Topic overview
The storage strategy is an important part of storage location control. It comprises of several individual strategies that together specify the procedure during put-away and withdrawal in warehouses categorized in storage locations. These strategies include the put-away and withdrawal strategies, picking strategies and replenishment strategy.
In this article, the storage strategies are described. The applications used and their fields, actions and procedures have been described in other articles.
Definition of terms
Storage strategies
Storage strategies are differentiated into put-away strategies and withdrawal strategies. The strategies use the properties of inventory and storage locations to determine suitable picking or put-away locations for the inventory of an item.
Replenishment strategies
The replenishment strategy determines whether filling existing storage units with part quantities has priority over put-away on empty storage locations. If inventory cannot be put away via replenishment, than put-away strategies will be tried, in order to to put the inventory away.
Put-away strategy
The put-away strategy is used to determine the criteria by which suitable put-away locations are identified for item inventory to be stored. For this, several properties stored in the system are considered, e.g., characteristics of the item inventory and the attributes of the put-away location. Possible put-away strategies are bulk additions to existing stock and empty location strategy.
Bulk additions to existing stock
With bulk additions to existing stock, goods are stored either until the storage location is completely full or the time limit has expired. Only from this time can inventories be picked from the storage location again. This means that the put-away dates of the inventories in the storage location are as similar as possible. Bulk inventory addition is often used together with bulk locations or fixed locations.
Put-away sort orders
A put-away sort order specifies the sequence in which aisles, rows, levels, and storage locations of a warehouse zone are considered when putting away inventory. The put-away sort order can achieve, for example, transverse or row-oriented put-away.
Replenishment restriction
A replenishment restriction is the characteristic used to limit the put-away of items to a storage location or a slot on which items are already stored. This characteristic can be, for example, the item (replenishment segregated by item), the batch or the lot (replenishment segregated by identifier), or the best-before of a batch/the generation date of a lot.
Withdrawal strategy
Withdrawal strategies analyze the current item inventory according to age and identify the oldest stocks first according to the FIFO principle (First In First Out). The age is kept up to date on a daily basis per item inventory and indicates initial entry into storage. For items managed by lots or by serial numbers, the identifier creation date is used as a basis for establishing the age; for items managed by batches, the expiration date is used.
Withdrawal sort order
A withdrawal sort order specifies the sequence in which aisles, rows, levels, and storage locations of a warehouse zone are considered for withdrawal. A withdrawal sort order has an effect only when the withdrawal strategy determines several inventories of the same age.
Picking strategies
The picking strategy controls the behavior for picking. The picking strategy may include picking via the issue of goods zone or direct bin picking via the storage locations of the Reserve utilization.
Storage location
A storage location is the exact point in a warehouse where items can be stored. A storage location within a warehouse always lies in a warehouse zone and is determined precisely on the basis of a row, a level, and a storage location number. Each storage location has a storage location category that establishes the use of the storage location. The availability of storage locations is essential for storage location control.
Slot
A storage slot is a subunit of a storage location. It is the smallest component of a warehouse. A storage slot can accept exactly one storage unit. The number of storage slots is the maximum number of storage units allowed for the storage location.
Scope
The following individual strategies belong to the storage strategy:
- Replenishment strategy
The replenishment strategy determines whether partially used quantities are to be refilled and whether picking locations are to be replenished to their maximum inventory level.
- Put-away strategy
The put-away strategy specifies the criteria according to which the put-away logic determines storage locations.
- Withdrawal strategy
The withdrawal strategy specifies the criteria according to which the withdrawal logic determines storage locations.
- Picking strategy
The picking strategy determines how the picking will take place if there is no fixed picking location in the warehouse zone.
- Fixed location put-away strategy
The fixed location put-away strategy defines how fixed locations are to be included in the put-away process.
- Fixed location withdrawal strategy
The fixed location withdrawal strategy defines how fixed locations are to be included in the withdrawal process.
Furthermore, a replenishment restriction can be specified in a storage strategy. It determines how to limit the put-away of items in a storage location or slot in which items are already stored.
The storage strategy also comprises the put-away sort order, the withdrawal sort order, and the preferred withdrawal of partially used quantities. Besides, the Bulk additions to existing stock put-away strategy requires a time limit to be defined for bulk inventory addition.
Usage
You can enter an inventory strategy in the following applications:
- Items
- Classifications (Inventory item classification 1)
- Warehouses
- Inventory order types
If you enter a storage strategy in one of the applications, then the storage strategy features will be displayed in the corresponding input fields. If you change one of the features, your entry in the Storage strategy field will be deleted. If a storage strategy does not exist with the given combination of characteristics, then a new storage strategy will be generated automatically. The newly generated storage strategy does not have an identification or a description and can neither be displayed nor edited in the Storage strategy application.
The storage strategy to be used is determined in the following sequence:
- Inventory item and warehouse
(Items application in the Inventory management view under the Warehouse data tab)
- Inventory item
(Items application in the Inventory management view)
- Inventory item classification 1
(Classifications application)
- Warehouse zone
(Warehouses application)
- Warehouse
(Warehouses application)
- Inventory order
(Inventory order types application)
If a valid storage strategy has been found at a level, the levels under it are ignored. If you save a storage strategy in the inventory item or in the inventory item classification 1, then this storage strategy is valid in all warehouses. If you do not save any storage strategy in the inventory item and the inventory item classification 1, then various storage strategies can be applied, depending on the warehouse or warehouse zone. By specifying a storage strategy in the inventory order type, you can define separate storage strategies for specific processes, which deviate from the settings in the master data, such as warehouse and item.
Put-away
The put-away process basically comprises three steps:
- Put-away in picking locations without replenishment order
- Replenishment of partially used quantities
- Put-away in empty storage locations or slots
Goods will only be put away to a picking location if the current inventory of the picking location is below the reorder level and there are no open replenishment orders for the picking location. Partially used quantities are replenished on the basis of the replenishment strategy used. The put-away strategy determines how item inventories are put away in empty storage locations and slots. The fixed location put-away strategy determines whether storage locations of the Fixed location without storage unit category are to be preferred to standard storage locations in the put-away process or whether goods may only be put away in these storage locations.
Subsequently, all strategies relevant to the put-away are described in detail.
Replenishment strategy
A partially used quantity can relate to a storage unit or a storage location without storage unit. In storage locations with storage unit, the current inventory in the storage unit must be less than the highest inventory level saved for the item in the packaging definition. In storage locations without storage unit, the current inventory must be less than the highest inventory level in the storage location type. An empty storage unit or a storage location without inventory is not considered to be canceled and is therefore not replenished either.
During replenishment, it is attempted to get back to the highest inventory level in the storage location. Picking locations are replenished up to the maximum inventory level – not to the inventory capacity according to replenishment definition.
In storage locations of the storage location category Bulk storage location with storage unit, replenishment is considered to be storage of storage units until the storage location reaches its maximum acceptance capacity. Therefore, a replenishment strategy should be used for storage locations of this category.
In order to replenish an inventory in a storage location, the storage location or the slot must be item-segregated. Furthermore, the storage location must not have any storage location reservations. A storage location reservation is if a future issue or receipt is planned in the storage location. If the storage location is sub-divided into slots, then there cannot be any issues reservation for the complete storage location and the storage location must have inventory slots that do not have any receipts reservations yet. If the Batch/Lot replenishment restriction is applied with the used storage strategy or storage location type of the storage location to be replenished, then the inventory must also be item-segregated after the replenishment. The identifier segregation is not included in the storage locations of Picking location without storage unit category. Replenishment is not always identifier-segregated in the picking locations.
Possible replenishment strategies are:
- All locations
Storage locations of the storage location category Picking location without storage unit are also considered in the replenishment strategy All locations. The storage locations are included in the sequence defined by the put-away restriction or warehouse zone priority and put-away sort order. The picking locations are not replenished with any preference. While replenishing fixed picking locations, the replenishment definition saved in the replenishment lot size is not included. While replenishing, it is attempted to reach the highest inventory level (and not the inventory capacity) at the picking location.
- All locations except picking locations
Storage locations of the storage location category Picking location without storage unit are not considered in the replenishment strategy All locations except picking locations.
- Do not replenish
Storage locations are not replenished in the replenishment strategy Do not replenish.
The following example shows how an inventory of 30 pcs. of batch 1 of the item A1 is put-away through the replenishment strategy All locations.
There are following inventories in the L1 warehouse:
Storage location | Item/identifier | Quantity | Comment |
L1-R1-001-01-001 | A1 / Batch 1 | 10 pc. | Full storage unit |
L1-R1-001-01-002 | A1 / Batch 1 | 4 pc. | Partially used quantity |
A2 | 2 pc. | Partially used quantity | |
L1-R2-001-01-001 | A1 / Batch 1 | 4 pc. | Partially used quantity |
L1-R2-001-01-002 | A1 / Batch 2 | 8 pc. | Partially used quantity |
L1-R2-001-10-001 | A1 / Batch 3 | 16 pc. | Picking location |
According to the put-away restriction, the storage locations are included in alphanumeric sequence (as shown above). In picking location L1-R2-001-10-001, a replenishment definition for Item A1 is saved. The reorder level is 10 pcs. and the highest inventory level is 30 pcs.
A complete storage unit is stored in the storage location L1-R1-001-01-001. Storage location is not taken into consideration. The storage location L1-R1-001-01-002 is not item-segregated, and therefore not included either.
In the Warehouse zone R2, the storage location L1-R2-001-01-001 is replenished with 6 pcs. Since no new inventory record is generated, the put-away inventory receives the same put-away date and therefore the same FIFO date as the existing inventory. Then, at the storage location L1-R2-001-01-002, 2 pcs. are replenished. Since the batch 1 was not available at the storage location, a new inventory record is generated with the current date as put-away date.
Finally, the picking location is considered. In order to get the highest inventory level of 30 pcs., 14 pcs. are put-away there.
The remaining 8 pcs. cannot be put-away through the replenishment. This remaining quantity is put-away using the put-away strategy.
Put-away strategy
The put-away strategy specifies the criteria according to which the put-away logic determines the storage locations if the put-away quantity could not be completely put-away through the replenishment of partially used quantities. Storage locations of the storage location category Picking location without storage unit are not included.
Possible put-away strategies are:
- Empty location
- Bulk additions to existing stock
Empty location
In the put-away strategy Empty location only empty storage locations are included. If the storage location is sub-divided into slots, then at least one of the slots must be empty. If a storage unit is used in the put-away process, then all slots must use the same storage unit. The put-away can also take place in warehouse zones without storage locations (simple warehouse zones).
In order to put-away an inventory in a storage location of the Storage location with storage unit category or Storage location without storage unit category, the storage location must not show any storage location reservations. A storage location reservation is if a future issue or receipt is planned in the storage location. If the storage location is sub-divided into slots, then there cannot be any issues reservation for the complete storage location and the storage location must have inventory slots that do not have any receipts reservations yet. In the storage location category Bulk location with storage unit and Fixed location without storage unit, a put-away with existing storage location reservations is also possible. In such a case, the sum of the current inventory quantity, the quantity of future receipts and put-away inventory quantities must not exceed the capacity of the storage location. This means the in a fixed location without storage unit, for instance, several open storage orders can exist for put-away simultaneously.
If Item or Batch/Lot is defined as replenishment restriction in the storage strategy used or for the storage location type of the storage location, the inventory must also be item/identifier-segregated after the put-away.
Bulk additions to existing stock
The put-away takes place under the inclusion of bulk additions to existing stock term with the put-away strategy Bulk additions to existing stock.
The bulk additions to existing stock term is reset with the first put-away for an empty storage location. It gives the time period in which additional storage can be carried out at the storage location and that the storage location is not included in the withdrawal.
The time period in which no withdrawal is permitted, is dynamically calculated at the time of the withdrawal from the attribute putAwayTime
in the business object com.cisag.app.inventory.obj.UnitOnhandhand
. In contrast to the put-away date used for the calculation of the FIFO date, the bulk additions to existing stock term also has an entry.
Only if one of the following conditions is met, the item inventories in the storage location will be included again when inventory is withdrawn:
- The storage location is full.
- Bulk additions to existing stock has run out.
- A withdrawal has already taken place at the storage location after the last setting of the bulk additions to existing stock term, for instance with the help of a manual inventory posting. Manual put-aways do not have any influence on the bulk additions to existing stock term.
From the first entry of one of the conditions, the storage location is not available for the put-away. Another put-away is possible only if the storage location is empty again. With the first put-away at an empty storage location, the bulk additions to existing stock term is reset. A withdrawal will be possible only if one of the abovementioned conditions is met.
With the put-away strategy Bulk additions to existing stock only storage locations of the storage location categories Bulk location with storage unit, Fixed location without storage unit, and Storage location without storage unit are included.
If you are using the put-away strategy Bulk additions to existing stock, the inventory must be item and identifier segregated after put-away in the storage location.
Fixed location put-away strategy
The fixed location put-away strategy defines how fixed locations are used in the put-away process.
The following fixed location put-away strategies are possible:
- Not preferred
The Not preferred fixed location put-away strategy takes item definitions of fixed locations as an item restriction only. Fixed locations can solely be used for the respectively assigned items. - Preferred
The Preferred fixed location put-away strategy chooses fixed locations over standard storage locations in the put-away process. If the inventory has not been fully put away in fixed locations, the system tries to put the item away in other storage locations. - Exclusive
The Exclusive fixed location put-away strategy will only put away the item in a fixed location if an item definition exists for the item to be put away in a fixed location. If this is not possible, e.g., due to maximum inventory, the put-away process will be canceled. If, however, no fixed locations exist in the respective warehouse zone, items will be put away in reserve locations.
Put-away sort order
With put-away sort orders, you can define the sequence in which the put-away logic is included in the storage locations. If required, enter for one or more of the following structure levels of the warehouse organization a numeric value between one and four:
- Aisle
- Row
- Level
- Location
A structure level with a low value has precedence in put-away before a structure level with a higher value. If you do not enter a value, the structure level is also not sorted. If there is no value for a structure level used in the inventory organization, the sequence of this structure level and all subsequent structure levels is not defined.
Since warehouses and warehouse zones can be of different inventory organizations, all structure levels are displayed. Values for a structure level that find no use by the inventory organization, are ignored in the sort order.
The inventory organization is determined in the Warehouses application per warehouse and warehouse zone. The following table shows the structure levels used in the respective inventory organizations:
- Simple warehouse
In the warehouse this entry means that it does not have any other sub-division resulting in storage location control being impossible here.In a warehouse zone it means that it is not sub-divided into locations. The warehouse in which there is such a warehouse zone must however have an inventory organization that permits another sub-division.If in the Customizing application the storage location control is not activated, the you can enter simple warehouses. - High rack storage area
In a warehouse this entry means that it is further sub-divided into warehouse zones and is offered while entering the warehouses in this warehouse the inventory organization High rack storage area as default for the inventory organization of the warehouse zone.In a warehouse zone it means that it is sub-divided into rows, levels and locations. - Bulk storage
In a warehouse this entry means that it is further sub-divided into warehouse zones and is offered while entering the warehouses in this warehouse the inventory organization Bulk storage as default for the inventory organization of the warehouse zone.In a warehouse zone it means that it is sub-divided into rows and locations. - Locations only
In a warehouse this entry means that it is further sub-divided into warehouse zones and is offered while entering the warehouses in this warehouse the inventory organization Locations only as default for the inventory organization of the warehouse zone.In a warehouse zone it means that it is sub-divided into locations only.
If in Customizing the utilization of aisles is activated and the inventory organization has rows, then the rows can be compiled into aisles. An aisle comprises of rows that can be operated by the same physical area. In the put-away sort order, the rows and aisles both can be sorted. The aisles should appear before the rows. Enter a sequence for the aisles that is larger than the one for the rows to ignore the value during the put-away.
Some put-away sort orders of a high rack storage area have been shown as example below. The level of the rows is numbered according to their sort sequence. The arrows show the sort sequence of the individual locations.
Aisle – Level – Row – Location
The inventories are first put away at the lowest level of an aisle in this put-away sort order. Per level, the storage locations are sorted according to the row and location.
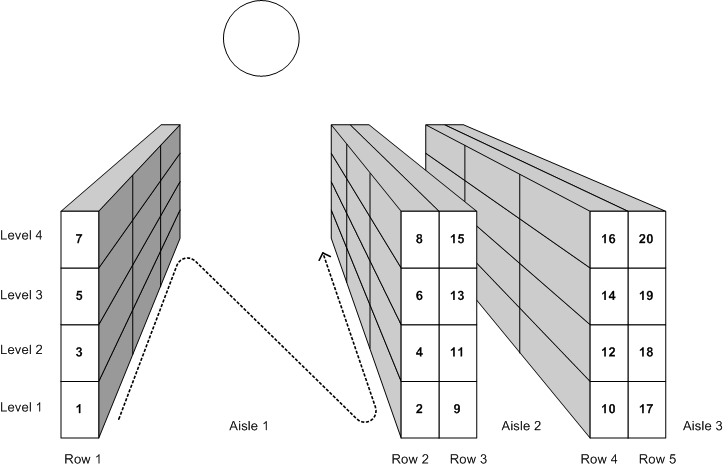
Aisle – Level – Location – Row
The inventories are first put-away at the lowest level of an aisle in this put-away sort order. Per level, the storage locations are sorted according to the location and row.
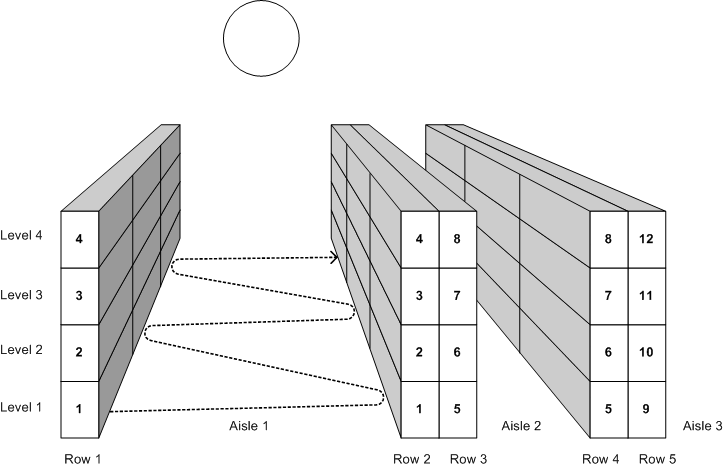
Aisle – Location – Level – Row
The inventories are first put-away at the locations with the lowest numbers in this put-away sort order. Per location, the storage locations are sorted according to the level and row.
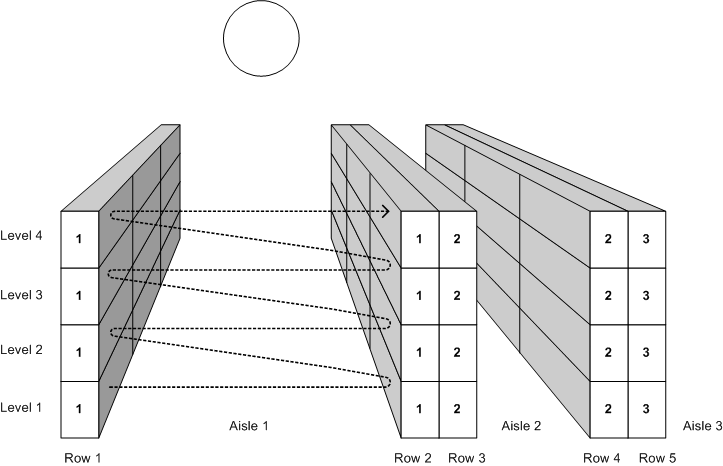
Location – Level – Aisle – Row
In this sort order, the inventories are transverse oriented according to location and level.
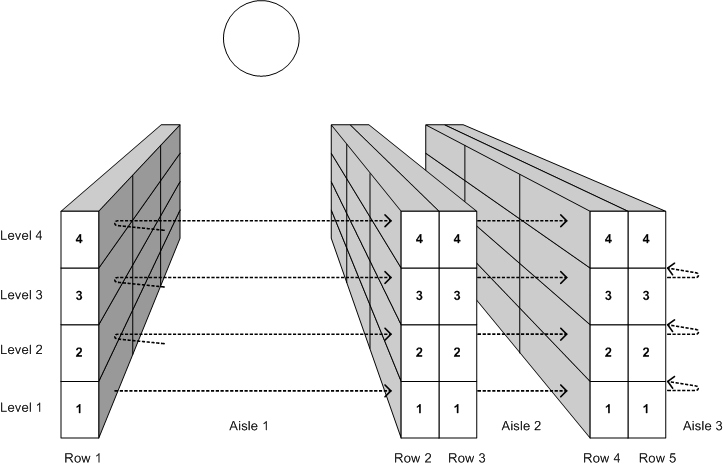
Replenishment restrictions
The replenishment restriction determines how to limit the automatic put-away of items in a storage location or a slot on which items have already been stored.
In the course of the automatic put-away, two or three replenishment restrictions in total are included and applied in succession when determining a storage location:
- Storage location replenishment restriction of the storage location type
- Slot replenishment restriction of the storage location type if the storage location is divided into slots
- Replenishment restriction of the storage strategy
If at least one of these replenishment restrictions prohibits using a storage location, the goods will not be put away in this storage location.
The following replenishment restrictions are possible:
- Process
You can put away the inventories of another item in the storage location or slot if an open issue or receipt exists for the storage location, which originates from the same process in which the inventories are put away.
NoteIf free inventory has already been put away in the storage location or slot, the storage location with this replenishment restriction cannot be restocked since the inventory is not part of a put-away process. - Classification
You can put away the inventories of other items in the storage location or slot if they belong to the same inventory item classification 1 as the item already put away. - Item (replenishment segregated by item)
You can only put away the inventories of exactly one item in the storage location or slot. Different identifiers are permitted.
This replenishment restriction also applies to items managed by identifiers of the Serial number with inventory management or Serial number without inventory management category. - Batch expiration date/lot generation date
You can put away batches with the same expiration date or lots generated on the same day in the storage location or slot. - Batch/lot (replenishment segregated by identifier)
You can only put away exactly one batch or exactly one lot of an item in the storage location or slot. - None
The storage location or slot can be replenished without restrictions.
Withdrawal
All strategies relevant for the withdrawal are described in detail.
Withdrawal strategy
In all storage strategies, the withdrawal item inventories are determined according to their FIFO date. FIFO corresponds to the assumption that inventory that was put away first will also be withdrawn first (first in, first out). The FIFO date has been explained in detail in the Identifier assignment article.
How FIFO date is to be included in withdrawal can be determined with the withdrawal strategy.
Possible withdrawal strategies are:
- FIFO
- Strict FIFO
For more information, refer to Introduction: Storage location control. It provides a detailed description of how selection of withdrawal strategy affects the withdrawal logic.
Withdrawal sort order
With withdrawal sort orders, you can define the sequence in which the withdrawal logic is included in the storage locations. The withdrawal sort order comes in question only if many inventories are determined having the same FIFO date. In such a case, the withdrawal sort order decides the sequence in which the determined inventories are withdrawn.
The withdrawal sort order is defined just like the put-away sort-order; see the Put-away sort order chapter.
Picking strategy
The picking strategy determines how the picking will take place if there is no fixed picking location in the warehouse zone.
Possible picking strategies are:
- Any storage location (bin picking)
In case of the Any storage location picking strategy, the quantity to be picked is taken from the item inventory in the source storage location. Relocations across warehouses take place through the issue of goods zone of the source warehouse and through the receipt of goods zone of the destination warehouse. - Picking point
The item inventory is first transported to the issue of goods zone (picking point) in the “Picking point” strategy. Any remaining inventory will be returned to the source storage location. An internal relocation within a warehouse is realized through the receipt of goods zone. If the destination warehouse zone is not divided into storage locations, the inventory will be relocated directly from the source storage location to the destination warehouse zone. - Picking point without return transfer
In case of the Picking point without return transfer strategy, the item inventory is first transported to the issue of goods zone (picking point). Any remaining inventory remains in the issue of goods zone. Use this strategy, for example, if you always pick only small quantities and many successive picking orders require the same item. Thus, you do not have to put items back with a return transfer order again and again.
The Picking with storage location-controlled warehouses article gives a detailed description of picking in sub-divided warehouses. The Introduction: Transport processes article describes inventory orders that are generated when using various picking strategies.
Fixed location withdrawal strategy
The fixed location withdrawal strategy defines how fixed locations are used in the withdrawal process.
Possible fixed location withdrawal strategies are:
- Not preferred
The Not preferred fixed location withdrawal strategy does not allow for withdrawing from fixed locations first. - Preferred
The Preferred fixed location withdrawal strategy chooses fixed locations over standard storage locations in the withdrawal process. If the required inventory could not be fully withdrawn from fixed locations, the system tries to withdraw any remaining quantity of the required item inventory from other storage locations.
First withdraw partially used quantities
If the withdrawal strategy FIFO is being used and the preferred withdrawal of partially used quantities is activated, then first the partially used quantities are determined in reserve locations or slots by the withdrawal logic. A partially used quantity is when the item inventory is smaller than the capacity according to the packaging definition. A partially used quantity is also present if the item inventory matches the packaging definition, but the reserve location or slot is not segregated by items.
A partially used quantity can refer to both a storage unit in a slot and a storage location without storage unit. An empty storage unit or a storage location without inventory is not considered as partially used.
In order to withdraw a partially used quantity, the storage location must not have any storage location reservations. A storage location reservation is if a future issue or receipt is registered.
Preferred withdrawal of partially used quantities is not possible at storage locations of the Bulk location with storage unit storage location category, since only full storage unit can be put-away or withdrawn in such storage locations. With the withdrawal strategy Strict FIFO partially used quantities cannot be withdrawn as preference either.
For more information, refer to Introduction: Storage location control. It provides a detailed description of how preferred withdrawal of partially used quantities affects the withdrawal logic.