Topic overview
The Material requirements query application displays the results of a planning run for each item, considering the actual demand origins and demand coverages.
The following questions can be answered in the application:
- What are the components of demand for a given item and when will they be covered?
- What item quantity must be produced at what time point?
- What requirements exist at what due date?
- What conflicts are there with regard to order due dates and quantities?
The Material requirements query application makes it possible to preview and adjust demands as long as it takes to reach an optimum combination of production assortment and its utilization.
The Material requirements query application makes it possible, depending on a given item, to preview planning recommendations for internal distribution (in a multi-site environment only), external purchasing, or production. The application displays the primary and secondary demand, demand forecast numbers, current inventory, and demand origin and coverage. With this application, it is possible to display and change the results of material requirements planning. The application is composed of:
- Header – it allows defining an item whose planning data is to be displayed
- Work pane – it displays planning data
Header

Apart from the standard buttons, the application header contains the following buttons:
- [Select action] → [Update planning] – it recalculates all production structures modified manually in planning recommendations. If a secondary demand is modified for semi-finished goods (in the Demand table), manual changes made for the semi-finished goods in a planning recommendation are retained.
- [Select action] → [Discard changes] – it allows resetting all changes made in the Demand table
The application header contains the following fields:
- Item (required) – select an item for which planning run results should be edited. The item cannot be a reference item and must have inventory management data, purchasing data, and production data.
- Unit – the base unit of the selected item is displayed
- Time period – select the time period for which you wish to edit the planning run results. If the application has already displayed the results of another planning and the time period does not match the current planning, it is possible to accept the time period of the new planning in this field by deleting the content and selecting [Refresh] in the standard toolbar.
- Period duration – if required, select the detailing level for displaying planning periods. The day-accuracy method is always used as part of the internal planning logic. In turn, to get a week display, the user can enter 7 in the Period duration field.
- Material requirements planning (required) – select the desired material requirements planning. The last opened planning is the default planning. Since there can be several planning runs and each planning can be derived from different parameters, different results may be displayed for a single item.
- Status – it displays the status of a given material requirements planning retrieved from the Status tab of the Material requirements planning application for a selected item
- Site – it is only used in multi-site environments. Select the sites for which demands are to be displayed.
- Item status – it displays the planning status of a selected item
Work pane
The planning work pane makes it possible to preview and edit demand data. It is composed of the following tabs:
- Demand – it enables the user to preview and edit planning data in a table
- Diagram – it displays planning data in a graphic form
- Planning data – it displays planning data for an item selected in the header
- Classifications – it displays a classification assigned to a selected item
Demand tab
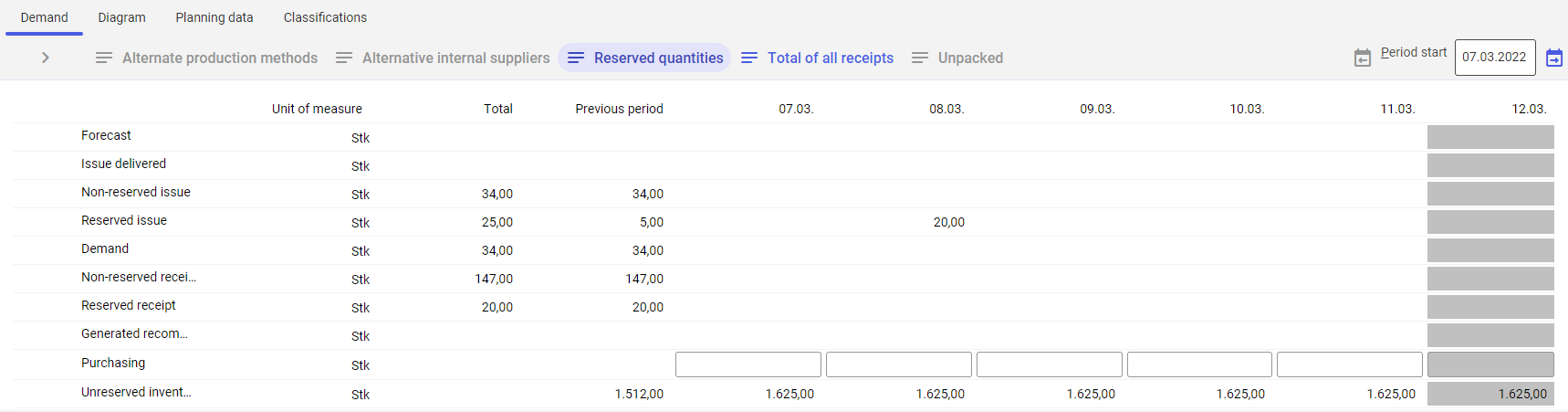
The planning run result for each item is displayed on the Demand tab. The demands determined can be changed or reworked manually. The results are displayed in a matrix:
- Planning periods are displayed horizontally
- Planning run results and/or demand origins and demand coverages are displayed vertically
The planning run results header contains the following buttons:
- [Alternative production methods] – if an item has been assigned alternative production methods, the [Alternative production methods] button can be used to display a demand line for each permitted production method.
- [Alternative internal suppliers] – using this button, it is possible to display all sites in which purchasing can be done internally for items derived from distribution orders (in a multi-site environment)
- [Reserved quantities] – using this button, issues, receipts, and the inventory of reserved and unreserved quantities can be displayed separately for the line items. By default, the button is activated if reservations are enabled in the Customizing application for at least one displayed site.
- [Total of all receipts] – using this button, it is possible to display a line containing the total of all item receipts
- Period – it displays planning periods. Depending on the selected detailing level (period duration), planning results can be different. Note that the Total column displays the sum of all current demands within a given planning period. Days marked in the calendar as Non-working day are marked in gray. The buttons [Display previous period] and [Show next period] make it possible to change the scope of previewed planning data.
The planning results table contains the following lines:
- Forecast – it displays the planned demand quantity derived from the demand forecast. Quantities resulting from a demand generated on the basis of demand forecasts entered in the detailing level of the week are calculated only within a given week, considering working days according to the company calendar. The same is applicable for monthly forecasts. Demand forecasts are not included within the planning time fence. If no working days are defined for a week in the company calendar (i.e. the entire week is a non-working week), the demand of the forecast of the last working day prior to that is included.
- Issue delivered – this line is taken into account if an item is planned with a forecast. It displays all issues that affect the forecast quantity.
- Issue – it displays the planned demand quantity derived from the following demand origins:
- Sales quotations
- Sales orders
- Material reservations in Production
- Distribution orders (in a multi-site environment)
- Distribution recommendations (in a multi-site environment). The line is only visible if the button [Reserved quantities] is not activated.
- Non-reserved issue – this line displays the unreserved issue quantity for demands. The line is only visible if the button [Reserved quantities] is activated.
- Reserved issue – this line displays the reserved issue quantity for demands. The line is only visible if the button [Reserved quantities] is activated.
- Demand – it displays every planned demand quantity that results from the comparison of forecasts, delivered issues, and started issues. A definite demand is any planned demand that is used for determining the planned inventory and a possible additional demand (in purchasing or production).
- Receipts – it displays the planned receipts quantity derived from the following demand coverages:
- Purchase orders
- Production orders
- Co-product/raw material reservations in Production
- Purchasing recommendations (including manually created purchasing recommendations)
- Distribution orders (in a multi-site environment)
- Distribution recommendations (in a multi-site environment)
- Non-reserved receipt – this line displays the unreserved receipts quantity. The line is only visible if the button [Reserved quantities] is activated.
- Reserved receipt – this line displays the reserved receipts quantity. The line is only visible if the button [Reserved quantities] is activated.
- Generated recommendation – it displays the quantity from recommendations for a given item that have been generated as a result of material requirements planning or entered manually. The data is retrieved from purchasing, production, or distribution recommendations.
- Purchasing – it displays the additional demand for purchasing. This purchasing recommendation can be changed manually.
- Internal purchasing – it displays the additional demand for internal purchasing (distribution). This purchasing recommendation can be changed manually.
- Production – it displays the additional demand for production (according to the standard production procedure, i.e. with the demand defined as Production). This production recommendation can be changed manually.
- Inventory – it displays the planned inventory after taking into account the demand and planned deliveries
- Unreserved inventory – this line displays the unreserved inventory. The line is only visible if the button [Reserved quantities] is activated.
- Reserved inventory – this line displays the reserved inventory. The line is only visible if the button [Reserved quantities] is activated.
Purchasing demand – production demand
The decision whether an additional demand determined during planning will be purchased or produced (internally or externally) depends on the demand coverage assigned in the item production data. If an item can be purchased and produced as well, the default demand coverage can be changed. The user may manually enter additional quantities to be processed in the purchasing process in the Material requirements query application. Splitting of the demand quantity is possible within a planning period.
If a production method is used, each production requirement is always interpreted with the standard production method. If the item has been assigned more production methods, the [Alternative production methods] button can be used to display a demand line for each permitted production method.
For items with distribution orders assigned, the source site is always the internal main supplier of the item. All sites in which purchasing can be done internally as well may be displayed with the [Alternative internal suppliers] button.
More information and details on the process of demand determination may be found in the Material requirements planning article.
Demand origin

The corresponding demand origins/coverages are displayed on the basis of existing orders and additional demands determined.
- Demand origin/coverage on the basis of existing orders:
- Sales quotations
- Sales orders
- Purchase orders
- Distribution orders (in a multi-site environment)
- Production orders
- Planned demand coverage:
- Production recommendations
- Distribution recommendations
- Purchasing recommendations
- Planned demand origin that results from production recommendations associated with items of the upstream production level:
- Planned material reservations in production
- Planned co-product reservations in production
- Planned demand coverage/origin resulting from kit items (kits):
- Planned demands for kit items for components
- Planned demand coverage by components at a kit item level
The list header contains the following buttons:
- [Origin] – the demand coverage/origin can be shown/hidden using this button for existing sales quotations, sales orders, purchase orders, distribution orders (in a multi-site environment)
- [All periods] – all periods, i.e. the entire planning horizon, can be displayed using this button
The list columns are described below:
- Category – a category is displayed using separate symbols for:
- Sales order
- Purchasing order
- Production
- Internal purchasing
(in a multi-site environment)
- Sales order
- Order/recommendation – an order type, order number, and line item number are displayed for existing orders. The following texts are displayed for demand coverages that have not yet been converted into orders:
- Production: Production recommendation
- Purchasing: Purchasing recommendation
- Internal purchasing: Issues from distribution recommendations or Receipts from distribution recommendations
The Upstream production recommendation text is displayed for planned demand origins/coverages that result from production recommendations of items of the upstream production level.
If a kit item is created, the Material requirements query application generates a demand recommendation and displays the text Demand for kit item.
Determining the Demand coverage for kit items value in the Items application (Planning view) affects the method of calculation of item availability. If the Kit option is selected, the system will calculate demand resulting from the entire kit. In turn, if the Components option is selected, demand will be calculated at the component level.
The Indefinite demand coverage text is displayed if a planning recommendation has been calculated but the corresponding item data is missing. It may be so if the Production option has been entered in the Demand coverage field in the Items application (Planning view), but relevant production data has not been included, which makes it impossible to determine the coverage method for the created demand.
- Due date – a due date displayed for existing orders
- Quantity – the quantity of the demand origin/coverage in the base unit of a given item
- Reserved quantity – the reserved quantity of the demand origin/coverage displayed in the base unit of a given item
- Site – it displays an organization in which a demand exists
- Note – displayed depending on the demand type:
- Production orders: Production items
- Purchase orders: Delivery partner
- Sales orders: Ordering party
- Sales quotations: Quotation recipient
- Distribution orders: Source/Target site
- Production recommendations: The text Generated manually is displayed for manually changed production recommendations
- Purchasing recommendations: The text Generated manually is displayed for manually changed purchasing recommendations
- Distribution recommendations: Source/Target site
- Planned material reservations: Production item of the planned production order
- Planned co-product reservations: Production item of the planned production order
- Demand for kit item: The upstream kit item
- Receipt from an inventory requisition
- Issue from an inventory requisition
- Co-product
- Status – the status of the order line item is displayed for existing orders
- Configured demand coverage/origin element – for configurable demand coverages, the
is displayed. These orders and recommendations are treated separately as part of the Planning framework. More information may be found in the Material requirements planning article.
- Conflicts – it displays the conflict level, if any, with the use of symbols. More information may be found in the Cockpit: Planning conflicts article.
Diagram tab
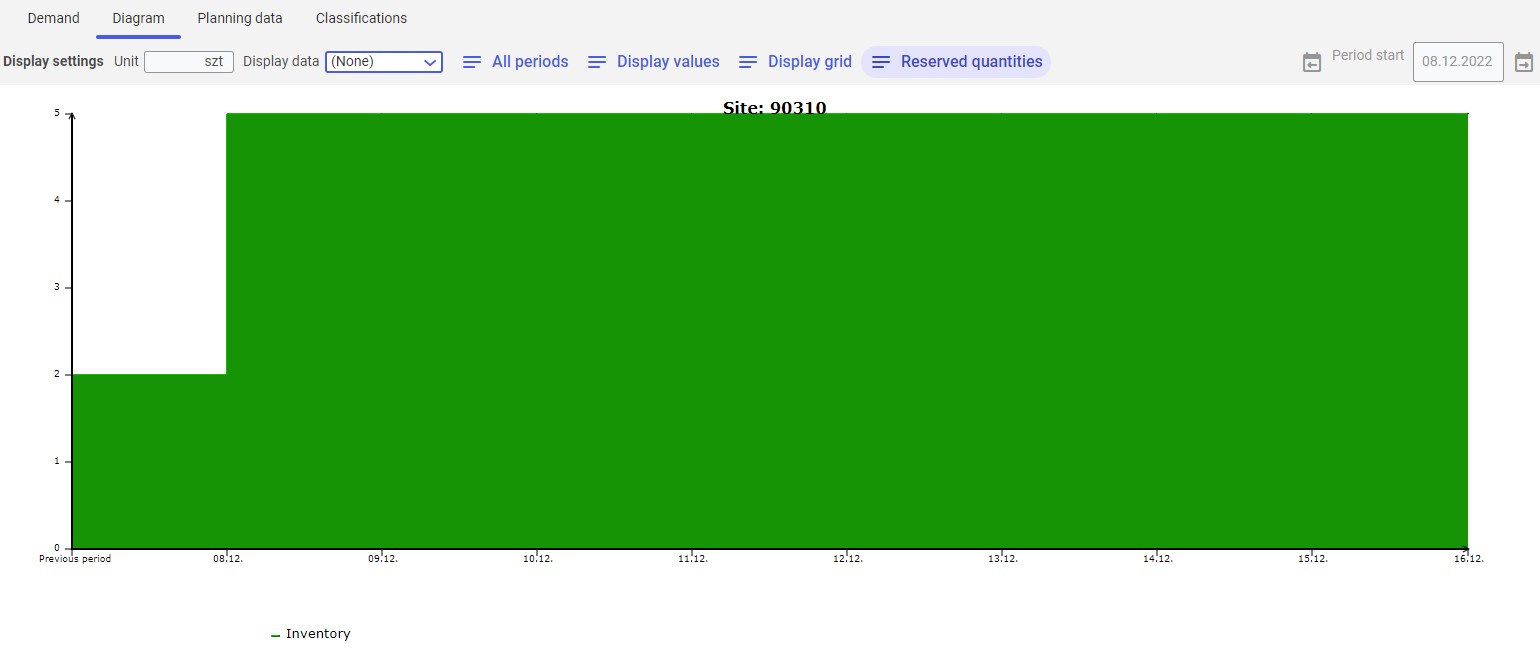
The planned inventory is displayed graphically. The diagram always shows fixed 10 periods (10 days). Optionally, the diagram may also include:
- Unit – it displays the unit of presented data
- Display data – it allows the user to define the type of data displayed in the diagram; by default, inventory level is displayed. The diagram may contain:
- Forecast
- Demand
- Issue
- Non-reserved issue
- Reserved issue
- Non-reserved receipt
- Receipt
- Purchasing
- Production
- Receipts excluding production and purchasing
- Minimum inventory level
- Issue delivered
- Generated recommendation
- Total of all receipts
- [All periods] – it displays all periods, i.e. the entire planning horizon
- [Display values] – it displays the values of displayed data for each day
- [Display grid] – it displays additional horizontal and vertical lines in the diagram to make it easier to read
- [Reserved quantities] – it affects the display of the inventory. When the button is active, the inventory is displayed excluding reservations. If the button is inactive, reservations have no influence on the display of the inventory. If several sites have been entered in the query pane in a multi-site environment, an individual diagram is generated for each site and displayed one after another on the tab.
Planning data tab
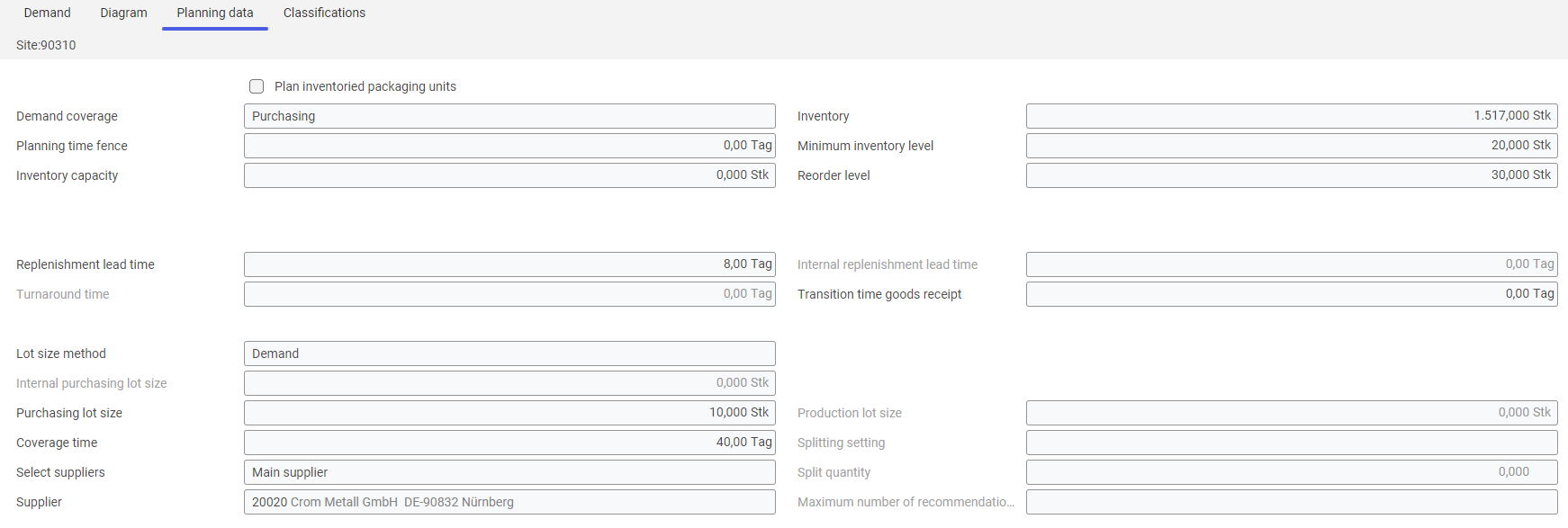
Information on item planning is displayed under the Planning data tab. This data is displayed for each site if several sites are included in the planning (in the case of a multi-site environment). The data is retrieved from the Items application for a material selected in the Item field and from the Material requirements planning application.
The detailed descriptions of fields on the tab may be found in the articles Material requirements planning and Items, Planning view.
Classifications tab
This tab displays information for classifications 1 and 2 of the purchasing item and production item.
- Classification 1 – production item classification 1 (item production data)
- Classification 2 – production item classification 2 (item production data)
- Classification 1 – purchasing item classification 1 (item purchasing data)
- Classification 2 – purchasing item classification 2 (item purchasing data)
Authorizations
Authorizations can be assigned by means of authorization roles, as well as by assigning an organization. The authorization concept is described in the Authorizations article.
Material requirements planning processes such as the acceptance of changes, generation of production orders etc. can only be carried out by an editor assigned to the material requirements planning.
Organizational assignments
Planning results related to a given item can only be displayed in the Material requirements query application if the user is assigned to the item’s inventory management organization.