Topic overview
The Cockpit: Planning conflicts application allows the user to preview planning conflicts that occurred in the course of material requirements planning. Either all or only selected demand origin/coverage elements are displayed. The application contains:
- Application header – it contains buttons and fields for filtering data displayed in the work pane’s table
- Work pane – it contains a table displaying data according to search criteria entered in the header
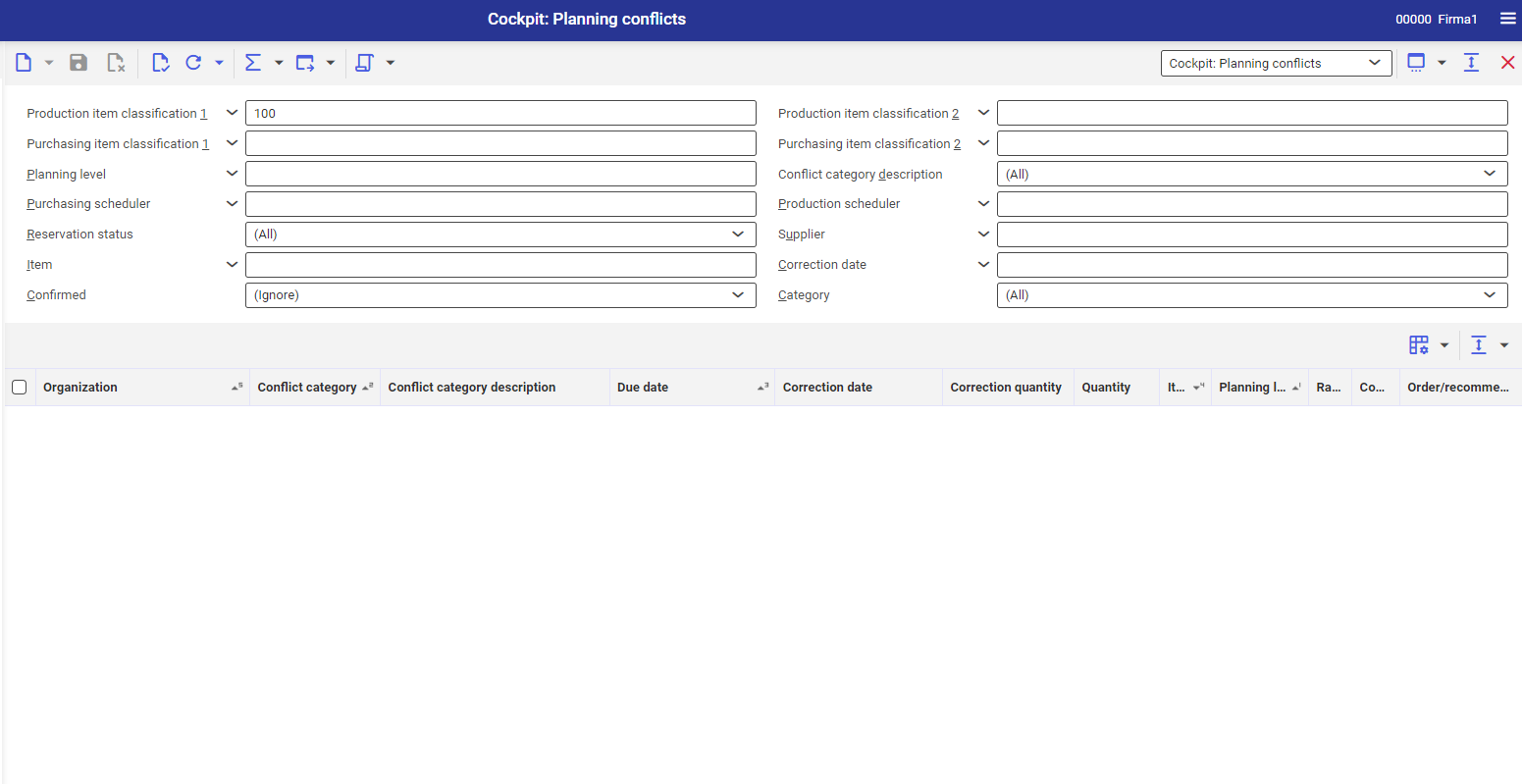
Application header
The application header is composed of the following buttons:
- [New] – opens empty cockpit sheet
- [Validate] – allows for verifying the correctness of the data entered in the application
- [Refresh] – refreshes the data in the table
- [Refresh] → [Refresh (background)] – refreshes the data in the table in background
- [Refresh] → [Stop] – if there is a big amount of updated data, it allows for stopping its refreshment in background
- [Refresh] → [Count objects] – the system calculates the quantities of line items corresponding to entered criteria. The information is displayed as a message.
- [Calculate and display totals] → [All objects] – sums up all records displayed in the window. The total is presented as a separate row in the bottom of the table. The Quantity and Correction quantity values are summed up.
- [Calculate and display totals] → [All objects with group totals] – sums up all record groups displayed in the window. The total is displayed in an additional row below each group. The Quantity and Correction quantity values are summed up.
- [Calculate and display totals] → [Selected objects] – sums up records selected in the first column of the table. The total is displayed in an additional row. The Quantity and Correction quantity values are summed up.
- [Calculate and display totals] → [Hide totals] – hides row with summed up sums
- [Export] – allows for exporting data to a file. Detailed description can be found in article: Export data.
- [Export] → [Export displayed objects]
- [Export] → [Export objects according to search criteria]
- [Export] → [Copy hyperlink with search criteria]
- [Select action] → [Confirmed] – allows for accepting a conflict
In the application, it is possible to filter data according to the following information:
- Production item classification 1 – here, it is necessary to select the classification as a search criterion. Classification from the category Production item classification 1 are admissible.
- Production item classification 2 – here, it is necessary to select the classification as a search criterion. Classification from the category Production item classification 2 are admissible.
- Purchasing item classification 1 – here, it is necessary to select the classification as a search criterion. Classification from the category Purchasing item classification 1 are admissible.
- Purchasing item classification 2 – here, it is necessary to select the classification as a search criterion. Classification from the category Purchasing item classification 2 are admissible.
- Planning level – here, it is necessary to enter the planning level for which planning conflicts are to be displayed
- Conflict category description – here, it is necessary to select conflict categories. Available import options:
- Finished goods/demand in previous period
- Semi-finished goods/demand in previous period
- Start/order date in previous period
- Purchasing/demand in previous period
- Purchasing/order in previous period
- Delayed production due date
- Delayed planning recommendation date
- Early order/recommendation due date
- Delayed order/recommendation date
- Quantity of order/recommendation too high
- Quantity of order/recommendation too small
- Order/recommendation not required
- Shortfall of minimum inventory level in planning time fence
- Quantity of order/recommendation too high in planning time fence
- Order/recommendation not required in planning time fence
- Excess inventory due to lot size or order
- Purchasing/RFQ in previous period
- Delayed date of order/recommendation due to the transition time goods receipt
- Minimum inventory level undershoot after adaptation of the production recommendation
- Reorder level undershoot after adaptation of the production recommendation
- (other)
Conflict categories are described in detail in the Descriptions of material planning conflict categories chapter.
- Purchasing scheduler – here, it is necessary to select the purchasing scheduler. This allows for limiting the planning conflicts for particular items. The purchasing scheduler is assigned in the item planning data.
- Production scheduler – here, it is necessary to select the production scheduler. This allows for limiting the planning conflicts for particular items. The production scheduler is assigned in the item planning data.
- Reservation status – here, it is necessary so specify planning conflicts based on the origin reservation status and sources of demand coverage. Possible statuses are:
- Not reserved
- Partially reserved
- Completely reserved
- (other)
- Supplier – here, it is necessary to enter the supplier for which planning conflicts are to be displayed. The supplier is assigned in the item planning data.
- Item – here, it is necessary to enter the item for which planning conflicts are to be displayed
- Correction date – here, it is necessary to specify the correction date for which planning conflicts are to be displayed
- Confirmed – allows for deciding whether already confirmed conflicts should be displayed. It is possible to select one of the following options:
- Yes
- No
- Ignore
- Category – here, it is necessary to select the category of origin or demand coverage. The following categories are available:
- Unspecified demands
- Demand forecast
- Sales orders
- Material requirements for released production orders
- Purchase orders
- Released production order
- Entered production order
- Planning recommendation
- Secondary requirements
- Co-product
- Purchasing recommendation
- Manually changed production recommendation
- Production recommendation
- Distribution recommendation
- Issue from distribution order
- Receipts from distribution recommendation
- Planned issue from distribution recommendation
- Receipts from distribution recommendation
- Issue from distribution recommendation
- Sales recommendation
- Issue completed
- Secondary requirements for kit items
- Receipt via kit components
- Material demand in picking order
- Inventory requisition receipt
- Issue from inventory requisition
- Purchasing RFQs
- Issue due to unpacking
- Receipts due to unpacking
- Planned proposal from cross-site production
- Material requirement planning – allows for selecting material requirement planning for which planning conflicts are to be displayed
- Purchasing scheduler – allows for filtering planning conflict assigned to a selected scheduler
- Organization – allows for displaying planning conflicts occurring for a selected organization
Work pane
The work pane is composed of a table displaying the results containing planning conflicts. Additionally, on the work pane toolbar, the following buttons are available:
- [Hide/Show ranges] – allows for modifying displayed table, the following options are available:
- Hide/Show list header – hides/shows the descriptions of table columns
- Hide/Show line status – hides/shows the column with the line status
- Show grouping and sort area – allows for dragging the name of a column onto the area displayed above the table header and grouping data by selected attribute, as well as for hiding an area
- Expand all groups – expands line items grouped in the table
- Reduce all groups – reduces line items grouped in the table
- Show all areas – displays all columns and descriptions
- Hide all areas – hides all columns and descriptions
The application table displays data in accordance with the filter entered in the application header.
Description of material planning conflict categories
A base planning date and the date of the first planning period are important for determining a conflict. The base date is defined on the basis of a planning run’s creation date, taking offset into account.
Finished goods/demand in previous period
It refers to sales quotations and orders whose shipping date falls within a previous period.
Depending on the material requirements planning level of a given item, a distinction is made as to whether the item is a finished or semi-finished product. If the item does not contain any semi-finished goods, the material requirements planning is carried out at the level 1. This means that the system will generate demand recommendations only for materials needed to produce the final product. However, if semi-finished goods are also included in the end product, their planning takes place at subsequent levels (>1) and consequently the semi-finished goods are also included in the planning.
Semi-finished goods/demand in previous period
It refers to:
- material reservations of released production orders whose date falls within a previous period
- sales quotations and sales order items whose shipping date falls within a previous period
- additional production requirements (secondary requirements) for semi-finished goods determined in the course of material requirements planning that fall, along with a requirement date, within a previous period, i.e. before the first planning period
Start/order date in previous period
It refers to planning recommendations whose start date falls within a previous period. The system then makes no distinction between production, purchasing, and distribution recommendations.
Purchasing/demand in previous period
This conflict category refers to:
- order recommendations whose shipping date falls within a previous period
- planned order recommendations whose due date falls within a previous period
Purchasing/order in previous period
It refers to purchasing recommendations whose delivery date falls within a previous planning period.
Delayed production due date
It refers to:
- receipts originating from released production orders whose end date falls within a previous period
- started production orders for semi-finished goods whose end date falls within a previous period
Delayed planning recommendation date
This conflict category for planning recommendations occurs when the recommendation date is set to a day later than the associated demand origin due to the planning time fence or a holiday.
Early order/recommendation due date
This conflict category occurs for receipts originating from orders or recommendations if the receipt date is earlier than the date of a demand origin. This conflict may be caused, for instance, by moving a sales order into the future after a production or purchasing recommendation has already been generated.
Delayed order/recommendation date
This conflict occurs if sufficient quantities are available in the planning horizon but the order receipt date is later than the demand origin date. This problem mainly arises when there are delays in deliveries from suppliers or production due dates are shifted.
Quantity of order/recommendation too high
The primary planning goal is to accurately meet the demand for a given item within the planning horizon. If the quantities of demand origins (e.g. sales order items) decrease, the quantity of associated demand coverage is too high. Since quantity cannot be automatically adjusted to planning and purchasing recommendations already created, this conflict is displayed if some quantity is no longer required. A correction quantity is recommended in case of this conflict.
Order/recommendation not required
This conflict arises when demand coverage is no longer needed to cover a required quantity in the planning horizon because demand origins no longer exist. An order/recommendation may be deleted.
Shortfall of minimum inventory level in planning time fence
This conflict category always arises when the demand date falls within the planning time fence but the quantity resulting from the demand leads to a deficit in the minimum inventory level.
Quantity of order/recommendation too high in planning time fence
This conflict is visible for generated recommendations and orders if their date falls within the planning period and the inventory available at the end of the period exceeds the minimum level. The surplus is less than the quantity of the recommendation or order.
Order/recommendation not required in planning time fence
This conflict category is visible for generated recommendations and orders when their date falls within the planning time fence and the available inventory exceeds the minimum level at the end of the period. This surplus is so high that the recommendation or order is no longer needed.
Excess inventory due to lot size or order
This conflict category is similar to Quantity of order/recommendation too high in planning time fence. However, in this case, it is not possible to recommend a correction quantity because the lot size does not allow the quantity to be changed. Even if the order quantity deviates from the established lot size, no correction quantity is shown.
Purchasing/RFQ in previous period
This conflict category becomes visible for generated recommendations and orders when their delivery date falls within a previous planning period.
Delayed date of order/recommendation due to the transition time goods receipt
This planning conflict category refers to a case where sufficient quantities are available within the planning horizon but the order receipt date is later than the demand origin date due to the transition time before the receipt of goods in the warehouse.
Minimum inventory level undershoot after adaptation of the production recommendation
This planning conflict category refers to a case where a planning recommendation, created after stock levels dropped below a minimum inventory level, is to be reduced or deleted. This may occur if the Optimization in case of shortage in reorder level parameter is activated.
Reorder level undershoot after adaptation of the production recommendation
This planning category refers to a case where a planning recommendation, created after stock levels dropped below a reorder level, is to be reduced or deleted. This may occur if the Optimization in case of shortage in reorder level parameter is activated.
Data export
Action [Export] → [Export displayed objects]
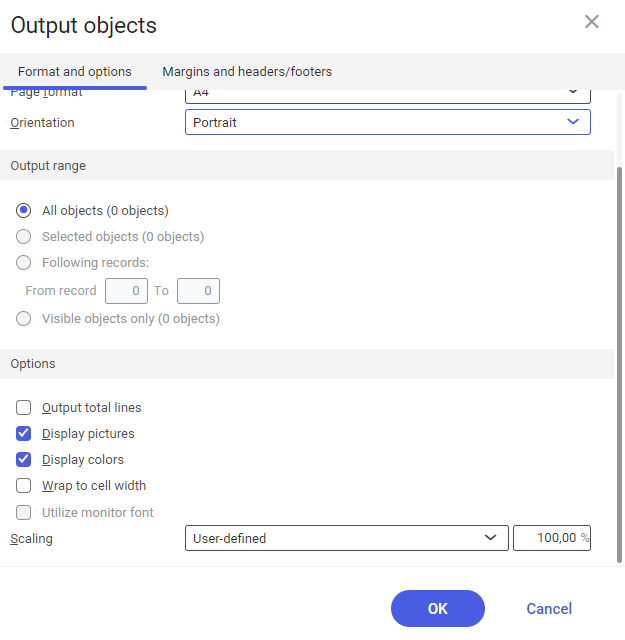
It allows for exporting data currently displayed in the table. Opens the Output objects dialog window. The dialog window is composed of the following tabs, areas and fields:
- Tab Format and options – allows for defining particular export settings
- Section Output format – allows for defining the basic settings of the document format and orientation. The section is composed of the following fields:
- Format – allows for selecting the format of the file to which the data is to be exported. Possible formats are XLS or PDF.
- Page format – allows for selecting the sheet size. Available values are A4 and A3.
- Orientation – allows for selecting the orientation of an exported document. Available options are Portrait and Landscape
- Section Output range – allows for selecting the range of exported data. The section is composed of the following fields:
- All objects – allows for exporting all records from the table.
- Selected objects – allows for exporting only selected objects from the table
- Following records – allows for selecting defining table line items to export in fields From record/To.
- Visible objects only – allows for exporting the data visible in the table
- Section Options – allows for defining additional export options:
- Output total lines – exports data along with the lines displaying totals
- Display pictures – exports data along with its photos
- Display colors – exports data in color
- Wrap to cell width – exports data in the table with text content wrapped according to defined column width
- Utilize monitor font – exports data in defined font used in the system
- Scaling – allows for scaling the view of exported data. The automatic scaling selects the value by itself and no scaling sets the value to 100%. The non-standard scaling allows for editing the percentage of the view scaling.
- Tab Margins and headers/footers – allows for defining the size of the margin and the type of the data which is to be displayed in the header and in the footer.
- Section Output format – allows for defining the basic settings of the document format and orientation. The section is composed of the following fields:
Action [Export] → [Export objects according to search criteria]
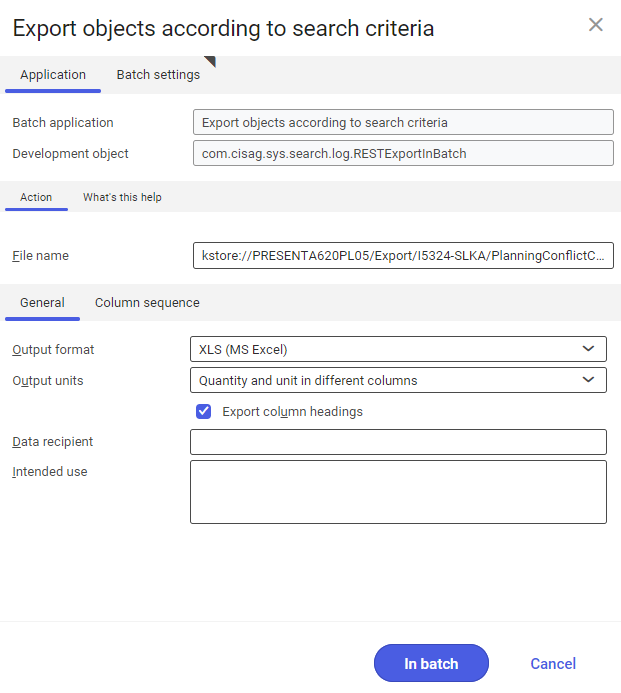
Allows for exporting data according to set data filtering criteria. Displays the Export objects according to search criteria dialog window. The dialog window is composed of the following tabs, areas and fields:
- Tab Application – allows for defining particular export settings
- Batch application – defines the application which will be started in background in order to export data.
- Development object – technical name of the application responsible for the data export
- Section Action – contains File name filed, where it is necessary to specify the path of the target folder and the name of the file with exported data.
- Tab General – allows for defining the format of exported data.
- Output format – allows for defining the format of the file in which the data will be exported. Available formats: XLS, XLSX, CSV, XML, HTML.
- Output units – allows for defining the method of presenting units on the export document. Quantity and its unit can be exported in one column or in two separate columns.
- Export column headings (parameter) – if this parameter is checked, the data is exported with the names of the columns of the table
- Data recipient – allows for adding the data recipient to the application logs
- Intended use – allows for adding the purpose of the data export to the application logs
- Tab Column sequence – allows for defining the order of columns in the export file
- Tab Settings – allows for defining the settings of the batch job
Action [Export] → [Copy hyperlink with search criteria]
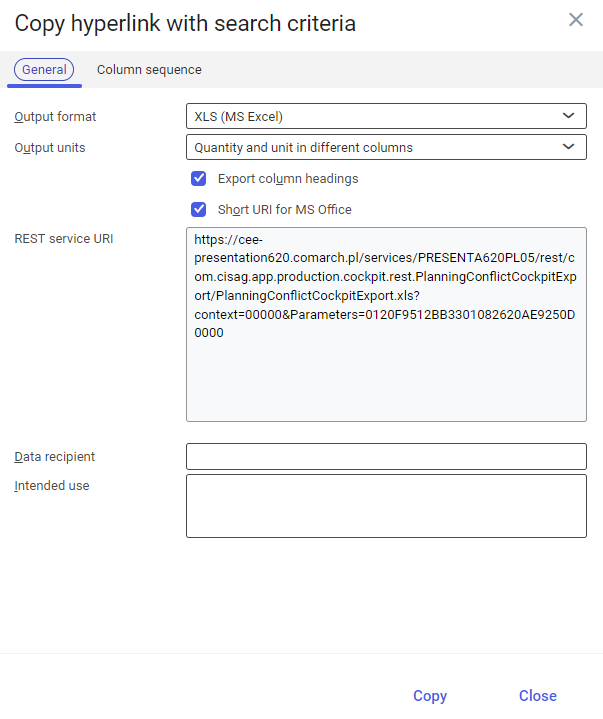
This action allows for generating a hyperlink which, after being pasted in the browser, allows for retrieving the defined data file. After selecting the action, the Copy hyperlink with search criteria dialog window is displayed. The dialog window is composed of the following tabs:
- Tab General – allows for defining the format of exported data.
- Output format – allows for defining the format of the file in which the data will be exported. Available formats: XLS, XLSX, CSV, XML, HTML.
- Output units – allows for defining the method of presenting units on the export document. Quantity and its unit can be exported in one column or in two separate columns.
- Export column headings (parameter) – if this parameter is checked, the data is exported with the names of the columns of the table
- Short URI for MS Office (parameter) – allows for generating a shortened URI
- REST service URI – link address which, after being copied, will allow for retrieving the data file
- Data recipient – allows for adding the data recipient to the application logs
- Intended use – allows for adding the purpose of the data export to the application logs
- Tab Column sequence – allows for defining the order of columns in the export file
Customizing
The Cockpit: Planning conflicts application requires no additional settings in the Customizing application.
Business entities
No business entity has authorizations to this application.
Special capabilities
The Cockpit: Planning conflicts application has no special capabilities.
Organizational assignments
Organization structures are used to control usable or editable data. For this purpose, the Content-based authorizations parameter must be activated in the Customizing application (Base function).
For a given user to be able to use the Cockpit: Planning conflicts application, the user needs to be assigned to an organization which is part of one of the following organization structures:
- Purchasing
- Inventory Management
Special features
Material requirements planning processes such as the acceptance of changes, generation of production orders etc. can only be carried out by an editor assigned to the material requirements planning.
Authorizations for business partners
The Cockpit: Planning conflicts application is not released for business partners.