General information
WM (Warehouse Issue) and PM (Warehouse Receipt) documents can be created by the operator or generated automatically when approving a commercial document.
A WM document item is always related to one stock of goods. If a sales document item requires goods to be taken from different stocks, it will be split accordingly in the warehouse document. A PM document item is always linked to the delivery.
WM and PM are internal quantitative documents. They cause a change in the stock of goods in the warehouse. WM reduces the stock quantity already when the item is entered, before the document is approved. The PM only changes the stock quantity after the document has been approved. In order for the quantity received with a PM document generated by the operator to be available for sale, the PM must be linked to the commercial document.
From the context menu available on the list of WM documents, it is possible to generate commercial documents:
- Sales invoice
- Export invoice
- Internal document (FW)
- MMW (inter-warehouse) transfer
- Receipt
- Internal expenditure
- Release of deposit goods
- Stock issue
- Stock export issue
- Parcel from the indicated
- Dispatch from the indicated
The 2020.2 version of Comarch ERP XL supports calling the context menu by a shortcut: Shift + F10 for warehouse documents.
When generating commercial documents from multiple warehouse documents. The system groups the indicated warehouse documents according to the correspondence of the main contractor set for these documents. In the case of warehouse documents originating from an order, the contractor is determined on the basis of the main contractor from the order; in the case of warehouse documents registered regardless of the order, it is determined on the basis of the main contractor assigned to the contractor card, for which the warehouse document was issued.
Warehouse receipt (PM)
The Warehouse receipt (PM) documents the receipt into the warehouse. It can be generated manually by the operator, or automatically – when the commercial document is approved with the option selected: Warehouse documents – approved.
The PM is an internal quantitative document. The document only changes the stock quantity after the document has been approved. In order for the quantity received with a PM document generated by the operator to be available for sale, the PM must be linked to the commercial document.
PM, tab: General
The appearance of the tab depends on the method of document generation (manual or automatic). When generating a PM document manually, the Operator adds a document item in which he/she defines the goods, its parameters (feature, EAN, expiry date) and quantity. Then, on a separate tab of the item window, he/she can specify the placement of this item in one or more warehouse locations. The warehouse placement can be done by manual editing or by activating the warehouse placement option by the system based on the given parameters (more information about the warehouse placement can be found in the chapter: Warehouse location management).
In the second case – the automatically generated PM document – the data are copied from the commercial document and cannot be edited. In such a document, items can only be moved between the two lists before approving it. The top panel displays a list of goods whose release/receipt will be confirmed by a document. The bottom panel displays goods that are on the commercial document but will not be released/received, e.g. due to discrepancies between records and actual stock or – delivery shortages.
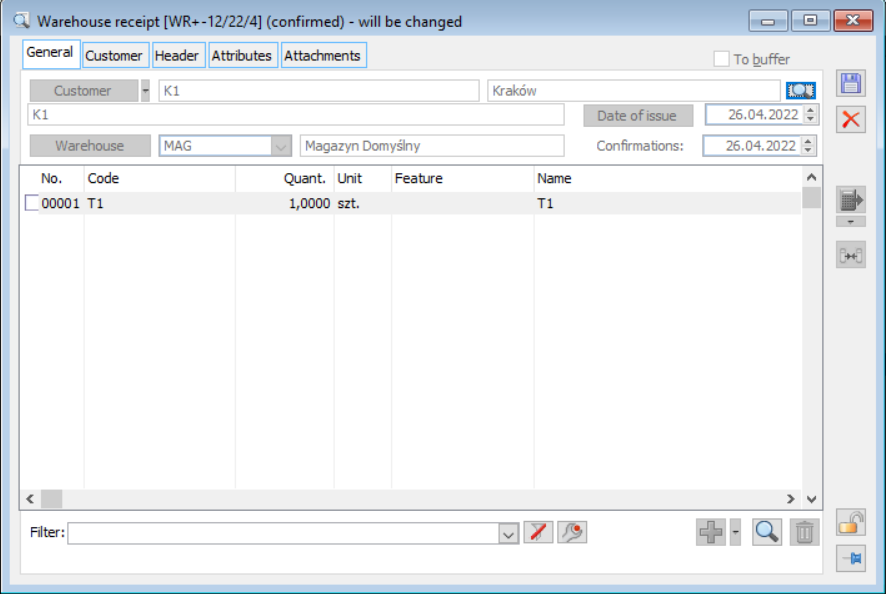
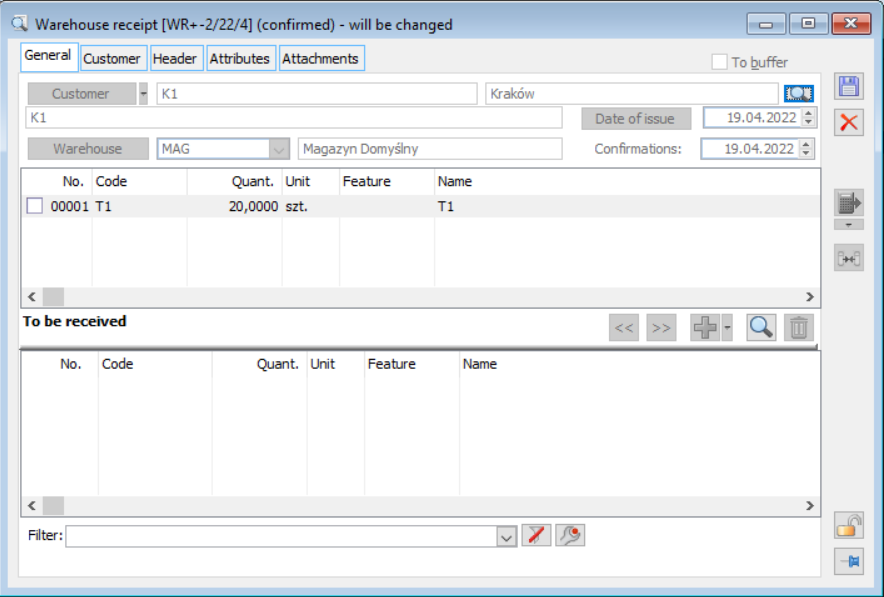
The tab contains the following functions:
Contractor – supplier of goods.
Warehouse – the warehouse to which goods are received. For an automatically-generated PM, the warehouse is unavailable for editing (also when the PM is in the buffer). For such a document, the warehouse that has been defined as the target warehouse in the definition of the centre’s document will be indicated (window: Definition of PM document, tab: Warehouses, field: Target warehouse).
Issue date – the date on which the document was issued (receipt of goods into the warehouse).
Approval date – this date has not only an informative role, but can also be the basis for setting dates on commercial documents generated from warehouse documents.
It is possible to parameterise the date setting on warehouse documents generated from commercial documents. In CDN.Konfig there is a parameter Kon_numer= -133 (date of the warehouse document from the commercial one) and if: Kon_Wartosc=0 – the current date is taken on the warehouse document Kon_Wartosc=1 – the date on the warehouse document is taken from the commercial document.
[Change] – the button allows viewing/editing the PM document item. A description of the item can be found in the chapter: The transaction item of a PM document.
[Add] – Allows adding the goods item to the document. Adding the goods item is also available by taking a reading from the collector. This is made possible by a set of functions under the button:
The button is active only on a manually generated PM document
[Delete] – removes the goods item from the document. The button is active only for a manually generated PM document.
[Add], [Delete] – buttons are active on the automatically generated PM document and only if it is in the buffer. They enable the transfer of goods between lists, as described above.
[Goods substitutes] – opens the list of substitutes of the highlighted goods in the mode:
- to be selected if the document is in the buffer
- to be previewed, if approved
The button is active if the document has items and the selected item has at least one substitute.
[Edit contractor] – allows viewing and editing the card of the main contractor.
The transaction item of a PM document, tab: General
The tab displays the transaction item data. Here, it is also possible to describe a batch of goods using a feature. Next to the feature control, a magnifying glass button is displayed with the drop-down menu , providing the options [Edit feature] – always active and [Select from list] – active only if all the conditions are met, i.e. the document is not approved, a specific feature class has been entered in the feature class control for a given value, there is no “foreign delivery” on the item and the item is not generated from or linked to a commercial document. If the PM document is in the buffer, it is also possible to edit the expiry date of the goods that are received into the warehouse (the default date is given according to the parameter setting: Mark the batch with the expiry date on the goods card on the tab: Stock/By location). However, the auxiliary unit is automatically rewritten to the PM/WM item from the commercial document or order to which it was generated.
If an auxiliary unit is selected on a PM item to which a logistic is assigned, the stock sub-items will always be in this unit, regardless of the quantity.
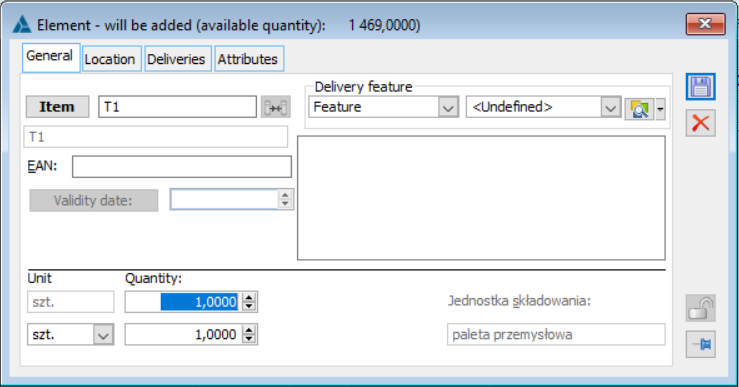
- On the document item, it is possible to use the feature of substitutes through the [Goods substitutes] icon – it opens the list of substitutes of the highlighted goods in the mode:
- to be selected if the document is in the buffer
- to be previewed, if approved
- The button is active if the document has items and the selected item has at least one substitute
The transaction item of a PM document, tab: Location
This tab allows defining the location of the goods, i.e. a specific address within the warehouse to which the consignment of goods will be accepted (provided that the addresses in the given warehouse allow the acceptance of goods in a specific storage unit and there is still space to place the goods in the address).
This location shall be indicated:
- Automatically, if the feature is enabled for the target warehouse: Warehouse location management – more in the chapter: Warehouse location management.
The transaction item of a PM document, tab: Deliveries
The tab displays information about the deliveries of goods to which attributes can be assigned.
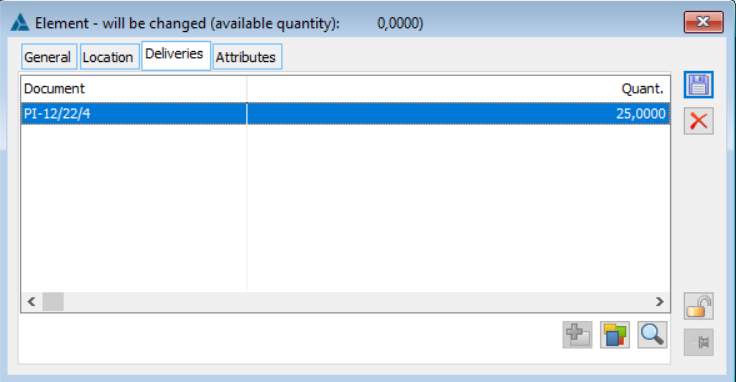
[Change delivery] – opens the list of goods delivery stock and allows selecting a delivery.
[Edit attributes] – allows attributes to be added to the selected PM document item.
[Edit delivery] – opens the Delivery window.
PM, tab: Contractor
The tab displays details of the supplier’s data, copied from the contractor’s card. The recipient can be selected by entering their acronym or choosing from a list opened by the button: . The address can be selected from the list of contractor’s addresses opened with the button:
. The current address is overwritten by default. Additionally, the name of the contractor’s bank and account number are displayed.
The data on the tab cannot be changed if the PM document was generated automatically.
[Edit contractor] – allows viewing and editing the card of the main contractor.
[Contractor address preview] – allows previewing the main contractor’s card.
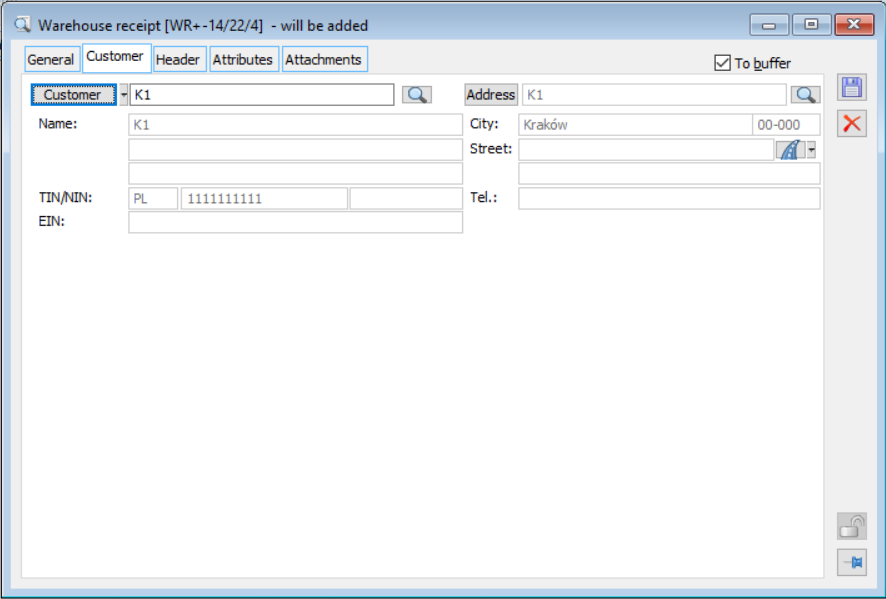
PM, tab: Header
The tab contains the header data of the document, such as the document number and series, the centre where the document was issued, the data of the operator performing the operation on the document and the description. The document can also be described by a transaction features. The transaction features are defined in the window: Configuration, from the tab: Sales/Components. The tab also contains the number of the FZ document for which the PM was generated. Using the button [Preview source document], you can open the FZ document for preview.
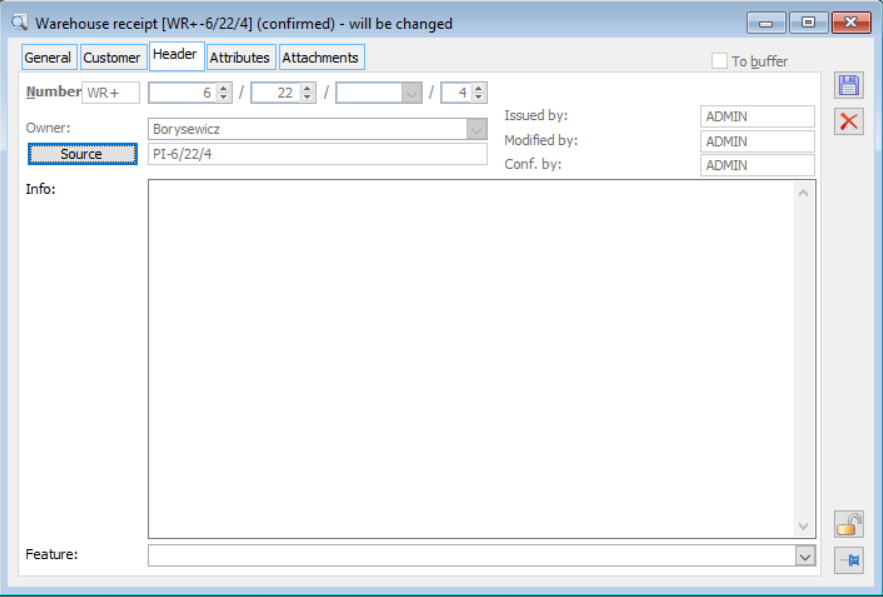
PM, tab: Attributes
The tab allows using attributes to describe a document. Attributes are added according to general rules.
Warehouse release (WM)
The WM documents the release of goods from the warehouse. The document can be generated:
Automatically
When the commercial document is approved (depending on the setting on the commercial document, on the tab: Header, option: Warehouse documents: Do not generate/To buffer/Approved)
Manually by the operator
This document is similar to the PM document, so the description will be limited to detailing the differences between the two documents.
On the WM document, on the tab: General, the contractor is indicated, which is the recipient of the goods, and the source warehouse (not the target warehouse as in the PM document), i.e. the warehouse from which the goods are to be released. For an automatically-generated WM, the warehouse is unavailable for editing (also when the WM is in the buffer). For such a document, the warehouse that has been defined as the target warehouse in the definition of the centre’s document will be indicated (window: Definition of PM document, tab: Warehouses, field: Target warehouse).
The button has a special function on WM documents, which are generated from a sales order and sales invoice: . In the case of such WM documents, the top panel will show the actual quantity on the WM, which is determined by the data entered from the collector.
Features in the collector are handled in the same way as in the WM form: If a feature is specified, only stock with that feature is loaded. If it is not specified (empty), stocks with any feature (the same, of course, because the WM item points to a batch, so the commercial sub-items must match as to the batch) are taken. No settings in the configuration or in the goods card are relevant here.
The sales order contains a quantity of 5 units of T1 goods. A WM document is generated from this order, on which the goods are entered in the same quantity as on the order. The button was then used: [Load data from the collector deleting the current list of items]. The collector has stored 4 pieces of T1 goods. After pressing the button, the WM document in the top panel (i.e. the one that determines the quantity of goods on the document) will display the quantity of goods T1 = 4 (as only such quantity was written to the collector). In the bottom panel, the remaining quantity of the order will be displayed, i.e. = 1.
The WM document, just like the PM document, includes the feature of managing the warehouse location, i.e. you can indicate a specific location (address) from which the goods are to be released. Indication may take place:
- Automatically (if the feature is enabled for the source warehouse: Warehouse location management) with the possibility of editing by the operator. When automatically indicating the location, from which a product will be taken, the priority, with which the product is taken (specified on the address where the stock is located) is taken into account (for more information, see: Defining the address type)
- Manually by the operator
When approving a WM document, the credit limit overrun is checked, but the value of the available limit is not displayed. Depending on the selection of the parameter on the document definition: Block or Allow, a message will be displayed. Warehouse release items are not included in the calculation of the value of the available credit limit – there is no value on the WM document. The limit check on a WM document aims to check whether the limit was exceeded before the document was issued.
A Domestic external export issue or a Domestic export invoice can be generated for a Warehouse release generated from a Domestic sales order. This is possible if the Transaction type is Domestic and the VAT rates are Domestic.
From the context menu available on the list of PM documents, it is possible to generate commercial documents:
- Purchase invoice
- Flat-rate farmer VAT invoice (VAT RR)
- Internal receipt
- Receipt of deposit goods
- Received note
- Import received note
- Parcel from the indicated
- Dispatch from the indicated
It is possible to parameterise the date setting on warehouse documents generated from commercial documents. In CDN.Konfig there is a parameter Kon_numer= -133 (date of the warehouse document from the commercial one) and if: Kon_Wartosc=0 – the current date is taken on the warehouse document Kon_Wartosc=1 – the date on the warehouse document is taken from the commercial document.
WM transaction item
The WM transaction item is similar to the PM document transaction item. On the general tab, the goods to be released and their quantity shall be indicated. It is also possible to indicate the features of the goods to be released.
A magnifying glass button is displayed next to the feature control with a drop-down menu providing the options [Edit feature] – always active and [Select from list] – active for “delivery feature” only if all the conditions are met, i.e. the document is not approved, a specific feature class has been entered in the feature class control for a given value, the item is not generated from the sales document or linked to it; active for “delivered feature” only if all conditions are met, i.e. the document is not approved, an option other than Sale/Stock option has been selected for the feature, a specific feature class has been entered in the feature class control for a given value.
On the tab: Location, the location (address) from which the goods will be released is indicated. As mentioned above, this indication may be automatic or manual. On the tab, another warehouse location may be indicated (automatically – using the button: or manually, using the button:
) and add a stock from the indicated location (using the button:
). Similarly to the transaction item of the PM document, for the selected stock, it is possible to display the data of the address where it is located, provided that the stock has an assigned location in the warehouse. The address is previewed by selecting it on the tab: Location, stock, and press the button:
[Address preview].
On the tab: Deliveries, information on the deliveries that created the stock for the goods to be released is displayed.
Intra-warehouse transfer (MP)
An intra-warehouse transfer document is used to move goods between locations within a single warehouse.
The document is handled in the following way: an item is added to the MP document, in which the goods and their parameters (EAN, feature, expiry date) are specified. Next, select the stock from which the goods are to be taken, edit the quantity, and select the destination address.
The list of MP documents is in the window: List of commercial documents, on the tab: Warehouse/MP.
If there is a stock reservation, it is possible to issue an MP that moves the stock between locations.
MP, tab: General
On the tab, the warehouse within which the transfer is to be made is indicated and the document item is added. This is done using fields and functions:
Warehouse – the field indicates the warehouse within which the goods are to be transferred between locations.
Issue date – the date on which the document was issued.
Approval date – this date has not only an informative role, but can also be the basis for setting dates on commercial documents generated from warehouse documents.
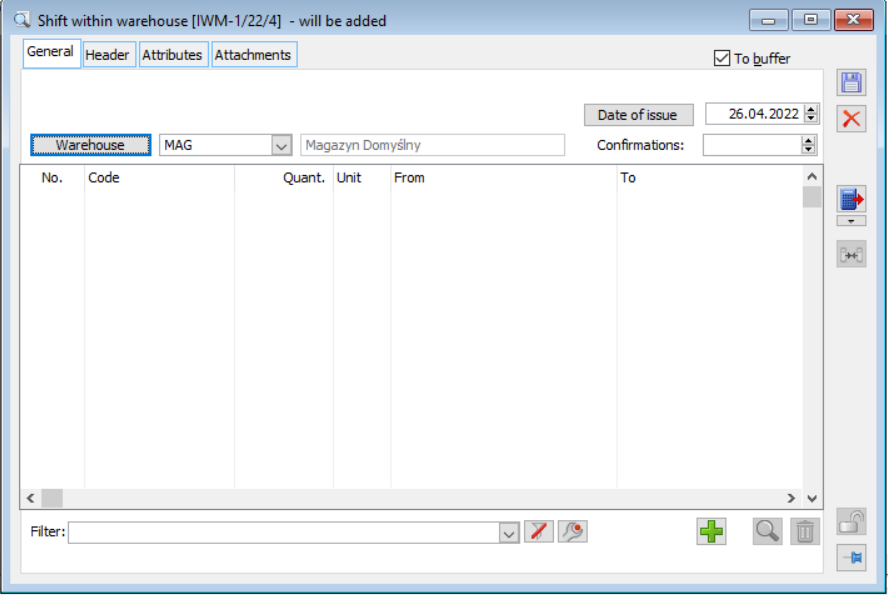
[Add] – used to add an item to a document.
[Change] – allows opening a document item for viewing/editing.
[Delete] – used to delete an item from a document.
MP transaction item
The transaction item indicates:
– when pressed, the list of stock that meets the criteria indicated in the other fields of the MP transaction element is displayed. The stock from which the transfer is to be made is selected by checking it and pressing the button:
[Select].
– when pressed, the list of locations (addresses) within the warehouse is displayed (window: Warehouse structure), where the destination of the goods to be transferred should be indicated.
– the code of the goods to be transferred is entered in the field.
Feature – the stock list from which the goods to be transferred are selected can be narrowed down according to the feature with which the goods were received into the warehouse (feature indicated on the PM document). There is a magnifying glass button with a drop-down menu next to the feature control.
Menu options:
[Edit feature] – always active, opens the Feature form where editing is possible on a non-approved document.
[Select from list] – active on a non-approved document if a specific feature class is specified on the item.
EAN – similarly to the feature, it enables narrowing (according to the EAN code criterion) the list of stock that can be transferred using a specific MP document.
Expiry date – the expiry date of the goods to be transferred (for more information on the expiry date, see the description of the goods card, Tab: Stock/By location).
Unit and quantity – the quantity of goods in a given unit in which the goods are to be moved.
Storage units – the fields indicate the units in which the goods were stored at the source location and in which they will be stored at the target location (e.g. after repacking).
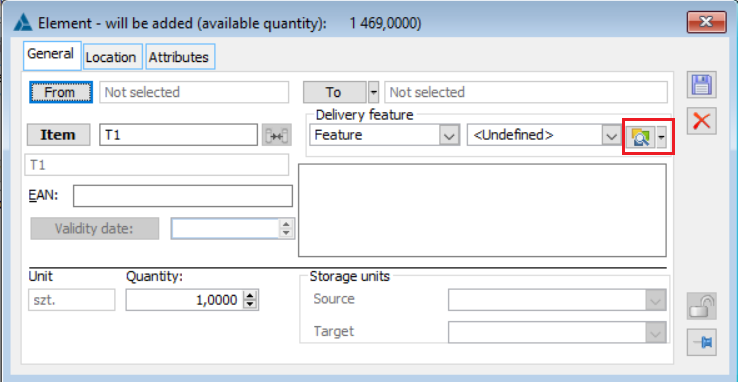
The transaction item can be described with attributes.
MP, tab: Header
The tab contains the header data of the document, such as its number and series, the indication of the centre where it was issued and the operator who made changes to the document. The document can be provided with a description and a transaction feature (selected from the dictionary defined in the configuration, on the tab: Sales/Transaction features).
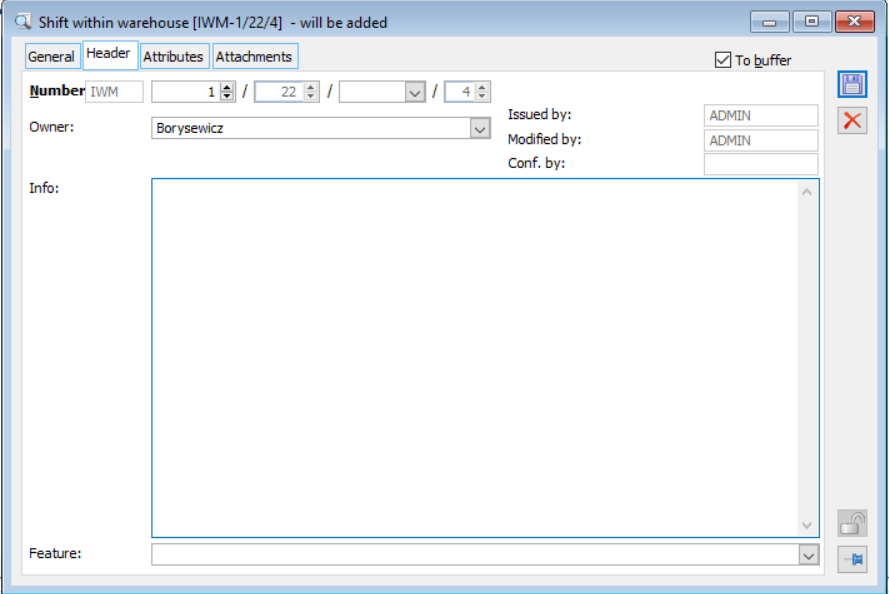
MP, tab: Attributes
The tab allows describing the document with attributes. To make this possible the attribute class must be assigned to the object: [Warehouse documents].[MP].