Production module in Comarch ERP Enterprise system allows for conducting the production activity of a company along with handling production processes. The module is divided into the following elements:
- Production structures – allow for defining the full production process. The following elements are production structures: operations, routes, bills of resources, bills of materials.
- Resources – allow for entering resources of a given company and managing them in time. In the system, the resources can be defined as a single resource, group of resources or list of resources.
- Production organization – functions related to the work time management and generating documentation. Additionally, to manage production data, processes handled by batch applications are necessary.
- Production order – the most important application of the Production module, responsible for the production execution in the system
- Posting – group of applications allowing for posting a production process
- External manufacturing – allows for entering production operations executed out of the firm to the process
- Product configuration – in case of the configuration of different product variants, the system allows for creating product configurator
- Calculation of the production inventory values – this function allows for evaluating the materials used in initiated production processes
- Additional functions of the production module – allow for adapting the production structures to a selected production item
The production module can cooperate with other system areas, such as:
- Planning
- Calculations
- Sales
- Inventory management
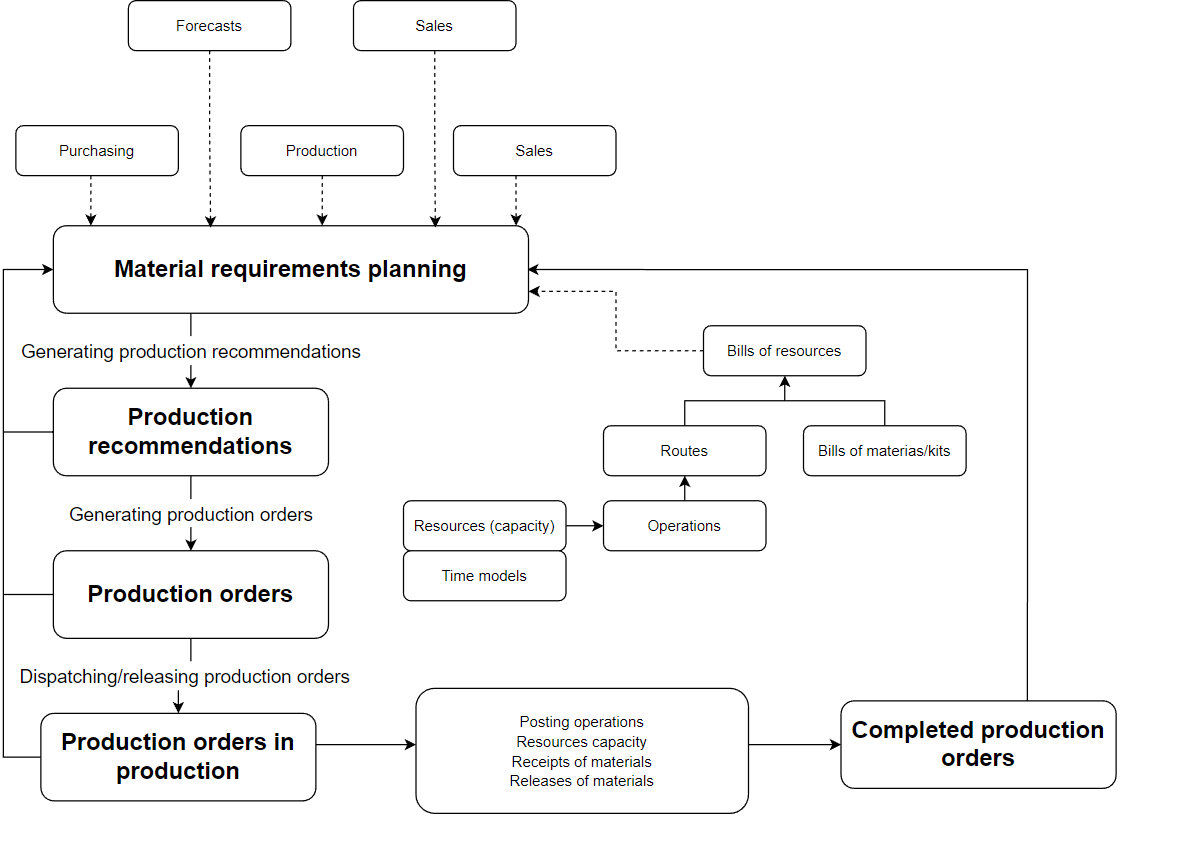
This graph presents the associations in production. It illustrates cooperations between the basic production data and the production process as well as factors affecting the production. Example of definition of a production process in the system can be found in article Example of the configuration of a production process in the system.
Production structures
The production structures allow for defining the data necessary for executing a production process. The system allows for executing production processes on the basis of the production data assigned to a production item in the application Items → Production view, these are:
- Bills of materials – only materials are retrieved to the production, production orders are not planned in time
- Bills of materials and Routes – materials from assigned bill of materials are retrieved for production and operations from assigned route are planned
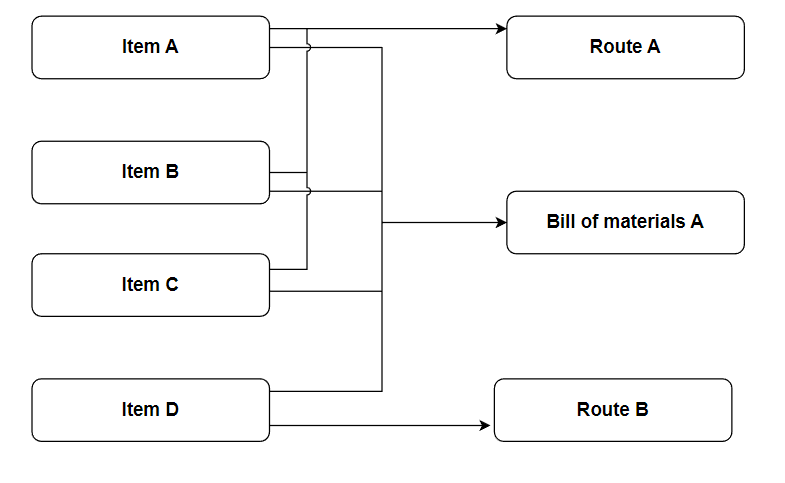
- Bill of resources – materials assigned to the operation according to defined bill of resources are retrieved for production
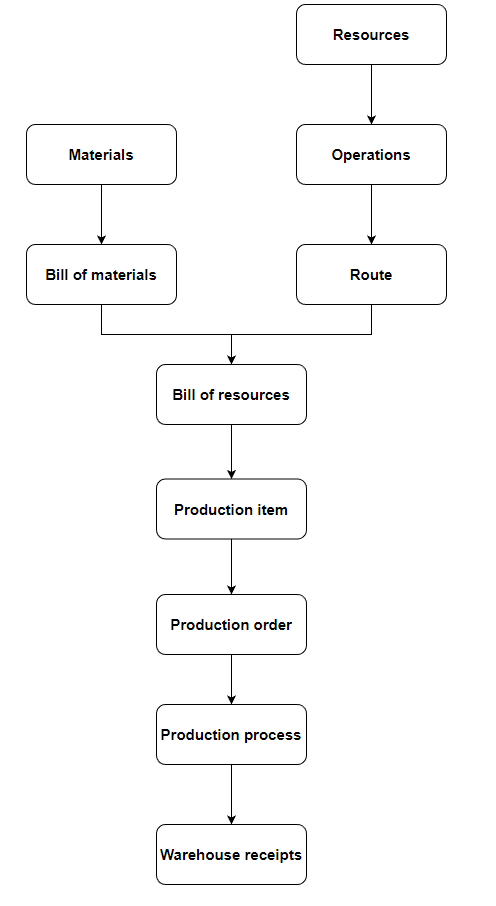
The minimum requirement which must be met in order to execute the production process is creation of a bill of materials containing at least one material and its assignment to the production item. Such setting allows for conducing the production activity based on materials only. It is not necessary to define and use data defined in time (resources, operations and routes).
The following elements represent production structures in the system:
- Bills of materials – list of all elements needed to produce the item. Such list can contain resources, materials, semi-finished products or other bills of resources. One or more bills of materials can be assigned to production items (in production method).
- Operations – activities executed in the production process. Resources necessary to execute a given activity are assigned to them. In the system, there are the following types of operations:
- Operation – operation executed in the company in which the production process was defined. To this type of operations, resources and lists of resources necessary for its execution are assigned.
- External manufacturing operation – operation executed in an external firm
- Internal external manufacturing operation – operation executed in a firm’s affiliate
- Routes – contain operations necessary for producing an item. The order of operations in a route and possible interdependencies between the operations are taken into account when starting the production order.
- Bill of resources – composed of the bill of materials and route. In the bill of resources, materials from the bill of materials are assigned to particular operations from the route. The bill of resources presents a full run of the production process.
In the Production view of the Items application, it is possible to define an alternative production method. Thanks to the alternative production method, other production structures can be assigned to the item and used for its production. The usage of an alternative production method can be also defined with the use of formulas and conditions regarding the bill of materials, route and bill of resources. These structures are called up with the use of the production order.
For each application allowing for defining the production structure, Structure view is available on the identification pane toolbar. It allows for previewing levels of the production structure and simulating defined structures indispensable for executing the production process for entered parameters.
In many cases, the items are subject to numerous technical modifications during the production cycle. Therefore, it is important to track changes made to production structures. It is possible thanks to the following functionalities:
- Master data versioning – allows for defining versions of existing production structures and blocking old versions, as well as previewing older versions of production data
- Change number – allows for defining numbers for added production data, e.g., for a resource added to the operation. Such number defines change made to a given production data.
Resources
For the execution of the production process, resources used in different stages of the production process are required. Resources are represented by machines, people but also electricity or water indispensable for the production. The system allows for defining resources according to the following scheme:
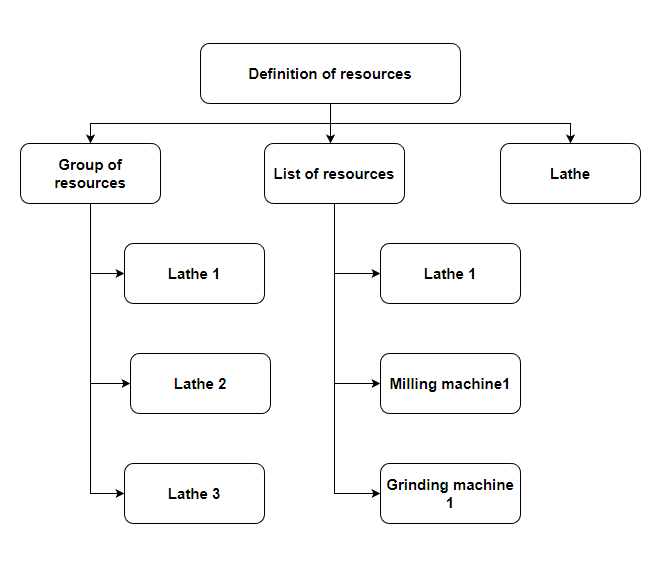
- Resources – are used by the operation in the production
- Bills of resources – allow for assigning different types of resources to one definition Allows for defining, for example, production cell.
- Resource group – allows for creating a group of resources of the same type. The group of resources enables more effective managing of resources efficiency.
Resources are assigned to cost centers which makes it possible to quote the cost of their work. Additionally, they can work in work in time limitation or in a mode unlimited in time, where the user can assign any work unit to them. It allows for defining time-independent resources, e.g., water. Each resource has its own, defined capacity level, on the basis of which its usage is planned.
To enable more efficient managing of resources, the following applications are available in the system:
- Resource capacities – allows for previewing and modifying resource work time
- Resource allocation – allows for checking planned production activities for resources. In the application, it is possible to filter capacity by resources, production order, site or time period. Here, it is also possible to make allocation of resources in graphic mode – offsetting of a given production operation within the buffering time.
- Resource utilization – allows for evaluating the utilization of resources available for production. It presents used resource work time in relation to the available time in a graphic form or as a table. It allows for filtering the capacity by resources, cost center, site, time period or material requirements planning.
Production organization
Time in production
To be able to organize and manage production, in the system must be defined production documentation. Also, the support of batch applications is required.
The time in production is defined on the basis of the company calendar, which contains working days and holidays. The creation of the schedule on whose basis production is planned is presented on the following scheme:
Example of applications affecting specification of the production duration
Shifts – in combination with the time model, the change means a specific work time
Time models – allows for defining work time intervals, e.g., 06:00 am – 9:30 am, 10:00 am – 2:00 pm
Week time model – allows for combining the data from the application Shifts and Time models and assigning them to weekdays. Time models are assigned to resources, which allows for planning their work and capacity.
Production documents
In the Production module, the following production documents are available:
- Production order documents – documents related to released production order
- Material documents – logistic documents related to the material security of the production process
- Work documents – documents related to activities in the production process
- Production orders for external manufacturing – documents related to the process of external manufacturing
The scheme presents the stages of the production process during which the process documentation is generated:
Additionally, for the production order it is possible to generate, depending on the production process definition, related documents:
- Sales orders – if the production order was generated from a sales order (manually or automatically for configured items)
- Product cost calculation – if configured item was calculated automatically or the order calculation was manually associated with the production order
- Purchase orders – for a released production order containing external manufacturing operations
- Receipts of production items – on the basis of the completion notification (and posted receipts) of a production item and related by-products
- Production completions – on the basis of the movement of the item from the main warehouse to the production warehouse, necessary for creating the production item
- Distribution orders – if the order contains the option of the internal external manufacturing
Batch applications
Batch applications allow for handling data entered to the system, as well as deleting, activating and transferring them. During the work, the user can start a batch process, thanks to which it is possible to continue the work in the system without the necessity of interrupting it. The following batch applications are available in the Production module:
- Activate production methods – during the first start of the system, it allows for activating Production methods option which allows for selecting the method of item production at the moment of ordering the production
- Reorganize production master data – allows for deleting production structures marked with deletion marker
- Reorganize set of connected formulas and conditions – allows for deleting entries regarding defined formulas and conditions directly in the database
- Reorganize service bills of material – allows for deleting service bills of materials marked with deletion marker
- Reorganize production orders – allows for deleting production orders marked with deletion marker and all reservations related to it
- Reorganize resources – allows for deleting resources marked with deletion marker
- Reorganize resource groups – allows for deleting groups of resources marked with deletion marker
- Reorganize production recommendations – allows for deleting production recommendations marked
- Check production planning structures – allows for verifying production structures for cyclic references
- Create production orders change history – allows for exporting production orders data used for the cost accounting in CFE (Comarch Financial Enterprise)
- Update change history of production orders – allows for updating production orders data used for the cost accounting in CFE (Comarch Financial Enterprise)
Production order
The production order is the basic production process element. It contains the order of material production or service execution in a specific date and quantity. The production order specifies the operations and materials with the use of which a given item quantity within a specific deadline has to be produced.
The basic settings of generated production orders are defined in production order type, in the Production order types application.
The production order type contains a series of settings possible to configure as predefined for a relevant production order type. They are used for identifying production orders and specifying initial settings. Additionally, in production order types, there is a series of data which is used in the inventory management, accounting or allow for limiting permissions for other organizations.
Example of setting of a production order type:
- Number range used for automatic assignment of numbers to production orders
- Production warehouse, issue warehouse and receipt warehouse
- Posting keys for material issues from the production warehouse
- Settings regarding reservations of material items
- Picking order types – if the production warehouse is provisioned by the main warehouse, the transfer of the material from the main warehouse to the production warehouse is controlled by the picking order
- Purchase order type and delivery order type – if in the production order, external manufacturing operations are included
The production order, depending on its type, can be:
- created manually in the Production orders application
- copied from a production order already existing in the Production orders application
- created on the basis of a sales order
- created on the basis of a production recommendation