The Production order types application is used to define production order types necessary to create production orders. It includes further settings that can be customized as predefined for a specific production order type. Furthermore, data in production order types is used in the logistics and financials frameworks or to limit other organizations’ authorizations to a specific type of production order.
The application consists of:
- Query pane – in the query pane you can define the basic data for production order type.
- Work pane – in the work pane’s tabs you can enter specific information regarding inventory logistics, vouchers and external manufacturing.
- Authorization table – in the authorization table you can define the organization’s permissions to a specific production order type.
Query pane
In the query pane you can specify the basic data for a production order. Following buttons are available in the toolbar, next to the standard buttons:
[New] – adds and duplicates a production order type.
[Delete] – removes a production order and adds and removes a deletion marker. It is not possible to delete a production order type that is used by other voucher types, sales order type for instance.
Fields and parameters available in the application query pane are the following:
- Type – name of production order type.
- Description – identification of production order type.
- Number range – a number range assigned to a production order type. A number range numbers respectively production orders and is defined in Number ranges
- Production warehouse – warehouse in which a production order operation will be performed.
- Receipts/issues warehouse – the default warehouse for material reservation line items and co-product line items, provided that a warehouse is not specified in the bill of material line item and in the co-product line item.
- Issues posting key – it is assigned for transaction records purposes and is defined in Posting keys
- Order priority – defines the priority of production order. It serves as a sorting criterion in applications of Cockpit
- Scheduling category – specifies the default scheduling category for production order type. Selectable options are:
- Forward one level – order completion date is calculated on the basis of order start date. It does not include necessary production of internally manufactured semi-finished goods.
- Backward single-level – order start date is calculated on the basis of order completion date. It does not include necessary production of internally manufactured semi-finished goods.
- Forward multiple levels – order completion date is calculated on the basis of order start date. It does include necessary production of internally manufactured semi-finished goods. For this purpose, it creates additional production orders that include the production of semi-finished goods.
- Backward multi-level – order start date is calculated on the basis of order completion date. It does include necessary production of internally manufactured semi-finished goods. For this purpose, it creates additional production orders that include the production of semi-finished goods.
- Forward multiple levels in order – order completion date is calculated on the basis of order start date. It does include necessary production of internally manufactured semi-finished goods by adding them to the newly created production order.
- Backward multi-level in order – order start date is calculated on the basis of order completion date. It does include necessary production of internally manufactured semi-finished goods by adding them to the newly created production order.
- Use finite capacity – determines whether to take into consideration available resource capacities. It is deselected, by default.
- Note resource reservation settings – if selected, it is possible to use work models with data defined in the Resources application under Valuation of gaps as interruption It is deselected, by default.
- Manual order reference necessary – forces the creation of a reference to a production order line item. The reference indicates the sales voucher on the basis of which a production order was generated. It is deselected, by default.
- Multi-level dispatching according to planning data – it runs production for all semi-finished goods necessary to produce a production item. This parameter can only be used if the Demand coverage field is set to Production in Items application → Planning data section under the Planning view for a given bill of material line item. It is selected, by default.
- Automatic production reports – time point at which a process step is to be reported in the system:
- On receipt of goods from production – a production report is created when the finished product is received in the warehouse.
- On report of operation – a production report is created after the last operation is posted.
- Purchase order type – in this field you can select a purchase order type defined in Purchase order types
- Use cost unit in production – in this field you can set whether a cost unit is to be used in the production order. Selectable options are:
- As per Customizing setting – settings are retrieved from Customizing application → Controlling.
- Yes – a cost unit will be used for a given production order type.
- No – a cost unit will not be used for a given production order type.
- Reporting – time point at which a finished product is to be received in the warehouse. Selectable options:
- As per Customizing setting – settings are retrieved from Customizing application→ Production → Reportings.
- Reporting via last operation – a finished product is received in the warehouse after the last operation is posted.
- None – product is not received in the warehouse automatically.
- Time of determination of identifier – time point or production order at which identification is to be assigned to the currently produced material. Selectable options are:
- While generation the production order without abort function – an identifier is defined or generated during creation of a production order.
- While generation the production order with abort function – an identifier is defined or generated during creation of a production order with an option of aborting the production order generation.
- While reporting in receipt of goods – an identifier for a production item is defined at the time the goods are received in a warehouse in Receipts of goods application.
- When dispatching the production order – an identifier is defined or generated during dispatching of a production order.
- When releasing the production order – an identifier is defined or generated after releasing the production order.
Work pane
The settings of warehouse logistics, documentation and in-house external production are specified in the work pane.
Material procurement tab
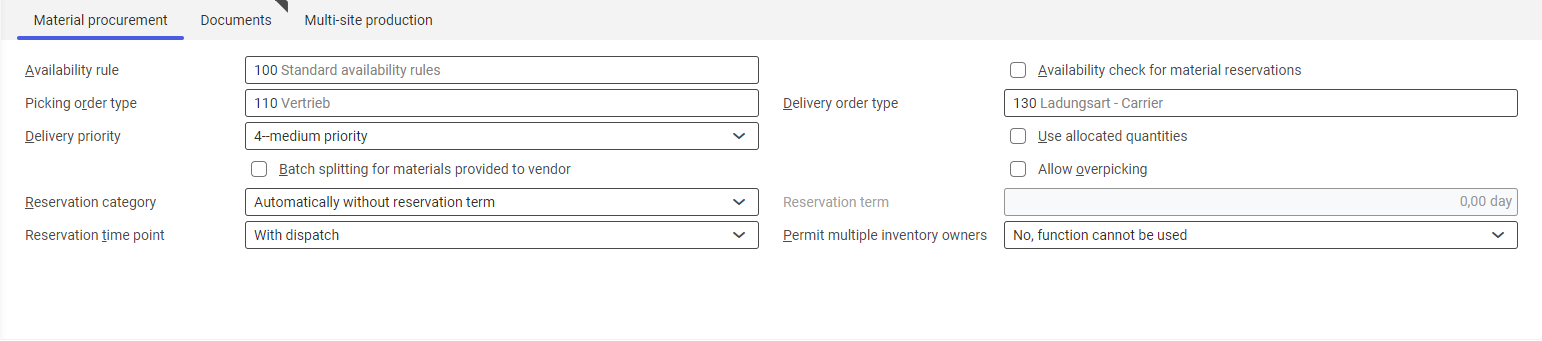
Following fields are available in this tab:
- Availability rule – type of availability rule for material reservation defined in Availability rules
- Availability check for material reservations – if selected, the system verifies the availability of materials through the action [Calculate availability] in Production orders It is deselected, by default.
- Picking order type – type of picking order, that is the movement of materials necessary for production from the components warehouse. It is defined in the Picking order types
- Delivery order type – type of delivery order defined in Delivery order types
- Delivery priority – delivery priority from 0 (the highest priority) to 8 (the lowest priority).
- Use allocated quantities – assigns material quantities to a specific production order. It activates the action [Set allocated quantities] available in Production orders It is deselected, by default.
- Batch splitting for materials provided to vendor – splits material quantities to be processed in the external manufacturing operation. It is deselected, by default.
- Allow overpicking – reserves materials above the required quantities. It is deselected, by default.
- Reservation time point – defines the time point of resource and material reservation. Selectable options are:
- With dispatch – reserves the line items when the production order is dispatched.
- During release – reserves the line items when the production order is released.
Documents tab
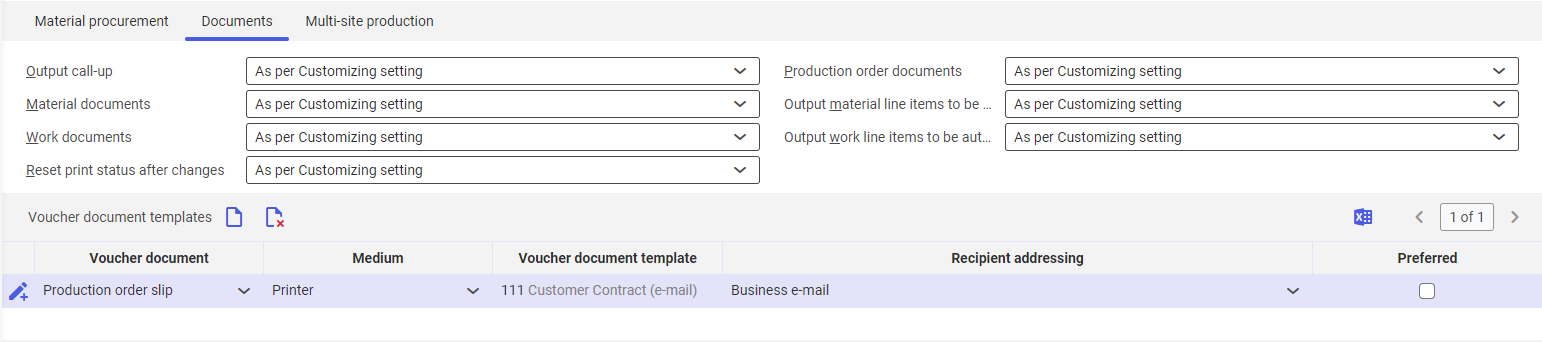
The Documents tab contains fields and a line item table in which it is possible to define a template document for a given production order type. Selectable fields are:
- Output call-up:
- As per Customizing setting – the system retrieves the document settings from the Production → Documents function under Customizing
- No print – generates production documents to a production order.
- All voucher together (default) – generates all production order-related documents as one voucher.
- Work documents individually – generates activity-related documents based on the data defined in Operations and Resources
- Material documents individually – generates material coverage-related documents based on the data defined in Warehouses
- All individually – generates all document types separately.
- Production order documents – defines which documents are to be printed from a production order action. Selectable options are:
- As per Customizing setting – the system retrieves the document settings from the Production → Documents function under Customizing
- No production order documents – does not generate production order-related documents.
- Production order slip – generates a production order slip only.
- Job ticket – generates a job ticket only.
- All production order documents – generates all production order-related documents.
- Material documents:
- As per Customizing setting – the system retrieves the document settings from the Production → Documents function under Customizing
- No material documents – does not generate documents related to coverage of materials for the production process.
- Material ticket – generates a material ticket only.
- Material list – generates a material list only.
- Output material line items:
- As per Customizing setting – the system retrieves the document settings from the Production → Documents function under Customizing
- Yes – displays in material documents all material line items defined in the production process.
- No – displays in material documents only the material line items without the automatic reporting option selected.
- Work documents
- As per Customizing setting – the system retrieves the document settings from the Production → Documents function under Customizing
- No work documents – does not generate documents related to production process activities.
- Work ticket – generates a work ticket only.
- Work list – generates a work list only.
- Output work line items:
- As per Customizing setting – the system retrieves the document settings from the Production → Documents function under Customizing
- Yes – displays in work documents all operations defined in the production process.
- No – displays in work documents only the operations without the automatic reporting option selected.
- Reset print status after changes:
- As per Customizing setting – the system retrieves the document settings from the Production → Documents function under Customizing
- Yes – in case data is changed in a production order of a given type, the output of documentation is undone.
- No – in case data is changed in a production order of a given type, the source documentation is preserved.
The Voucher document templates table in the Documents tab is handled with the following buttons and is composed of the columns below:
- [Add] – adds a new voucher in the line item table.
- [Set/remove deletion marker] – adds or removes a deletion marker for line item in the line item table. The line item is removed after the production order type is saved.
- Voucher document – in this column you can select a defined type of production voucher. Selectable options are:
- Production order slip
- Job ticket
- Material list
- Material ticket
- Work list
- Work ticket
- External manufacturing delivery
- Medium – an output medium of the defined voucher. Selectable options are:
- Printer
- Fax
- Voucher document template – in this column you can assign a template defined in the Voucher document templates application to a voucher.
- Recipient addressing – if Fax or E-mail is selected as medium, then it is possible to define the address details of the voucher recipient. Selectable options are:
- Business fax
- Private fax
- Private e-mail
- Business e-mail
- (No selection)
- Preferred – this parameter is used to select a preferred voucher type that will ultimately be added to a production order in case there are several templates defined for one voucher type.
Multi-site production tab

The Multi-site production tab activates upon selecting the Internal external manufacturing parameter and is composed of the following fields:
- Employee responsible – employee coordinating the production process.
- Return transport distribution order type – type of distribution order for return transport selected from among the types defined in the Distribution order types
- Destination warehouse for return transport – the warehouse in which the products returned from a supplier are to be stored.
- Settlement distribution order type – distribution order used for settlements and defined in Distribution order types
- Calculation type – calculation type used for cost calculation and defined in Calculation types
- Source warehouse for service – source warehouse for in-house external operation process.
- Destination warehouse for service – target warehouse for in-house external operation process.
Authorizations table
In the Authorizations table, you can grant the rights to an organization to use a given type of production order. Organization data and the authorization level are added to the table that is handled with the buttons below and is composed of the following columns:
- [Add] – adds an authorization to the table as a new record.
- [Find and add organizations] – opens a dialog window to search for and add one or more organizations to the table.
- [Set/remove deletion marker] – adds or removes a deletion marker for the line item table. The line item is removed after the production order is saved.
- Organization – an organization for which authorizations are granted.
- Own authorization – authorizations for the specified organization. Selectable options are:
- Read – the specified organization can only read a given type of production order.
- Maintain – the specified organization can use a given type of production order.
- Authorization for other organizations – authorizations granted for other organizations. Selectable options are:
- Read – other organizations can only read a given type of production order.
- Maintain – other organizations can use a given type of production order.