Topic overview
Material requirements planning is a group of processes which allows for planning material requirements on the basis of the data available in the system. Depending on the setting selected in application Items -> Planning view -> Demand coverage, the user decides which business process will execute the demand for a given item and which recommendations should be generated withing planning for a given item:
- Production – the demand for a given item is covered through the production process and planned production recommendations are the final effect
- External purchase – the demand for a given item is covered through the purchase from an external company and planned purchase recommendations are the final effect
- Internal purchase – the demand for a given item is covered through the internal purchase and planned distribution recommendations are the final effect
During the calculations, the planning takes into consideration many factors, e.g., item production and planning data, inventory levels, production plan structures. The purpose of the material requirements planning consists of controlling of the timeliness and the quantity for entered requirements, as well as an appropriate handling of inventory levels and their completing.
Application description
The Material requirements planning application is used to start a new planning run with specified parameters. Material requirements planning results can be stored in the Knowledge Store and reimported and further processed, if necessary.
The Material requirements planning application is composed of a header and work pane.
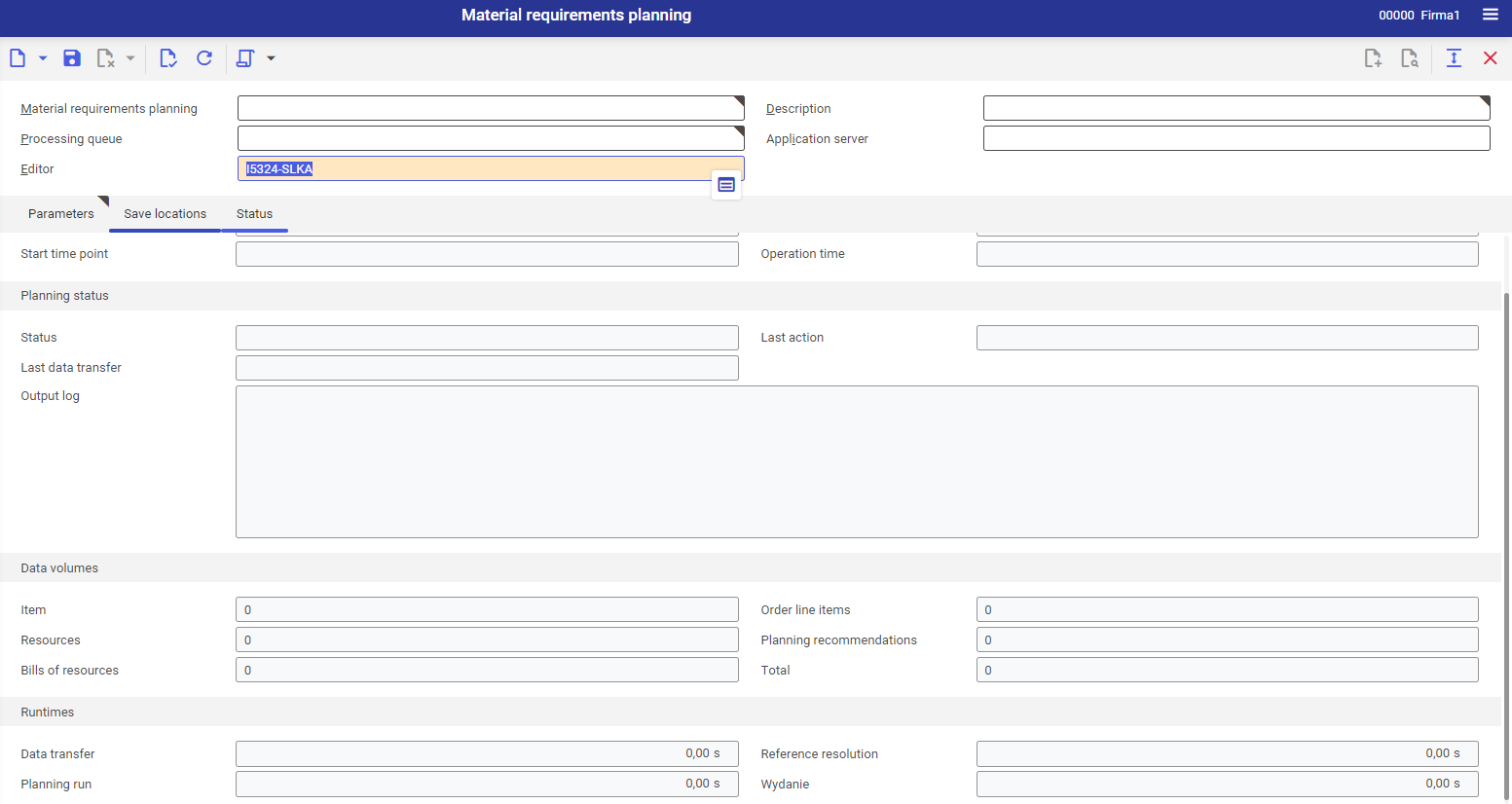
Application header
The application header allows the user to display appropriate material requirements planning data. To do so, select the [Value assistant] button in the Material requirements planning field. The button expands a drop-down list, enabling the selection of planning data.
Once a given item is selected, its corresponding data is displayed in the application header.
Also, the application header makes it possible to define new material requirements planning. To do so, select the [New] or [Duplicate] button.

Selecting the [New] button creates a new form, enabling the user to define particular values in the fields:
- Material requirements planning (required) – define unique identification of the material requirements planning. The identification may consist of digits, letters, or their combinations.
- Description (required) – enter a material requirements planning description, e. an additional name facilitating searching operations
- Processing queue (required) – for executing a material requirements planning run, specify a processing queue used to start planning
- Application server (required) – the ERP system application server on which the material requirements planning will be executed. If the field is empty, the application server is determined via the processing queue.
- Editor – select the editor of the material requirements planning. The employee assigned to the current user is provided as the default. The results of the material requirements planning can be viewed by all authorized users.
Work pane
In the work pane, it is possible to define material requirements planning parameters. Available tabs include:
- Parameters
- Save locations
- Status
Parameters tab
Material requirements planning parameters make it possible to control:
- The planning mode in which the planning server will be started
- The planning horizon
- The planning level of the inventory management criteria on which the user would like to plan
- The demand origin or demand coverage elements to be taken into consideration by the planning
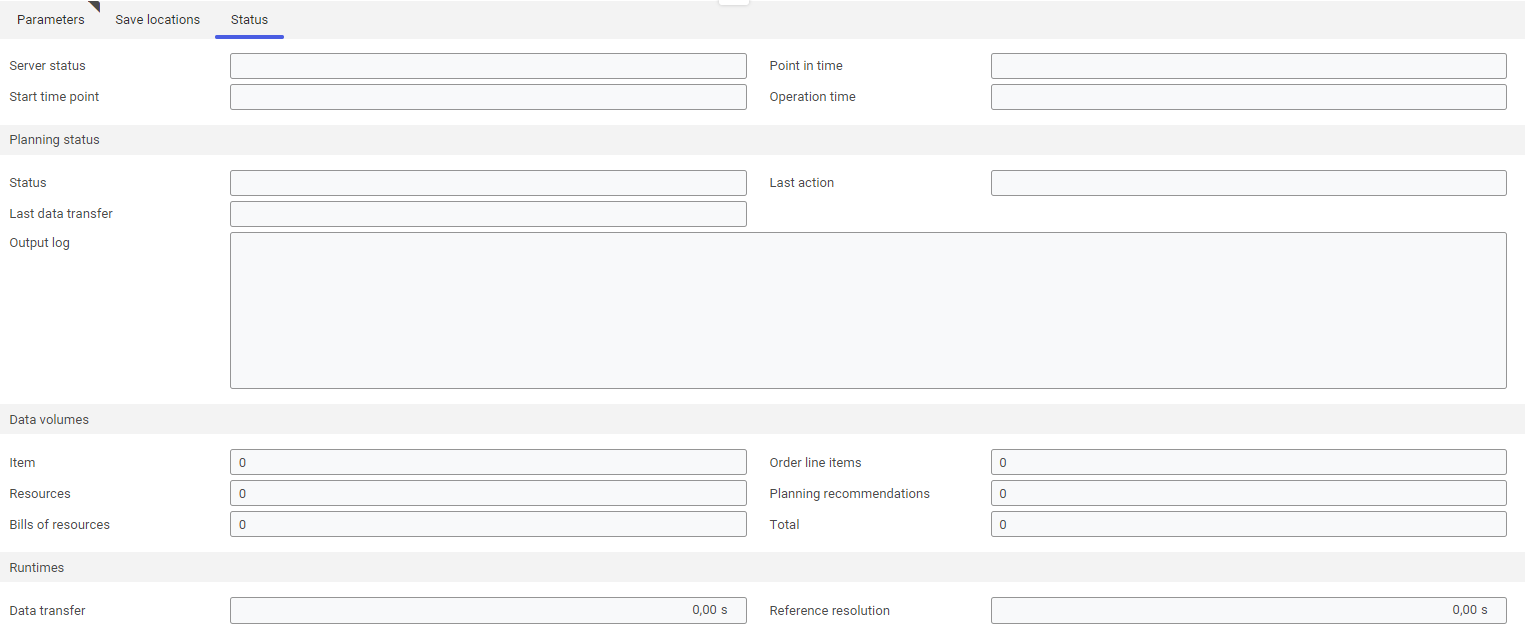
Execution section
- Planning mode (required) – specify the mode in which planning is to be performed:
- Prepare planning
It starts the batch job. Data is not transferred and planning is not performed. - Execute planning
It starts the batch job and executes a complete planning run preceded by the transfer of all data. - Update planning
It repeats the planning. This allows the material requirements planning to be updated automatically at definable intervals.
- Prepare planning
- Update interval – specify the update interval in a time unit. The planning server will update the material requirements planning according to the specified time. The interval defines the period between the start of two planning runs.
Simulation section
- Simulation – this parameter allows planning to be run in the simulation mode, in which only forecasts are taken into account by the system. Based on such a simulation, it is possible to generate a material availability date. Moreover, no planning recommendations can be generated from material requirements planning runs with the Simulation parameter active.
- Planning start – it allows defining the start date of a planning simulation
Scheduling section
- Offset – it specifies the planning offset from the current date. Data may be entered in one of the units day or week. By default, the day unit is selected. It is possible to enter negative values.
- Planning horizon (required) – in this field, specify the desired planning horizon (in calendar days)
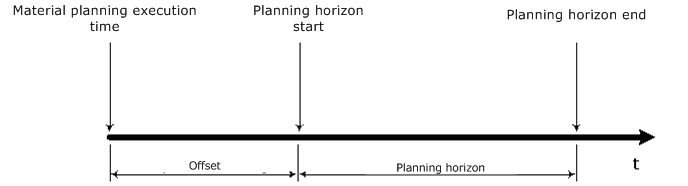
Planning data section
- Sites (required) – select which sites (inventory logistics organizations) are to be considered in the planning. At least one site must be selected. A site is also assigned to each warehouse in a multi-site environment.
- Owners of inventory – choose the inventory owners for which inventories and their availability data are to be considered in the planning. Exclude inventories that should not be available from the planning perspective.
- Use suppliers as demand coverages (parameter) – select this parameter if supplier inventories are to be taken into account in the planning. If the parameter is deactivated, supplier inventories are not taken into account. The parameter is available if the Multiple inventory owners function is activated in Customizing → Inventory Management.
- Suppliers – specify suppliers whose inventories are to be taken into account in the planning. If the field is not filled in, the inventories of all suppliers are used.
- Forecast type – if required, select an existing demand forecast created in the Demand forecast types application. When starting a planning run, a demand forecast creates virtual demands in the system, with quantities based on forecast settings.
- Planner – if required, select an existing employee as a planner. Only the items assigned to this planner and all unassigned items (with no planner entered) are considered for planning. The planner may be selected in the Planning view of the Items application.
- Warehouse – if required, select an existing warehouse. Only the inventories of the selected warehouse will be considered for the planning.
- Warehouse classification – if required, select an existing warehouse classification (national, international)
- Production recommendations – select which production recommendations are to be considered in the current planning according to their status:
- All
- Created
- Blocked
- In process
- Released
By default, none of the options is selected.
- Purchasing recommendations – select which purchasing recommendations are to be considered in the current planning according to their status:
- All
- Created
- Blocked
- In process
- Released
- Distribution recommendations – select which distribution recommendations are to be considered in the current planning according to their status:
- All
- Created
- Blocked
- In process
- Released
- Sales recommendations – select which sales recommendations are to be considered in the current planning according to their status:
- All
- Created
- Blocked
- In process
- Released
- Availability rule (required) – select an existing availability rule. The definitions of availability rules determine the line items of a selected order type that are considered as the demand origin or demand coverage elements. Availability rules can be defined in the Availability rules application.
Planning section
- Requirements planning – it allows the user to specify which planning data (from the Planning view of the Items application) is to be considered. Available options:
- All
- Lot size
- Minimum inventory level
- Reorder level
- Level – select a planning level:
- Item
The inventory management criteria Minimum inventory level, Reorder level, and Lot size are retrieved from item planning data. - Item + Warehouse
The inventory management criteria Minimum inventory level, Reorder level, and Lot size are retrieved from the Warehouse data section in the Planning view of the Items application.
- Item
- Forecast distribution – adjust settings for the distribution of planning forecast quantities:
- Even distribution:
The requirement quantity is distributed proportionally over the individual work days of a relevant period (week/month). - First work day of the period:
The requirement quantity is set to the first work day of a relevant period (week/month). - Last work day of the period:
The requirement quantity is set to the last work day of a relevant period (week/month). - Mid-period:
The requirement quantity is set to the work day of a relevant period (week/month) closest to the middle of the period. The middle of the period is Wednesday for a weekly forecast, and the 15th day of the month for a monthly forecast.
- Even distribution:
- Prior period’s forecast results – specify the mode for settling forecasts with respect to the previous period:
- Issues only:
Issues of materials will be included as the demand for the previous period; the difference relative to the forecast values will be credited to the first planning period. - Forecasts and issues:
Forecasts and issues of materials will be included as the demand for the previous period.
- Issues only:
- Buffer time reduction – specify a value for the buffer time reduction. The planning will reduce buffer times (idle periods before of after an operation) defined for all operations by this value. In the case of operations for which a maximum buffer time reduction has been specified, the times may not be reduced.
- Capacity limit – this parameter may be used to activate planning with capacity limit. By default, the parameter is deactivated.
- Round up dynamic lot size – if this parameter is deactivated, only the setting from the lot size method defined in the Items application is considered. If the Exact lot size method is selected there, a planning recommendation is always rounded up to this exact lot size. If the Coverage time lot size method is selected, only the coverage time is considered. In turn, if the Round up dynamic lot size is selected, the coverage time will be used to determine the demand and then the requirements quantity for the planning recommendation is rounded up to the lot size.
- Multi-site requirements calculation – activating this parameter enables the generation of multi-site requirements. By default, the parameter is not selected.
- Planning data for configured item – if this parameter is selected, no separate planning recommendations are created for configured demands in the planning. The lot size method and all other planning data from the item master data are evaluated. One of the following lot size methods must be selected in the Planning view of the Items application:
- Demand
- Exact lot size
- A lot size or higher demand
- Coverage time
- Weekly lot
- Monthly lot
If the Demand lot size method has been selected, separate planning recommendations are created for each configured item created as a result of product configuration rules.
- Offset planned receipts against demands – in the end-of-period material requirements planning, excess allocations will be reduced again by reducing the number of planning recommendations. Select one of the following options:
- No additional validation and offset
No additional offset will be used if this option is selected. - Validation and offset with possible safety inventory level shortage
If the are shortages within the minimum or safety inventory levels, the planning recommendation either will not be reduced or will be reduced only to the minimum or safety inventory level. - Validation and offset without safety inventory level shortage
The minimum and safety inventory levels cannot have shortages. Inventory levels cannot be negative.
- No additional validation and offset
- Log untransferred line items – in some cases, bill of material line items will not be accepted for planning. Using this parameter, it is possible to determine whether relevant (untransferred) bill of material line items should be processed. If the parameter is selected, the planning error log will list untransfered bill of material line items.
- Recommendations in case of blocked item view – if this parameter is selected, recommendations will be generated also in the case where the Inventory Management or Purchasing and Production views of the Items application are blocked. However, it will not be possible to generate orders from such recommendations.
- Include demands of the inventory owners – if inventory is owned by a different organization, the system will take its demand for given items into account and will calculate recommendations on their basis
- Optimization in case of shortage in reorder level – if this parameter is selected, two new recommendations will be created. The first one will cover shortages in the reorder stock level, while the second one will cover the demand quantity. See the article New algorithm for planning a reorder level for more details.
- Plan inventoried packaging units – if this parameter is selected, the system will consider demand for packages when planning. The Material requirements query application will make it possible to preview item planning data and verify planning for packages, thus including a relevant quantity calculation.
- Note resource reservation settings – if this parameter is selected, the system will consider the reserved work time of resources when recalculating planning.
Save locations tab
On the Save locations tab, it is possible to specify a file for the error log and a backup file. Both the files will be located in the Knowledge Store. Two file formats – *.doc and *.txt – can be used. As material requirements planning is performed, these files will be generated automatically, if they do not yet exist.

- Log file – specify an existing or new log file in the Knowledge Store. Error messages generated in the course of the material requirements planning will be contained in this log file. If the specified file does not exist yet, it will be created automatically when performing the [Transfer planning data and execute planning] action.
- Link to log file – this field shows the link to the generated planning log file in the Knowledge Store. Use this link to open the log file.
- Backup file – specify an existing or new file in the Knowledge Store. The entire material requirements planning data set is stored in this backup file. If the specified file does not exist yet, it will be created automatically when performing the [Save backup file] action. It is recommended to save planning data in the backup file on a regular basis.
Status tab
The Status tab presents the current operational status of the planning server and of the material requirements planning itself, as well as the data volume of the material requirements planning.
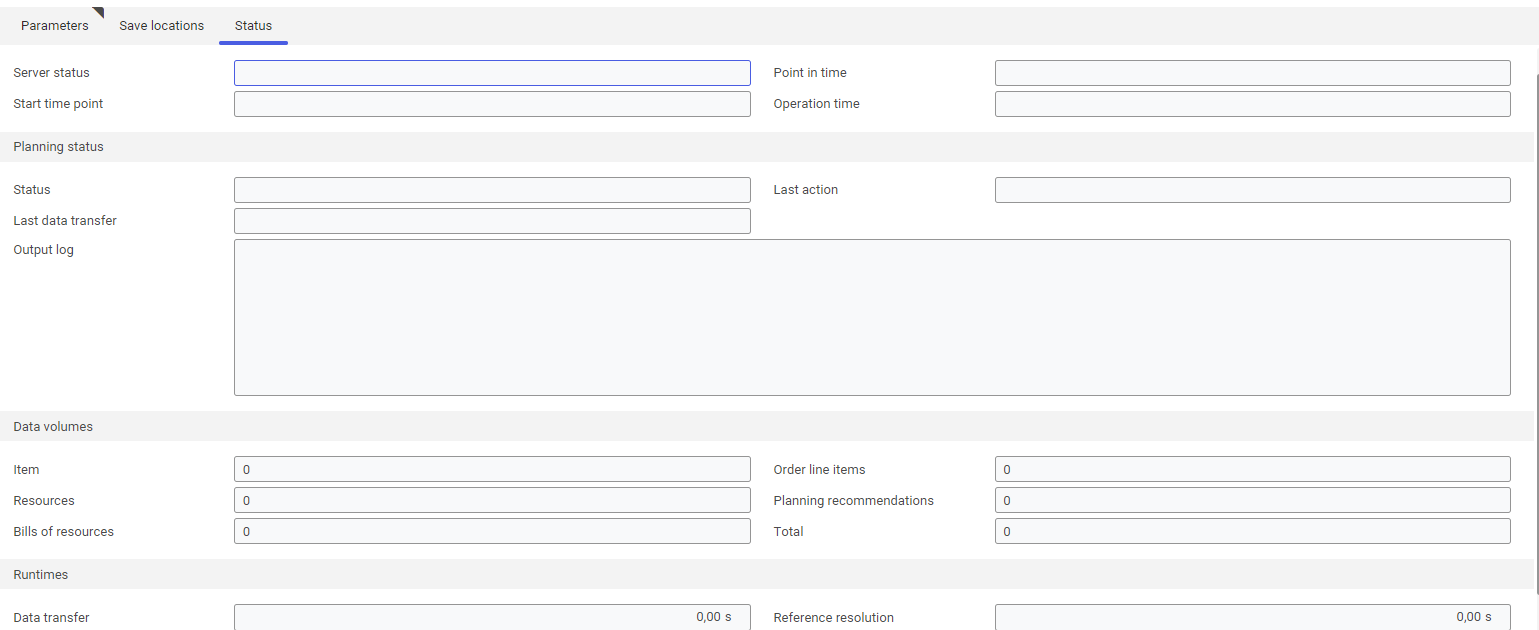
Planning server status section
- Server status – this field displays the status of the planning server. Available statuses include:
- Running
- Out of operation
- Starting
The field is non-editable. In order to change the status of the planning server, it is necessary to perform the action [Restart planning server] or [Stop planning server].
- Point in time – the current time point of the status server. The time point is shown with a precision of milliseconds.
- Start time point – the start time point of the planning server. The time point is shown with a precision of milliseconds. If the planning server is not running, the field is empty.
- Operation time – the duration since the last start time point of the planning server. The time point is shown with a precision of milliseconds. If the planning server is not running, the field is empty.
Planning status section
Available fields:
- Status – during a planning run, this field displays the actions currently being executed, e.g. Configuring APS, Transferring item resources, Transferring bill of resources and structure data. The planning run is then closed correctly, if the Waiting for user requirement status is indicated.
- Last action – this field indicates the last correctly executed action, e.g. APS configuration was performed, Resources were transferred, etc. The planning run is then closed correctly, if the Material requirements planning was performed or Determined conflicts were saved status is indicated.
- Last data transfer – this field displays the date and time of the last data transfer from the OLTP database or the last update from the backup file
- Output log – this field displays any fatal errors that have occurred. In general, these represent interruption conditions for the planning. This field also provides a general error message, if problems prevented individual items from having been planned.
Data volumes section
Available fields:
- Items – the number of items transferred from the OLTP database
- Order line items – the number of order line items transferred from the OLTP database
- Resources – the amount of resources transferred from the OLTP database
- Planning recommendations – the number of generated production recommendations
- Bills of resources – the number of production structures (bills of material, routings, bills of resources) transferred from the OLTP database
- Total – the amount of data (items, order line items, resources, production structures) transferred from the OLTP database
Runtimes section
Available fields:
- Data transfer – the runtime of the data transfer (in seconds)
- Reference resolution – the runtime for the reference resolution within the planning (in seconds)
- Planning run – the runtime for the effective planning run (in seconds)
- Issue – issue time (in seconds)
Material requirements planning process
A new material requirements planning process is started by the [Transfer planning data and execute planning] action. When a new planning process is started, the existing data set of a preceding planning run of the same material requirements planning, if any, is first deleted. Select the abovementioned action if the planning parameters have been changed.
To update a previously performed planning run with data revised since the last data transfer, select the [Update planning data and execute planning] action.
To repeat a planning run without any change in the input data, the user may select the [Re-execute planning] action.
The action [Update planning] is used to update planning recommendations and repeat the planning run. It is possible to modify planning data (in other applications, e.g. Material requirements query) and plan on the basis of modified requirements any number of times.
When the planning processed is closed, the following actions can be started:
- Automatic generation of production recommendations for the generation of production orders
- Automatic generation of purchasing recommendations (external) for the generation of purchase orders and purchasing RFQs
- Automatic generation of distribution recommendations (internal and only in multi-site environments) for the generation of distribution orders
- Planning data update
- Repeating of the primary and secondary requirements calculations
- Saving of the relevant production planning data set
Application-related actions
The following actions are available in the Material requirements planning application:
- [Transfer planning data and execute planning]
- [Update planning data and execute planning]
- [Re-execute planning]
- [Open backup file]
- [Save backup file]
- [Restart planning server]
- [Stop planning server]
Transfer planning data and execute planning
This action is used to completely restructure and repeat a planning run. Any existing planning data is deleted.
- All master data required for the planning (items, resources, company calendars, etc.) is transferred from the OLTP database
- The current inventories as well as the existing recommendations based on the restriction (with a status other than Created) and all demand origin or demand coverage elements based on the availability rules are transferred
- Forecast data is transferred
- The total planning including primary requirements and secondary requirements calculation is performed
- New planning recommendations are created
- Planned resource reservations resulting from the planning recommendations are created
Update planning data and execute planning
This action retrieves all planning-relevant changes, transfers them to the planning data set, and updates the planning. Changes to the following master data and/or demand origin or demand coverage elements are transferred:
- Company calendar
- Demand forecasts
- Resources/resource groups
- Items
- Inventories
- Sales quotations
- Sales orders
- Purchasing RFQs
- Purchase orders
- Production orders
- Purchasing recommendations
- Distribution recommendations (only in multi-site environments)
Changes to the following master data are not transferred or considered when planning is updated:
- Time models
- Week time models
- Resource capacities
If purchasing, distribution or production recommendations were generated from a planning recommendation, they are considered independent data. In order to share and use such data in a planning operation, it is necessary to mark them with planning parameters.
Recommendations can be selected and included according to their categories and statuses:
Category:
- Purchasing recommendations
- Distribution recommendations
- Production recommendations
Status:
- Created
- Blocked
- In process
- Released
Sales recommendations can be included in a planning operation only as a requirement origin. Such recommendations are not generated within a planning operation.
The user generated a purchasing recommendation from a planning recommendation and modified the due date and quantity specified for it. The change is to be included in another planning operation. The user automatically changes the status of the purchasing recommendation to In process. The manual change is taken into consideration only if the purchasing recommendation is included according to planning parameters and the user executes the action [Update planning data and execute planning]. Then, the purchasing recommendation is considered as demand coverage.
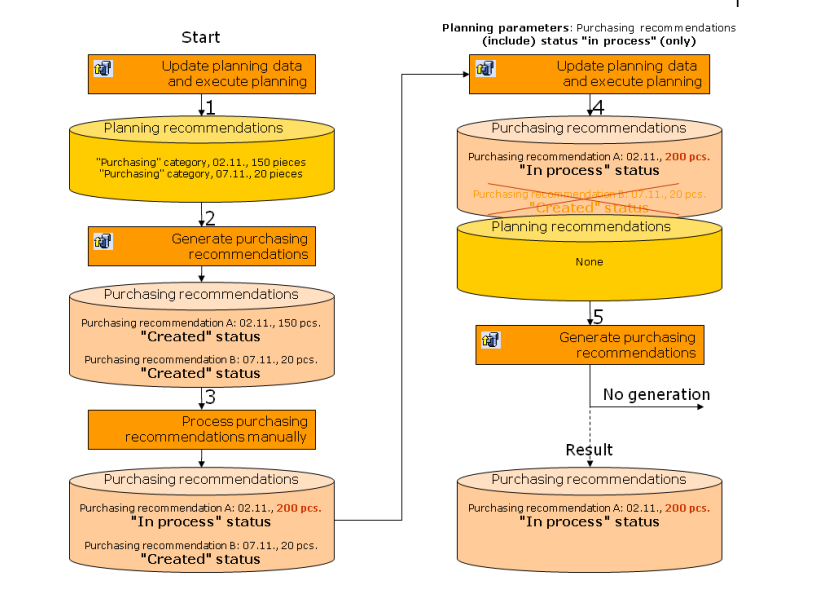
If an existing purchasing recommendation is not used by the planning operation (purchasing recommendation B in the example), the system considers it as non-existing and deletes it. New planning recommendations are generated. If necessary, it is possible to generate more purchasing recommendations from new planning recommendations. The planning does not affect only the operation of generating purchasing orders from a purchasing recommendation (or purchasing RFQs).
Re-execute planning
This action deletes existing planning recommendations (except for purchasing, distribution and production recommendations) and re-executes planning. This action also generates new planning recommendations. Associated secondary demands are also subject to the re-execution of planning.
If the user has already generated a purchasing, production or distribution recommendation from a planning recommendation, such recommendations are marked with a flag. Further purchasing, production or distribution recommendations cannot be generated from flagged planning recommendations.
If corresponding production, purchasing and distribution recommendations were generated from the planning recommendation and the [Re-execute] planning action was performed, the flagged planning recommendations are deleted and the system generates new, not flagged, planning recommendations. Then, these planning recommendations are included during another generation of production, purchasing or distribution recommendations (or during each further repetition of these actions).
It is also possible to modify calculated planning recommendations manually. The user can also make use of the Material requirements query and make planning according to their own changes with the use of the [Update planning] action.
The Discard changes action in the Material requirements query is of use only if the user has carried out manual changes in the planning recommendations and wishes to discard them.
Open backup file
Planning data sets are located in a file stored in the Knowledge Store. The file is non-editable.
Save backup file
This action allows planning data sets to be saved in a file and stored in the Knowledge Store. The file is non-editable.
The entire material requirements planning data set is stored in this backup file.
Reset planning server
Each time the planning server is restarted, a batch job is generated for the Start planning environment batch application.
If the batch job is canceled or deleted manually in the Batch jobs application, the corresponding planning server cannot be started until the ERP system application server has been restarted.
During the starting operation, the status of the planning server is set as Starting. After the successful start, the status changes to Running.
Stop planning server
This action stops and deactivates the planning server.
After the planning server stops, its status is set as Out of operation.
Authorizations
Authorizations to planning processes and all the particular actions can be assigned by means of authorization roles as well as by assignment of organizations. The authorization concept is described in the Authorizations article.