter the split quantity in this field
Example:
The product requirement is 1,050 pcs. The split quantity is 250 pcs. This order is split into 5 orders, that is – 4 x 250 pcs and 1 x 50 pcs.
- Split interval − enter the time between the split orders in this field
- Maximum number of recommendations − here, you can specify the maximum number of planning or production recommendations (depending on the settings of splitting, the field is mandatory if the setting Split when generating production recommendations or Split when generating planning recommendations is selected)
Production method section
This section allows for specifying item production method The production method is necessary for a given item to be considered a production item and used in the production process.

- Category − select the master data necessary for production of this item:
- Bill of material − only one bill of material is necessary for production.
- Bill of material + routing − bill of material and routing are necessary for production.
- Bill of resources − in the item production process, production technology representing combination of material bill and production routing, will be used
In accordance with selected production method, it is necessary to fill−in values in the following fields:
- Bill of material (mandatory field) − allows for assigning specific bill of material to the item. Bills of material are defined in Bills of material application.
- Routing − allows for assigning production routing to an item. Routings are defined in Routings application.
- Bill of resources − allows for assigning production technology to an item. Bills of resources are defined in Bills of resources application.
Alternate methods section
If other production methods are possible for the item’s production, the assignments valid to the routing, bill of material or bill of resources can be selected for each method.

After selecting the button [New], in the table appears new row in which it is possible to determine specific values for columns:
- Production method − here you can select production method (e.g., for external production). Production method is defined in Production methods application.
- Category − here you can define production method category:
- Bill of material
- Bill of material and routing
- Bill of resources
In accordance with selected production method, it is necessary to fill−in values in the following fields:
- Bill of material −allows for specifying an alternate bill of material for the item
- Routing − allows for specifying an alternate routing for the item
- Bill of resources − allows for specifying an alternate bill of resources for the item
Texts tab
In this tab, you can create additional descriptions for an item, which will be important for the production process. They are used when printing production document.

Other fields tab
In Other fields tab, you can enter additional fields, e.g., when it is necessary to specify fields defined by the user, in order to complete the information. The user−defined fields are basically related to the business object and must therefore be defined independent of each other in all views.
