Topic overview
If in Customizing application, the storage location control is activated, then the warehouses can be subdivided into warehouse zones and storage locations. The storage location control supports the logistic processes in the sub-divided warehouses. This makes storage location control a function that is not merely used in Inventory Management, but is also integrated into the inventory-related frameworks.
In this article, the most important processes of the storage location control are explained. The applications used and their fields, actions and procedures have been described in other articles.
Processes
The storage location control provides separate strategies for the put-away and withdrawal of items. The following illustration shows which transport processes result from which voucher categories and which process is executed by the warehouse logistic server.
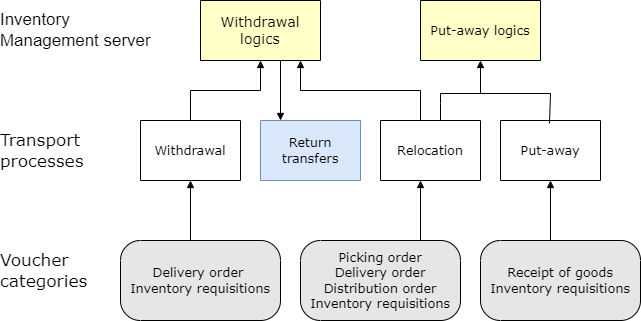
The article Introduction: Transport processes describes the following transport processes:
- withdrawal
- put-away
- relocation
- return transfer
The put-away and withdrawal logic and other processes relevant for the storage location control have been described below.
Put-away logic
The put-away logic determines storage locations for put-away of item inventories. The item inventory to be put-away is defined by the following minimum entries:
- Owners of inventory
- Warehouse
- Items
- Identifier (if the item is managed in identifiers)
- Quantity
The put-away logic first determines the sequence of the warehouse zones. The sequence results from the put-away restriction used. Warehouse zones with the sequence zero (0) are not included. If no put-away restriction is used, then the warehouse zones are sorted by their priorities.
The put-away in sub-divided warehouses takes place in three steps. In each step, all warehouse zones to be included in the determined sequence according to suitable put-away locations are browsed.
- Replenish fixed picking locations with uncovered demand
First included are the fixed picking locations:
- without open receipts
- with a current item inventory that is smaller than the safety inventory item (recorder level).
Picking locations are replensihed according to the replenishment definition. While replenishment, it is attempted to get back to the inventory capacity.
- Replenish non-empty storage locations
In the second step, depending on the replenishment strategy, it is attempted to replenish non-empty storage locations to which the following applies:
- storage locations and slots are item segregated
- current item inventory is smaller than the capacity according to the packaging definition
Storage locations with and without storage units are replenished. Picking locations are replenished up to the maximum inventory level and not to inventory capacity according to replenishment definition.
- Put-away to empty locations or in simple warehouse zones
Finally, it is attempted to put-away item inventory to empty storage locations or slots according to put-away strategy. The put-away can also take place in warehouse zones without storage locations (simple warehouse zones) and the following general conditions must be fulfilled so that the put-away logic can consider the storage location:
- The owner of inventory of the storage location must be the same as for the item inventory to be put-away. The owner of inventory for a storage location can be specified in the Storage locations application or for a storage zone in the Warehouses application.
- The storage location must be usable. The usability of the storage location can be determined in the Storage locations application.
- Storage location must not be full. A storage location is full if the current inventory is same or higher than the highest inventory level. Future issues are not included. The highest inventory level must be specified in the Storage location types or Storage locations applications.
- No future access must be registered for the storage location.
If the storage location is sub-divided into slots, then there cannot be any issues reservation for a slot in which put-away is to take place.
If the storage location is not sub-divided into slots, then there cannot be any issues reservation for the entire storage location.
In storage locations or storage location type fixed location without storage unit and picking location without storage unit put-away for existing open put-aways and withdrawals is also possible if the highest inventory level of the storage location is not exceeded as a result. For storage locations of the fixed location type without storage unit, this is independent of the storage location specification. In this case, the storage location can be filled with different items. Alternatively, you can force an item-only replenishment by specifying the item entry in the storage location type used for the storage location replenishment restriction.
It must be specified for a storage location that a storage unit used may be stored in it during put-away. If the storage unit and the storage location type are not specified, the storage unit specified in the Items, Inventory Management view application is used. If the storage unit is not specified, but the storage location type is known, then the storage unit specified therein is used, provided only one is specified. Otherwise, all usable storage unitis sorted in descending order of size and the first one is used. Usable storage unit is:
- all storage units specified in the storage location type,
- the storage unit that is directly assigned to the packaging unit according to the item master data and, in addition, all storage units that are assigned to packaging units that contain the packaging unit in question.
- If the item inventory has been put-away with put-away strategy bulk additions to existing stock, then deadline for bulk additions to existing stock must not be missed. If the deadline for bulk additions to existing stock has not been missed but the first withdrawal from the storage location has taken place already, then the storage location is also not included.
- If the item inventory is put-away considering the item or identifier segregation, then the storage location or slot must be segregated by item or identifier.
- If a maximum load acceptance or a maximum volume is specified in the storage location type, then these values must not be exceeded with the items or loading units to be stored.
The article Introduction: Storage strategies has a detailed description of the strategies relevant for put-away logic.
Withdrawal logic
The withdrawal logic determines storage locations for withdrawal of item inventories. The item inventory to be withdrawn is defined by the following minimum entries:
- Owners of inventory
- Warehouse
- Items
- identifier (if the item is managed in identifiers)
- Quantity
- QA status
- Packaging (if the item is managed in inventory-managed packaging units) and its binding unit
The relevant storage strategy is first determined for each withdrawal operation. Based on a withdrawal strategy, which results from various settings in a storage strategy, the inevntories of the required item (if necessary, taking into account the characteristic value) are placed in a sequence. This sequence is essentially influenced by the consumption sequence procedure of the storage strategy. Other characteristics are, for example, the priority with which the inventory owner is taken into account and the packaging of the inventory. Further information on determining the inventory to be withdrawn can be found in the article Storage strategies.
Independent of the storage strategy, the withdrawal logic always executes the following steps in the sub-divided warehouses:
- Determine item inventories
Item inventories that do not match are expressly excluded in the determination. An exclusion takes place when the warehouse zone does not have the Released status.
- Sort item inventories
The sorting criteria depend on the item inventories as well as withdrawal strategy, withdrawal restriction and, for logistics units, also on the preferred packaging setting. These settings determine the sequence in which the item inventories are withdrawn.
- Withdraw item inventories
The sorted item inventories are used for the withdrawal. If an item inventory cannot be withdrawn, the next item inventory is continued. This step is repeated until either the required inventory quantity is withdrawn or all item inventories are used. In the latter case, the withdrawal cannot be completed successfully.
The determination of withdrawal locations takes place through the following steps:
- Withdraw canceled quantities
If the withdrawal strategy FIFO is being used and the preferred withdrawal of canceled quantities is activated, then first the canceled quantities are determined at reserve locations or slots. A cancellation quantity is when the item inventory is smaller than the capacity according to the packaging definition. A cancellation quantity is also present if the item inventory matches the packaging definition but the reserve location or slot is item segregated. With the withdrawal strategy strict FIFO cancellation quantities cannot be withdrawn as preference.
- Withdraw entire storage units
Entire storage units are determined in the second step. A whole storage unit is a storage unit plus its current inventory. It is immaterial whether the storage location type permits storage unit or not. Item inventories included in the first step are not considered again.
If the withdrawn inventory is larger than the required inventory, then the withdrawal takes place on the basis of the picking strategy either per bin picking or through the picking point with final return transfers.
If the storage location contains a fixed picking location, then special picking and withdrawal through the picking point is not permitted. Any remaining quantities are taken from the picking location. In such a case, the withdrawal logic determines only item and identifier reserve locations, whose item inventory is less than or equal to the remaining inventory.
- Withdraw the remaining quantities from the picking location
If the withdrawal strategy FIFO is used and a fixed picking location is available in the storage location, then any remaining inventory from this fixed picking location is withdrawn. If the warehouse zone does not have any fixed picking location, then any remaining inventory is withdrawn on the basis of the picking strategy in the previous step.
In the calculation of the withdrawal quantity in a storage or slot location, all item units (parallel inventory units and packaging units) are taken into consideration. If withdrawal restrictions are included in a concrete withdrawal procedure, then specific item units are excluded or only specific item units are included. In the article Withdrawal restrictions, you will find a detailed description of the inclusions and exclusions of inventory units and the withdrawal in inventory units.
Additionally, the item units are excluded that could only be calculated with rounding differences in the base unit.
- Inventory item A without parallel inventory units, base unit pc. (0 decimal point), a packaging unit Pal correspond with 10 pcs.: The unit Pal is included in withdrawal, since it can be exactly converted with the factor 10 in the base unit pc.
- Inventory item B without parallel inventory units, base unit pkg (commercial unit with 0 decimal point), a packaging unit pc. correspond with 10 pkg: the unit pc. is excluded from the withdrawal, since it can be converted with factor 0.1 to the base unit pkg, but is limited to 0 decimal point.
- Inventory item C without parallel inventory units, base unit m (2 decimal points), four packaging units ctn correspond with 1 m: The unit ctn is included in withdrawal, since it can be exactly converted with the factor 0.25 in the base unit m.
In withdrawal, the following general conditions must be fulfilled so that the withdrawal logic can consider the storage location or item inventory:
- The owner of inventory of the storage location must be the same as for the item inventory to be withdrawn. The owner of inventory of the storage location can be specified in the Storage locations application or Warehouses application in the warehouse zone definitions.
- The storage location must be usable. The usability of the storage location can be determined in the Storage locations application.
- Storage location must not be empty. A storage location is empty, if the current inventory is zero. Future receipts are not included.
- The QA status of the warehouse zone in which the storage location is, must have the Released value. Specify the QA status in the Warehouses application.
- The item inventory must be stored in the given storage unit. If the storage unit is not given, then item inventories are included independent of the storage unit.
- If the item inventory has been put-away with put-away strategy bulk additions to existing stock, then either the storage location must be full, or deadline for bulk additions to existing stock must not be missed. If a withdrawal has taken place since the last put-away in the storage location, then further withdrawals are also permitted.
- The QA status of the withdrawal identifier must have the Released value. Specify the QA status in the Identifiers application.
- For storage locations of the type Storage location with storage unit, automatic withdrawal will lead to the creation of inventory orders if there are still open put-aways. Please note that inevntory is always withdrawn without storage unit, even if the entire available inventory is to be withdrawn.
The article Introduction: Storage strategies has a detailed description of the strategies relevant for withdrawal logic.
Picking order
The picking process can be organized in different ways in a company. The picking options that can be mapped with the system are described below.
- Serial picking
An inventory order is generated for each picking process, which is processed by an order picker. - Parallel picking
Several inventory orders are generated for each picking process, which can be processed in parallel by the pickers. For this purpose, identifiers can be specified that are used to automatically group the items into inventory orders. These can also be loading units, for example, if these are used as grouping identifiers. - Order-related picking
The inventory orders are generated based on just one order. An inventory order and, if necessary, a return transfer order are generated for each warehouse. - Cross-order picking
The inventory orders are generated based on several picking orders. The picking order line items with the same inventory owner, warehouse and item are first automatically combined in an inventory requisition line item. Inventory orders are then automatically generated from the inventory requisitions. - Item-related picking
Picking order line items that list the same item are combined in an inventory order.
Automatic identifier allocation by the inventory order
If a no identifiers have been specified in a previous process, then the withdrawal logic carries out an automatic identifier allocation while generating an inventory order. In doing so identifiers that have been found on the relevant withdrawal locations are determined. In contrast to the identifier allocation by picking or delivery order, no identifiers are allocated to the sub-divided warehouses that cannot be withdrawn. Therefore, it is recommended that inventory order and picking types must be configured in such a way that an automatic identifier allocation takes place only in simple warehouses. The identifier allocation must take place in the sub-divided warehouses only with inventory order generation.
Vouchers and voucher references
Inventory order voucher
An inventory order determines the item transport within a warehouse sub-divided into storage locations. Inventory orders are automatically generated for the withdrawal and put-away storage locations determined by the storage strategies. Alternatively, they are generated after an inventory requisition has been entered and a corresponding action has been executed. Inventory orders cannot be entered.
Inventory orders can only be assigned to one inventory management server. If a receipt of goods is entered for several sub-divided warehouses, and the warehouses are assigned to different inventory management servers, then an inventory order per related inventory management server is generated.
Inventory requisition voucher
An inventory requisition is a means of manually recording the relevant data for inventory movements in warehouses managed by storage locations. From the inventory requisition, and applying put-away and withdrawal strategies, a concrete inventory order is generated.
Voucher relationships
In the voucher references chain for the inventory order, following upstream vouchers are visible if they are connected with the order through a voucher relationship:
- Inventory requisition – if the inventory order is generated from an inventory requisition, then the inventory requisition is displayed as predecessor in the voucher references chain.
- Receipt of goods – if the inventory order is generated while posting a receipt of goods, then the receipt of goods appears in the voucher references chain.
- Picking order – if the inventory order is generated from a picking order, then the picking order appears in the voucher references chain.
- Delivery order – if the inventory order is generated from a delivery order, then the delivery order appears in the voucher references chain.
For more details on the display and functions of voucher references chain, refer to the article Voucher references chain.
FIFO date
In all withdrawal strategies, the item inventories are determined according to their FIFO date. FIFO corresponds to the assumption that inventory that was put away first will also be withdrawn first. How FIFO date is calculated depends on whether the item is managed in identifiers and/or in which identifier it will be managed.
If a new inventory record is generated in put-away (business object), then the item inventory receives a new FIFO date. If no new put-away is generated in put-away, then the inventory takes the FIFO date from existing item inventory.
For more information more about the FIFO date, refer to articles
- Identifier allocation
- Introduction: Transport processes
Settings
The settings described in the following chapters are required in order to use the storage location control:
- Customizing
- Item
Customizing
To be able to use the applications and functions for storage location control, activate the Storage location control function under the main Inventory management function in the Customizing application.
You can find further information in this article: Customizing: Inventory management.
Item
You define the inventory-managed packaging units in the Items application. You can also define a put-away strategy for each item.
Further information can be found in these articles:
- Items, Base view
- Introduction: Business processes with binding packaging specifications
Business entities
The warehouse inventories are saved in a simple warehouse at the warehouse level in the business entity:
com.cisag.app.inventory.stock.obj.WarehouseStock
detailed inventory
com.cisag.app.inventory.stock.obj.WarehouseStockSum
accumulated item/identifier inventories
The warehouse inventories are saved in the sub-divided warehouses at the level of the warehouse and storage locations in business entities com.cisag.app.inventory.obj.UnitOnhand
and its dependent com.cisag.app.inventory.obj.UnitOnhandDetail
.
The reservations and identifier reservations are saved at the level of the warehouse. They can therefore not be displayed in the cockpit application for inventory queries (Cockpit: Storage location inventories, Cockpit: Storage location inventories/Items, Cockpit: Storage location inventories/Identifiers).
The storage location reservations are saved at the level of the storage location. They are displayed in color in the Storage location query application and directly in the cockpit applications for inventory queries.
Further information on identifiers and identifier and storage location reservations can be found in these articles:
- Introduction: Identifiers
- Identifier reservations
- Storage location reservations
You will find a short description of the business objects generated during put-away at the storage location level.
Item inventories
While put-away of an item inventory at an empty storage location the following business objects instances are generated:
- 1
UnitOnhand
– per slot or warehouse zone (and per inventory owner) - 1
UnitOnhandDetail
– per combination of item, identifier (batch, lot, serial number with inventory management) and packaging unit
– per loading unit - 1
CurrentUnitOnhand
– only unpacked inventories without loading unit content and loading unitssynchronously updated inventory of sub-divided warehouses (warehouse zone and storage location inventories) SerialNumberOnhand
– synchronously updated inventory for serial numbers
Loading units
While put-away of a loading unit at an empty storage location, the following business objects instances are generated:
- 1
UnitOnHand
– per slot or warehouse zone (and per inventory owner) - 1
UnitOnHandDetail
– packed inventory: per combination of item and identifier (batch, lotm serial number with inventory management) - n
UnitOnhandDetail
– per loading unit - 1
UnitLoadOnHand
– unique loading unit inventory
– (current attribute) synchronously updated inventory - n
UnitLoadOnhandDetail
– loading unit content in the inventory - n
CurrentUnitLoadOnhandDetail
synchronously updated loading unit content in the inventory
–SerialNumberOnhand
unique serial number inventory
– current attribute: synchronously updated inventory for serial numbers actualUnitLoadNumber shows whether the serial number is in a loading unit
You can query inventories in loading units with the following applications:
- Cockpit: Loading unit inventories
- Cockpit: Storage location inventories
Put-away at bulk storage locations
While put-away of an item inventory with the help of put-away strategy bulk additions to existing stock, the following business object instances are generated:
- 1
UnitOnhand
– per storage location or warehouse zone (and per inventory owner) - 1
UnitOnhandDetail
– per combination of item, identifier (batch, lot, serial number with inventory management) and packaging unit - 1
CurrentUnitOnhand
– only unpacked inventories, no loading unit content and no loading units
– synchronously updated inventory of sub-divided warehouses (warehouse zone and storage location inventories) SerialNumberOnhand
– current attribute: synchronously updated inventory for serial numbers
The attribute currentStorageUnitCount
in the business object UnitOnhand
shows the number of storage units put-away currently in the storage location. Since only full storage units are permitted, the current inventory can be determined with the help of this attribute.