Customizing: Production application
Customizing → Production
Effects of Production function activation
The Production framework can be activated under Customizing → Production and is used to:
- create and manage production-specific items
- edit and activate the Production view for items
- define processes in the applications under Production framework
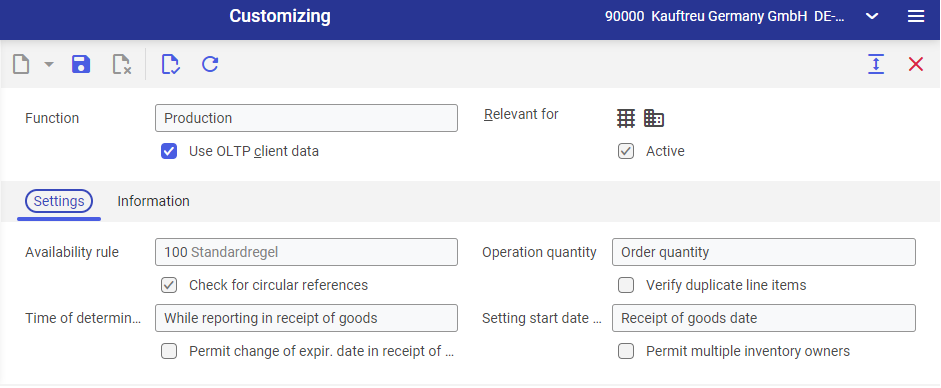
Settings tab
Following are the fields available in the Settings tab after activating the Production function:
Availability rule – you can select the default availability rule in this field. An availability rule in production is used to define which system objects to take into account in production orders. It is defined in the Availability rules application.
Operation quantity – determines the way of calculating an operation quantity in production orders. Selectable options are:
- Order quantity – the operation always contains the default quantity from the order header
- Execution quantity – the operation contains the quantity specified as planned
Check for circular references (parameter) – if selected, the system checks circular references to other production line items entered for data. In case of defining long production processes with large number of references for individual resources, the verification process can be time-consuming, hence, it is recommended to deactivate this function. The function can be activated at any moment during work with the system. For complex production structures, it is recommended to use the batch application Check production planning structures.
Verify duplicate line items (parameter) – if selected, the system checks whether line items in the built process does not contain duplicated data definitions. In case the system finds any duplicated master line items, a warning message will be displayed. The function can be activated at any moment during work with the system.
Time of determination of identifier – specifies the time to define an identifier for a production item. Selectable options are:
- While generation the production order without abort function – an identifier is defined or generated during creation of a production order.
- While generation the production order with abort function – an identifier is defined or generated during creation of a production order with an option of aborting the production order generation.
- While reporting in receipt of goods – an identifier for a production item is defined at the time the goods are received in a warehouse in the Receipts of goods application.
- When dispatching the production order – an identifier is defined or generated during dispatching of a production order.
- When releasing the production order – an identifier is defined or generated after releasing the production order.
Setting start date for expiration date determination – defines the start date from which the expiration date of a production item is to be specified. Selectable options are:
- Generation date of identifier – the start date receives the identifier creation date for the produced material.
- Receipts of goods date – the start date receives the produced material’s date of receipt.
- None – no expiration date specified.
Permit change of expiration date in receipt of goods (parameter) – changes the expiration date when the goods are received in warehouse. It generates an additional voucher related to this action. The function can be activated at any moment during work with the system.
Permit multiple inventory owners (parameter) – activates the option of verifying the material availability and reserving material for multiple inventory owners (organizations). If selected, in Production orders application it is possible to define multiple organizations for material line items, in which availability of a given material is to be verified. The function can be activated at any moment during work with the system.
Customizing → Production → Documents
It is used to define and activate vouchers that will be generated together with a production order. For more information about this function, refer to the article Production vouchers.
Customizing → Production → Configuration
This function activates the product configuration tool. If activated, it is possible to use the product configuration rules in sales quotations, sales orders and production orders. If deactivated, the Product configuration rules application is not available.
Customizing → Production → Method
This function activates alternative production methods for items. It cannot be deactivated if alternative production methods are already defined for items. For more information about this function, refer to the article Items, Production view.
Customizing → Production → External manufacturing
This function activates an external manufacturing for an organization. For more information about this function, refer to the article External manufacturing.
General tab
In this tab, you can define the following general settings regarding external manufacturing:
Automatic shipment picking – if selected, the system releases automatically the materials for dispatch to an external manufacturer after the operation preceding the external manufacturing is completed.
All BOM line items as material provided to vendor – if the bill of resources includes a bill of materials and a routing with only one external manufacturing operation, the system will assign all BOM line items to the specified external manufacturing operation, thus as a material provided to vendor.
External external manufacturing tab
In this tab you can define the following settings related to the operation of external external manufacturing:
Purchase order type – in this field you can select the generated production order for external manufacturing. Purchase order types are defined in Purchase order types
Production issues trigger – in this field you can specify the time to debit an account for the work performed by an external manufacturer.
- Delivery – an account will be debited when goods are dispatched to the external manufacturer.
- Processing by external manufacturer – an account will be debited when goods are processed by the external manufacturer.
- Receipt from external manufacturer – an account will be debited when goods are received from the external manufacturer.
Transit warehouse – defines a warehouse in which the dispatch and receipt of goods for an external manufacturer will be processed. It is created in the Warehouses Allowable warehouse type is Virtual warehouse.
External external manufacturing – supplier data tab
In this tab you can define details of suppliers’ performance, such as:
Start of work – defines the start time of external manufacturer’s working hours.
Daily capacity – specifies external manufacturer’s daily production capacity for outsourced production. It can be specified in hours, minutes or seconds.
Company calendar type – specifies the calendar the external manufacturer works by. A new calendar can be defined for the external manufacturer in the Company calendar types
Internal external manufacturing tab
In this tab you can define the following settings related to the operation of in-house external manufacturing:
Activate internal external manufacturing – activates in-house external manufacturing.
Effect in case of date change – specifies the effects in case of changing the date in a production order with an internal external manufacturing operation. Selectable options are:
- Notification with automatic scheduling – the person responsible for a production order in the site executing an in-house external manufacturing operation will be notified about changed date of the source production order. Changing the source production order date will change automatically the date of the production order in the site executing the in-house external manufacturing operation.
- Notification without automatic scheduling – the = person responsible for a production order in the site executing an in-house external manufacturing operation will be notified about changed date of the source production order. The date of the production order will not change in the site executing the in-house external manufacturing operation.
- Without notification with automatic scheduling – changing the source production order date will change automatically the date of the production order in the site executing the in-house external manufacturing operation. The person responsible for the production order in the site executing the in-house external manufacturing operation will not be notified about it.
Start of work – specifies the start time of external manufacturer’s working hours.
Daily capacity – specifies internal manufacturer’s daily production capacity for outsourced production. It can be specified in hours, minutes or seconds.
Customizing → Production → Reportings
The Reportings function activates the following settings related to feedback from production:
Settings tab
Overdelivery on receipt – a percentage value by which the manufactured quantity in a production order can exceed the target quantity defined in that order. Any other quantity will make it impossible to complete the production order.
Underelivery on receipt – a percentage value by which the manufactured quantity in a production order can be less than the target quantity defined in that order. Any other quantity will make it impossible to complete the production order.
Reporting via last operation – if selected, a production order will complete after the last operation is reported and the receipt of the manufactured item will be taken in the warehouse automatically. Setting of this parameter can be changed when creating a production order type in Production order types
Posting key – assigns a posting key for the purpose of classifying transaction flags in the system. Posting keys are defined in the Posting keys
Open quantity as default – if selected, then the quantity suggested by default in Production issues application is the material’s open quantity for a production order.
Customizing → Production → Number ranges
This function activates and assigns number ranges to the following objects:
- production order types
- resources
- resource groups
- week time models
- time models
- bills of resources
- product configuration steps
- product condition lists
- product configuration characteristics
- product conditions and actions
- service bill of material
Number ranges are defined in Number ranges application.
Customizing → Production → Master data versioning
This function activates the versioning of production master data. It cannot be deactivated when a production line item version is created (a new version of an existing routing is created for instance). More information about master data versioning can be found in the article Master data versioning.
Customizing → Production → Service bill of material (BOM)
If this function is active, the service bill of material will be generated automatically on the basis of production orders for the production line items that are relevant from the maintenance point of view.
Settings tab
Time point of the creation of a service BOM:
- Upon completion of the production order – a service bill of material is generated when the production order is completed
- Upon the first receipt of the production order – a service bill of material is generated when the first item necessary to process a production order is received
- Upon printing the production papers – a service bill of material is generated when the production order vouchers are output
- Upon release of the production order – a service bill of material is generated when the production order is released
More information can be found in the article Service bill of material.