Topic overview
Inventory management is a sub-area of logistics. It is used for storage of items, picking, and transport of items from the receipt of goods across all phases of production or storage up to the issue of goods. The items are always stored at one warehouse. A warehouse is always assigned to exactly one site, which in turn represents a node in the Inventory management organizational structure. In a multi-site environment, several sites can be considered for this. In a single site environment, this is always the active OLTP client. Items can be stored in various ways. If Storage location control is activated, items can be stored up to the storage location level. Without Storage location control activated, items can only be stored at unstructured warehouses. For additional information refer to the Introduction: Storage location control article.
Inventory management represents the connection between purchasing and/or production and sales. When a receipt of goods is posted, a defined quantity of an item is added to the inventory of a warehouse. A receipt is posted. The physical additional to the inventory is referred to as put-away” When an item is delivered, for example, to a customer, another inventory posting is made in order to reduce the inventory of the warehouse by the amount of the delivered quantity. An issue is posted. The physical removal from the inventory is called withdrawal.
This document explains the most important processes and functions of the inventory management. Refer to the respective introduction documents to learn more about individual inventory management topics. The applications used for it and the related fields, actions, and procedures are described in separate documents.
Definitions of terms
Inventory valuation
Inventory valuation is an ongoing calculation of the corresponding value for item inventory available in the warehouse. The value is expressed in monetary units in the corresponding internal currencies. All inventory postings that cause changes to the quantity or value of inventoried items are documented in various valuation processes. In the course of generating the inventory postings, the inventory and its valuation is updated on the basis of the floating average price method. The full sequence of dated inventory valuations, such as the dated average price, can only be identified after the posting period has been closed.
Warehouse inventory management
Warehouse inventory management is an ongoing recording of the current warehouse inventory. The inventory management server updates these values after every inventory posting with a quantity transaction. Warehouse inventory management is done at the lowest structural level of the warehouse and item or identifier. If the item has several parallel inventory units, then quantities are maintained for each unit. Inventory quantities can have different properties, such as subdivision into different quality statuses.
own inventory
Own inventory is the inventory whose inventory owner is the own firm. The own firm is assigned to this inventory as inventory owner in the ERP system. The inventory of other inventory owners is called external inventory.
external inventory
External inventory is every inventory which has an inventory owner other than the own firm assigned. External inventory can be inventory from affiliated companies or from external suppliers.
Consignment
In consignment, the goods of a supplier (consigner) are made available in a consignment warehouse directly on their customer’s (the consignee’s) premises. The business transaction and the transfer of ownership only take place upon the issue of the goods from the consignment warehouse, i.e. the customer’s use or resale of the goods. Such issue is referred to as consignment withdrawal. At agreed intervals, the customer informs the supplier about the consignment withdrawals in respective consignment withdrawal declarations. On the basis of these withdrawal declarations, invoices will be issued. From the purchasing perspective, this type of business is referred to as supplier consignment; from the sales perspective, it is referred to as customer consignment.
Inventory management
The term Inventory management defines the task of storing and picking items in many different ways. This term also includes the transport of the items from receipt of goods through all the production or storage stages right up to the issue of goods.
Inventory management server
The inventory management server is responsible for ongoing recording of the current warehouse inventory quantities and for maintaining the moving average prices in the warehouses assigned to it. In warehouses subdivided into storage locations, the inventory management server has additional tasks, such as reserving storage locations and inventory, and reconciling inventory count differences. When an inventory management server is launched, a batch job is generated. If a warehouse is subdivided into storage locations, then the data relevant for storage location control is loaded into a cache, to minimize access time.
Warehouses
A warehouse is a logically or physically defined area in which item inventory is maintained. A warehouse is always assigned to a site. A warehouse can be subdivided into storage locations if storage location control is enabled in Customizing. The exact structure of the warehouse is defined by the warehouse organization.
Inventory posting
Inventory posting is carried out in order to document all quantity and value transactions within Inventory management. In the process of inventory posting, inventory is updated and materials evaluated.
Reservation
A reservation is a guarantee that a certain good will be deliverable at a specific date. Reservations represent the link of a demand origin (element) to a demand coverage (element). A reservation is only possible if both items and warehouses match between demand origin (element) and demand coverage (element).
Availability
The availability is the predicted supply of an item on a current or a future date. Availability is calculated by means of an availability rule and consists of
• the current inventory,
• planned receipts,
• the planned issues.
Possible back orders can also be taken into account with the calculation of availability. If the reservation function is used, availability consists of
• the unreserved current inventory,
• the unreserved planned receipts, and
• the unreserved planned issues.
Partial quantities are also taken into consideration in the process.
Processes
The following ERP processes relevant to inventory management are briefly described in the following sections:
Receipt of goods
Goods can be delivered from the company’s own production, from a distribution, or as the result of an order. Alternatively, a customer may also return the goods back. Therefore, the receipts can have completely different sources: Accordingly, receipts can be created based on the purchasing or production process and also as a result of returns originating from the sales process. In multi-site systems, receipts can also be created from the distribution of goods among sites. All types of receipts of goods are created with the Receipts of goods application. When a receipt of goods is posted, the created quantity of a warehouse-managed item is added to the inventory.
The starting point is always a production order, purchase order, distribution order, or sales order, to which the delivered items must also be assigned during the course of creating the receipt of goods. The Receipts of goods application contains a separate view for each category (purchasing, production, goods return, and distribution), each containing the fields required for creating receipts of goods.
The Receipts of goods application is also used to create any services provided for the company itself that were ordered by means of purchase orders.
For more information about receipt of goods, refer to the Introduction: Receipts of goods article.
Picking
The picking order is a summary of items that are to be provided for another process in the correct quantity and with the correct identifier. It serves as the working basis for the warehouse personnel. At the same time, reporting is used to enable downstream processes. The traceability of identifiers is also based on the reporting.
Possible processes for which picking orders are generated are:
- Production orders
- Delivery orders from external manufacturing orders for material provided to vendor
- Delivery orders from the sales order
- Delivery orders from distribution orders
If reservations are used, item quantities can only be picked in the amount in which inventory reservations exist.
For more information on picking, refer to articles Picking order generation and Picking with storage location-managed warehouses. For information on identifier assignment, refer to the Identifier assignment article.
Delivery
Delivery orders are used to summarize the items that are to be delivered to a particular recipient or picked up. Recipients can be the delivery recipients of customers, a site of the company itself, or, in case of returns of goods, suppliers. Delivery orders are used for external deliveries, too, e.g. in an external third-party order with the supplier delivering items to the customer.
The delivery order describes the range of services, the delivery terms, and the shipping terms for the delivery of the items. It is used in particular to document which items will be delivered in what quantity and using what transport means. Besides, delivery orders are the basis for the delivery slips and pickup slips that are generated as voucher documents from delivery orders.
A delivery order can be used, along with its line items, as a basis for calculating the freight cost. It also serves as a criterion for the packaging of its line items into loading units and as line items for specific loads if these functions are activated in the Customizing application.
For more information on deliveries, see the Delivery order generation article.
Distribution
In a multi-site environment, items can also be delivered from one warehouse to another. The distribution of warehouse inventories is made through distribution orders. Distribution orders are a component of the Sales framework.
For additional information on distribution orders, refer to the Introduction: Distribution orders article.
Shipping
Shipping is used to convey the items to be delivered to their recipient by the agreed upon date. Several applications are available for this purpose, some of which are explained later on in this chapter.
Loading units
A loading unit is a summary of items in or for a suitable storage unit in order to store or ship it. A loading unit can also contain other loading units. Depending on the setting in the Customizing application, the loading unit identification can be selected by the user or formed from the NSU (number of shipping unit) according to the EAN128 standard.
Storage location control is required for consistent use of loading units. Only then can the system auto-join a loading unit created during receipt of goods with a delivery order. If Storage location control is not activated, loading units can be created with receipt of goods, but it is still necessary either to generate new loading units in the delivery order or to manually join the existing loading units with the delivery order in the Loading units application. The same applies if a loading unit has been put away in an unstructured warehouse or in a warehouse zone without storage locations.
Loading units can be generated in the Receipts of goods and Delivery orders applications. For a description of the use of loading units, refer to articles Introduction: Shipping and Loading units and storage location control.
Loads
A load is the summary of deliveries that are delivered to their point of destination in one process. This can be, for example, a truckload, as well as a collection of delivery orders that are to be shipped with a parcel service.
The Loads application is used to create the loads. For a description of the use of loads, refer to the Introduction: Shipping article.
Routes
A route establishes a certain order in which the delivery recipients are supplied. Routes can be used once and are summarized individually for pending deliveries. A route can also be re-used if, for example, deliveries have to be made regularly to the same recipients at certain intervals. The routes used regularly are also used for planning and selecting deliveries to be made from a site.
The Routes application is used to create routes. For a description of the use of routes, refer to the Introduction: Shipping article.
Inventory postings
All processes that lead to changes of quantity or value of inventoried items are documented in the form of inventory postings. Inventory postings are generated automatically as a result of upstream processes, but can also be created manually in the Inventory postings application. The following applications in the Inventory management framework are used to create and query the inventory postings:
- Inventory postings
In the Inventory postings application, you can create inventory postings manually. In the Posting error log view, you can correct incorrect inventory postings.
- Inventory posting query
In the Inventory posting query application, you can query manually-created inventory postings as well as automatically-generated inventory postings.
- Cockpit: Inventory posting errors
In the Inventory posting errors cockpit, you can query the incorrect inventory postings in the posting error log. In addition, you can change to the Inventory postings application in order to correct the incorrect inventory postings there.
- Posting key
The posting key describes the posting process. The posting key contains information about the type of action to be carried out, such as receipt, transfer, issue, revaluation, or correction. Furthermore, the posting key identifies whether the posting is a main process or a secondary process.
You can use the Posting keys application to create posting keys.
For a description of the applications and the related fields, actions, and procedures, refer to the respective article.
Inventory postings are processed asynchronously by the inventory management server responsible for the warehouse. During the course of the processing, the inventory management server updates the inventories and the inventory values according to the posting key used. If an inventory management server is not operating, inventory postings for the assigned warehouses are only processed once the inventory management server starts. For more detailed information on the inventory management server, refer to the Inventory management server article.
Each inventory posting contains the following numbers:
- Posting number
The posting number is generated based on the number range stored for the posting key used.
- Identification
The identification is a unique number in the database. It is assigned by the system when the inventory posting is generated.
- Processing number
The processing number is assigned by the inventory management server during processing and is unique following assignment. If the processing number is zero (0), this means that the inventory posting has not yet been processed by the inventory management server and, thus, has not been taken into account in the inventory or the inventory value.
In the case of a transfer posting or a revaluation, two inventory postings are produced: one inventory posting for the issue and one inventory posting for the receipt. Both receive the same posting number. However, the identification is always unique. If the posted quantity is positive, the issue posting receives the lower posting number. If the posted quantity is negative, the receipt posting receives the lower posting number. This ensures that the withdrawal occurs before the put-away, and in the case of a transfer posting that the FIFO date can be transferred successfully to the destination inventory.
Warehouse inventory management
Warehouse inventory management is an update of the current warehouse inventories. The inventory management server performs this update after every inventory posting with a quantity transaction. The warehouse inventory management is performed at the smallest structure level of a warehouse and item or identifier. If Storage Location Control is activated, the warehouse inventories are managed up to the level of the storage location or storage slot.
Inventory quantities
The current quantity of an inventory item in the warehouse is referred to as warehouse inventory. Warehouse inventory can be managed in up to three mutually-independent, parallel inventory units. Inventory quantities can also have different properties, such as subdivision into different quality assurance statuses.
For a simple warehouse, the warehouse inventories at the warehouse level are saved in the Inventory business entity. For subdivided warehouses, the warehouse inventories are stored both at the warehouse level as well as at the storage location level in the Storage location/slot inventory business entity and its dependent Inventory (items in storage unit).
You can see the current inventory of an item in the Cockpit: Inventories/items and Cockpit: Inventories/identifiers cockpit applications. If the warehouse is subdivided into storage locations, you can also query the inventories at storage location level in the Cockpit: Storage location inventories/items and Cockpit: Storage location inventories/identifiers cockpit applications.
Reservations
In order to ensure that a desired quantity of items is available at a specified time point, item quantities can be reserved. The available quantity is reduced by the amount of the reservation. These items are therefore no longer available for other purposes.
Reservations affect all processes that change the inventory and the availability of items. You can use the Reservations application to query and process reservations.
For more information on reservations, see the Introduction: Reservations article.
Availability
The available inventory designates the forecast inventory of an item on a future date. Availability is calculated using an availability rule and consists of the current inventory plus planned receipts and issues as well an any back orders.
If you have activated the Reservations function under Customizing, the available inventory is accepted as the forecast, unreserved inventory of an item at a future date.
Various processes in the ERP system factor in the availability of an item. For example, an availability check can be performed when creating a sales order or when dispatching a production order.
You can query the availability of an inventory item at a certain By date in the Availability query application as well as directly in the sales order line item.
For more information on availability and the availability query, see the Introduction: Availability article.
Identifiers
Items can be managed using identifiers. Identifiers are used to unambiguously identify an item or a particular quantity of an item. Thus, for example, a television is identified not only by the item number but also by the “serial number” identifier and is therefore unique. The following identifiers are supported: batch, lot, serial number with inventory management, and serial number without inventory management.
The properties of an identifier include the quality assurance status (QA status). It specifies whether the identifier is released, blocked, or in quarantine. Inventories of the identifier can be analyzed and utilized specifically according to the possible QA status. In addition, a QA status can be assigned to a warehouse or a warehouse zone. If the QA status at the warehouse level and the QA status at the identifier level coincide, the less favorable QA status applies in each case.
The expiration date of a batch is the date up to which the usability of a batch is guaranteed. If the expiration date is before the current date, the identifier will be deemed “expired” and no longer available for automatic batch assignment for pickings.
The retaining date is the time point up to which the batch is not available for withdrawal. This means that, for example, during this time the inventory of the identifier is not considered for the automatic identifier assignment.
In the availability calculation, the inventory of a batch is only regarded as available between the retaining date and the expiration date (or start of minimum batch lifetime).
For more information on identifiers, see the Introduction: Identifiers article.
Identifier assignment
If an item to be picked or delivered is managed using identifiers, an identifier assignment must be made before the item can be picked. As a result of the assignment, the item with this exact identifier will be available. When the Reservations function is used, the identifier assignment typically also generates reservations; otherwise, identifier reservations are generated.
For more information on identifier assignment, see the Identifier assignment article.
Identifier reservations
An identifier reservation is used to reserve a defined identifier (batch, lot, or serial number with inventory management). An identifier reservation is always used if the Reservations function is deactivated or when this function is active but other settings prevent a reservation in individual cases.
As a result of the identifier reservation, the quantity of planned issues of identifier-managed items of the corresponding warehouse is no longer available. The effect of the identifier reservation is that items with a certain identifier can only be picked or withdrawn up to the available warehouse inventory of the corresponding warehouse. The identifier of an item is only reserved if an issue from the warehouse is affected. Put-aways and warehouse-internal relocations of items that are managed using identifiers are not considered for identifier reservations.
In contrast to reservations, identifier reservations contain no information whatsoever about the origin of the reservation. This is one of the main differences. An exception to this is items that are managed using serial numbers. If an item with serial number is reserved via an identifier reservation, the origin of the reservation is noted with the serial number. All other information and functionalities of the Reservations function, such as reservations at the item level or reservation data in the availability query, are not available.
For more information on identifier reservations, see the Identifier Reservations article.
Identifier where-used list
In some industries, information about the identifiers of materials used in production is necessary (batch tracing). In case of recalls, it can be necessary to know which customers a certain identifier was sold to. The identifier where-used list gives information about both the origin of identifiers (such as receipt of goods or production) and their use (for instance, use in production, issue to customers, etc.).
In the Identifier where-used list application, you can trace the use and origin of a particular identifier down to any level of the bill of material.
For a description of the identifier where-used list, see the Identifier where-used list article.
Inventory owners
The inventory of an item in a warehouse, warehouse zone, or storage location is always assigned to an inventory owner.
Own inventory and external inventory
A warehouse can be used to store own inventory, external inventory, or both. External inventory can be inventory from an affiliated company or from an external supplier.
If the external inventory of an affiliated company is taken from a warehouse, this will result in an inventory posting and inter-company billing. If external inventory from external suppliers is taken from a warehouse within the scope of the supplier consignment, the external supplier will be informed about these withdrawals. This is done by means of consignment withdrawal declarations. The supplier issues the invoice based on the consignment withdrawal declaration.
The withdrawal implies the transfer of ownership of goods from the supplier to the customer. For this purpose, a revaluation takes place directly before the issue of goods, in which the inventory owner of the goods is changed.
For a full description of the supplier consignment, please see the Introduction: Supplier consignment article.
Multiple inventory owners
In structured warehouses, one can store inventories with different inventory owners. At warehouse zone level, inventories from different inventory owners can be stored in simple warehouse zones. Whereas only inventories having the same inventory owner can be stored at a storage location.
Planned receipts and issues are always assigned to one inventory owner, as well. Business processes, however, resulting in withdrawals in the supplier consignment can be configured in such a way that planned issues originated in these processes have no detailed inventory owner information. In this case, those planned issues refer to a group of external or internal inventory owners which are displayed in a defined order.
Such a sequence of inventory owners can be defined for each warehouse and item in Customizing. If corresponding definitions are given, the availability of an item in a warehouse can also be calculated for multiple inventory owners based on:
- the inventories of all listed owners,
- planned receipts and issues assigned to all listed owners, and
- planned issues without inventory owner information.
A planned issue without inventory owner information can be reserved for multiple inventory owners by using the Reservations function. Similar to the Identifier assignment, a specific inventory owner needs to be assigned automatically or manually before the consignment or delivery. With the assignment, the reservation becomes more specific as well.
Inventory valuation
All inventory postings that cause changes to the quantity or value of inventoried items are documented in various valuation methods. In the course of processing the inventory postings with the aid of the inventory management server, the inventories and their valuation are updated according to the floating average price method. The inventory valuations that are divided into periods, such as FIFO (first in/first out) or LIFO (last in/first out), can only be determined consistently after closing of the posting period.
The valuations that are divided into periods are based on the inventory postings with a posting date within the posting period to be calculated. Consequently, a back-dated inventory posting changes the average price divided into periods but also influences the current floating average price. A roll-up of back-dated inventory postings does not take place during the valuation.
In the Customizing application, you specify whether the inventory valuation occurs at the item level or at the item/warehouse level. For the Item valuation level, issues are generally valued at the floating average price at the item level; for the item/warehouse valuation level, issues are generally valued at the floating average price at the item/warehouse level. The setting is also relevant for the query of inventory values and the generation of inventory count valuations. Because the floating average price is always managed at both levels, it is technically possible to change between valuation levels subsequently. After the changeover, the average prices at the new valuation level must be carefully checked and, if necessary, corrected, e.g., with the aid of an inventory count valuation.
The inventory values that are divided into periods, including the average price that is divided into periods, can be calculated in the Calculate inventory values application and then displayed in the Inventory value query application. The floating average price is reliably displayed for the current period only if no back-dated or pre-dated inventory postings were made. The floating average price can be seen, for example, in the Inventory postings application with the aid of an issues posting key with the average price valuation price.
For more information on the possible valuation methods, see the Inventory valuation article.
Inventory count and inventory count evaluation
An inventory count is a record of the quantity and value of the existing inventory of a company’s assets and liabilities. The inventory count is made at a set time by carrying out a physical inventory check. In this process, the existing inventories are counted, measured, weighed, or estimated and can be compared to the book inventories. The implementation can be carried out by different inventory count methods such as annual inventory count, perpetual inventory count, or sampling inventory count.
You can make an inventory count of the warehouse inventories with the aid of the Generate inventory count and Inventory count applications. You can revaluate the warehouse inventories without the need for quantity changes as in the inventory count with the aid of the Generate inventory count valuation and Inventory count valuation applications.
For a description of the inventory count and the inventory count valuation, see the Introduction: Inventory count article.
Inventory management server
All processes that lead to changes of quantity or value of inventoried items are documented in the form of inventory postings. Inventory postings are generated automatically as a result of upstream processes, but can also be created manually in the Inventory postings application.
In the course of creating the inventory postings, the update of the inventories and the inventory valuation are carried out in accordance with the posting key used. One inventory management server is responsible for the update of the inventory quantities and the inventory values at a particular warehouse.
The following figure shows the processing of the inventory postings. The processing is subdivided into synchronous creation or generation and asynchronous processing by the inventory management server.
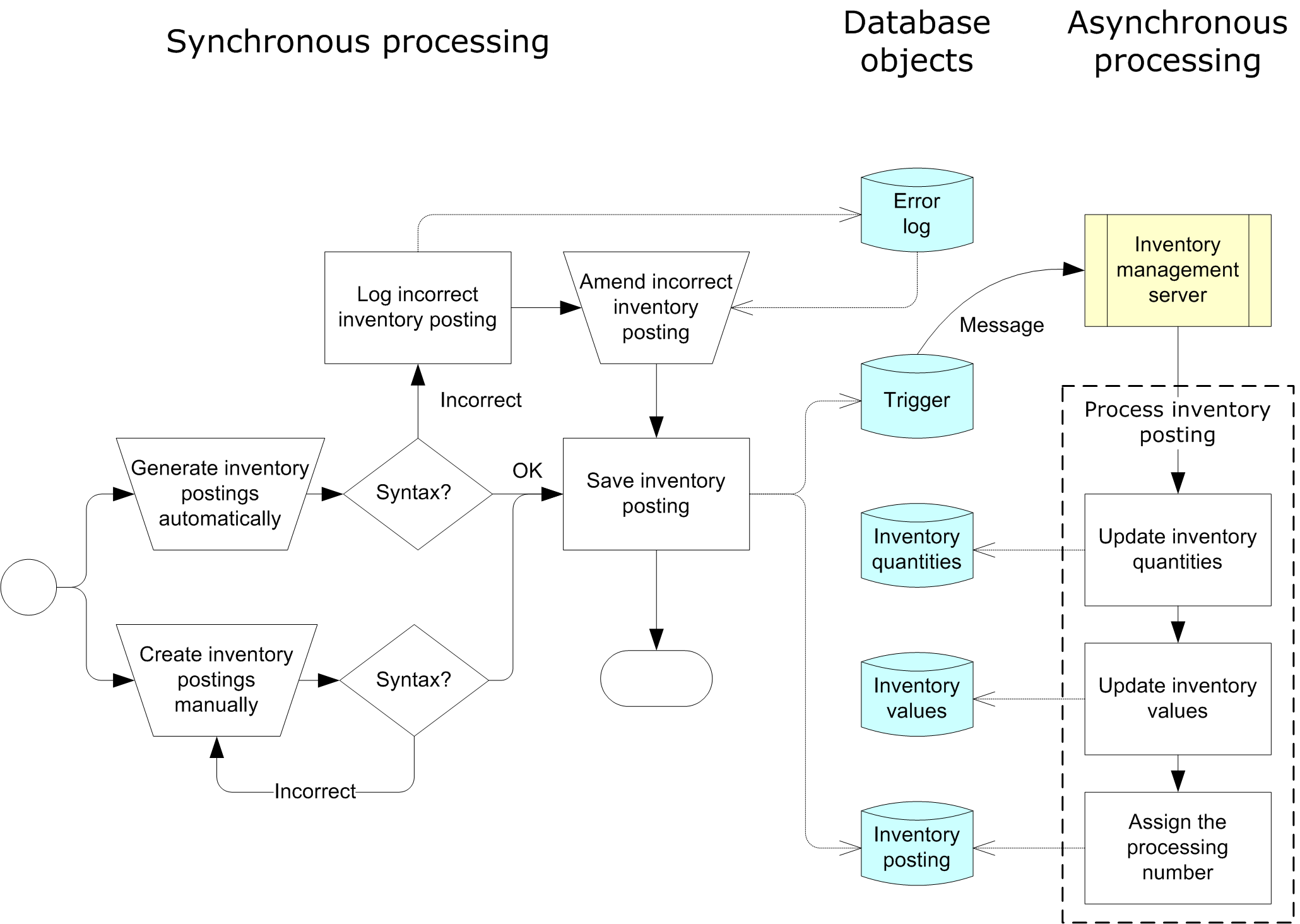
If the inventory posting is created manually, the information will be checked before saving. The inventory posting can only be saved if all information is correct. If, on the other hand, the inventory posting was generated by a process, incorrect or incomplete information results either in the stop of generating or in an entry in the posting error log. Such entries can be subsequently corrected and saved as inventory postings.
When the inventory posting is saved, the inventory management server responsible for the warehouse is notified.
The processing of the inventory posting by the inventory management server occurs asynchronously. During the course of the processing, the inventory management server updates the inventories and the inventory values according to the posting key used.
For the valuation of the floating average price, in the case of receipts the price is taken from the upstream process or from the user entries in the Inventory postings application. This price is written to the inventory posting during the initial, synchronous step of the inventory posting and is no longer changed by the inventory management server. In the case of issues, the floating average price at the time of the processing is always valued by the inventory management server.
A consecutive processing number is then assigned to the inventory posting. The presence of this number indicates that the inventory posting has been successfully processed by the inventory management server.
If the inventory management server is out of operation, an update of the inventory quantities and inventory values will not occur. After start of the inventory management server, all not yet processed inventory postings are processed.
To learn more about the inventory management server and the application of the same name, see the Inventory management server article.